Web Lines | Action Plan for CD Buckles, Part 3
- Published: July 05, 2017, By Tim Walker
Mechanisms, descriptions, and remedies for your cross direction buckles.
In Part 1 of our Action Plan, we looked at the reasons why cross direction buckles form. In Part 2, you'll find remedies for CD buckles starting at the core. Part 3 addresses remedies for CD buckles moving outward from the core.
Mechanism 4: Full Width CD Buckles
Description—In winding with low tension and strains, core shrinkage, escaping wound-in air, or other radial dimensional losses can shift the entire roll into MD compression and CD buckles. In the most dramatic cases, the entire roll sags into an egg shape.
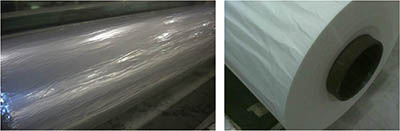
Remedies:
- Apply all the remedies of Mechanisms 1-3.
- Increase initial tension and strain of all CD buckling layers with more torque or nipping.
- Minimize material or process conditions that cause layers within a roll to lose thickness and decrease radial position over time, including coating, laminate layers, and surface roughness or features. Mechanics of thickness loss include: air compressing, air escaping, adhesive oozing, tissue or porous films compressing, hot roll winding cooling, and post-polymer processing density increases.
Mechanism 5: Partial Width CD Buckles
Description—Lanes of CD buckling will form in the wound roll where the web or coating thickness is below average in the same lateral position for many layers.
Partial width CD buckles are full width CD buckling mechanism appearing first where poor thickness profile creates locally softer regions.
The layers under the thin lanes have lower stack modulus and more easily compressed, relieving their MD tension, and with enough radial change, go into hoop compression and buckling.
In blown films, where the thickness profile is rotated with the collapsing bubble, buckling defects may follow the low thickness bands as they move across the roll.
Remedies:
- Apply appropriate remedies of Mechanisms #1-4.
- Reduce crossweb thickness variations, especially thickness profiles that are asymmetrical (one side thick, one side thin) or create "valleys" where two thick gauge bands have a band of average or below average thickness between them.
- Reduce diameter variations created by thickness variations with lower stack modulus, either by product design, lower winding tensions, or more entrained air. (Stack modulus can be reduce with greater porosity, increased roughness, lower winding tension, more entrained air, compliant coatings, and soft interleave webs.
- Oscillate thickness variations by CD shifting flat processes or rotating blown processes.
- Maximize the winding nip’s ability to conform around roll diameter variations. For "hard" rolls (films and foils), use a compliant nip roller (30A-45A Durometer, ¾ to 1-in. thick). Minimize core eccentricity.
MECHANISM 6: Buckling in Self-wound or laminated adhesive products
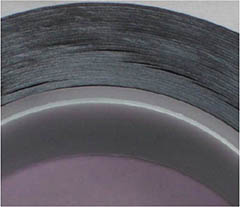
Description—Flow or shrinkage of adhesive layers, especially thick or low viscosity adhesives, can form CD buckles near the core, throughout the entire roll, in low thickness bands.
In smaller build-up self-wound PSA products, since the layers are bonded together with adhesion and gravity is a smaller factor, extreme loss of tension will not lead to sagging or egg-shaped rolls, instead forming buckling throughout the roll.
In narrow PSA rolls, the CD buckling may tunnel through the roll’s entire width, creating air gaps through the roll and peaking or "humps" at the outside of the roll.
Remedies:
- Apply appropriate remedies of Mechanisms #1-5.
- Reduce thickness change in adhesive layer through formulation change, reduce thickness, storing the rolls in a cool environment, or reducing the storage time.
Web handling expert Tim Walker, president of TJWalker+Assoc., has 25 years of experience in web processes, education, development, and production problem solving. Contact him at 651-686-5400; tjwalker@tjwa.com; www.webhandling.com.