Featured Stories
-
Elevating Pouch Manufacturing with Pearl Technologies' Cutting-Edge Solutions
For manufacturers seeking efficiency, precision, and safety in pouch production, Pearl delivers unmatched innovation across three standout... -
Faster Product Composition Analysis Equals Better Quality Assurance
Near Instant Testing and Reduced Costs to be Found -
Methods to Precisely Measure Tension and Web Control
How to Control Automatically Within Set Parameters
News | New Products
-
Convertech Brand to Fully Transition to Double E Group Same Team, Same Excellence, Unified Name
Double E Group has announced that Convertech, one of its subsidiaries and a trusted provider of core chucks and shaft solutions for the converting industry, will now operate solely under the Double E Group brand.
-
Pulse is Making Print Simple at Labelexpo Europe 2025
Narrow web ink specialist Pulse is Making Print Simple at Labelexpo Europe 2025, as it challenges flexo printers to rethink how they work and shows solutions that turn production bottlenecks into revenue generators.
-
ROTOCON to debut at Labelexpo Europe with three machine demonstrations
ROTOCON will make its Labelexpo Europe debut, exhibiting together with HS Machinery on stand 4D21.
-
At Interphex Japan, IL Group to Showcase Innovative Labeling Solutions and Contract Packaging Services
IL Group, a specialist in multifunctional labeling solutions for the pharmaceuticals and healthcare sectors
-
Revolutionizing Adherence: Clinical Trials Go Digital with Enhanced Key-Pak®
Keystone Folding Box Co., a leading provider of paperboard packaging solutions, has announced a strategic partnership with Med-Con Technologies
-
Innovating for Circularity: How New Sustainability Initiatives Are Shaping the Future of Labeling
In the face of growing regulatory, environmental and consumer pressures, the packaging and labeling industry continues to advance technologies and solutions that help to support a circular economy.
-
New Product Development: RKW Horizon®–MDO-PE Films with EVOH Barrier
RKW Horizon® is the new generation of sustainable PE plastic films based on the latest MDO technology.
Expert Advice
Converting Outlook | Flexo Is On The Go For 2018
- Published: May 17, 2018, By Susan Stansbury
Flexographic printing is a standout converting process. Flexo is the step that precedes processing from labels to lidding, from pouches to packages of every configuration...and so much more. This category continues to grow. The global printing industry is forecast to reach $980 billion this year, according to Smithers Pira, and it will be driven by growth in segments that include packaging and labels.
An optimistic outlook is also echoed by the Converting Solutions community. Growth last year and this year is the best in the last few years, according to Adrian Fordham, president of MoistTech Corp., an industry supplier. “We see considerable growth,” says Fordham. The flexo industry supply chain starts with machinery, materials, inks and then when it’s doing well, secondary suppliers involved with process improvement, like MoistTech, see growth too. “Right now, Flexo, converting and coating producers are showing very good results.”
In 2018, a key focus is on efficiency and evolving tech- nology for super-fast and high-quality, colorful results. For example, today’s water-based inks mean that moisture measurement and control are critical in-process as well as during windup where the web requires adequate dryness levels to avoid sticking. In this case, MoistTech’s measure- ment systems allow for moisture control and management of ink laydown thickness.
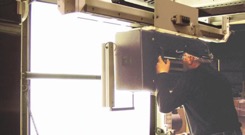
Press equipment manufacturer Retroflex, Inc. also sees the outlook for flexo as bright and including investment in add-ons. “While complete flexo printing line sales con- tinue to be strong, we also see a big increase in our clients wanting to add on-press sleeve changes and full servo operation features to new downstream units and to new 1, 2, 4 and 4 color flexo presses,” says Perry Lichon, Retroflex president. “Once only available on larger 8- and 10-color presses, we now offer these time and money saving features for nearly every flexo operation. This is allowing even the small print houses to experience the quick job change advantages that at one time only the larger shops had access to. Overall this is helping to fur- ther the growth of flexo.”
Whether it’s single-color or 10-color flexographic printing, industry insiders say there are many avenues to raise the game in-house and for each intended market segment. With the latest market demands for ever-better printing, reviewing basics and advancements are part of the solution.
Very thin film and substrates with highly irregular surfaces continue to be a challenge seen by Retroflex and others. Says Lichon, “In most cases—and thin films, in partic- ular—challenges can be solved or greatly reduced by get- ting back to basics. First and foremost, of course, you must make sure that the equipment (press, winders, etc.) you are working with are actually designed and capable of per- forming the functions you are expecting of them.”
Lichon notes basics such as dyne levels, proper tension, overall tension control, anilox selection, plate/cushion selection, appropriate dryer/curing settings, chilling, ink viscosity, nip pressures and some other items continue to be overlooked. He says, “just because the equipment is state of the art, failure to verify and check the basics can trip up a multimillion-dollar investment.” Many problems can be overcome, “not by making some high tech never- before-heard-of adjustment, but rather by just getting back to basics.”
Our industry contacts emphasize that the equipment end user should work with all of their suppliers to be sure the best solutions are being used, and used correctly, for each individual application. Lichon says, “A case in point, trying to print waxed paper at 2000 fpm: Working with a number of the suppliers has now allowed our client to reach speeds of 3000 fpm.” Look at your basics first, he emphasizes. Ultimately, flexo is often the converting industry’s aesthetic solution that turns consumers’ heads. It offers product and package designers the best of head-turning beauty as well as problems solved with unique combinations of sub- strates, coatings and inks.
Contact Company