Static, Be Gone!
- Published: November 01, 2009, By By Dr. Kelly Robinson Contributing Editor
Static charge accumulates on the surface of PE, PP, or PET films as they run through a coating, lamination, or converting process. Static charge also accumulates on the surfaces of insulating rollers covered with polyurethane, silicone rubber, or EPDM (ethylene-propylene-diene) rubber. Dissipating roller charge is important because charged roller surfaces attract dust particles, cause sparks to the grounded roller shafts, and may pose shock risks to personnel that clean the roller surfaces after a long run.
Using rollers covered with static dissipative or resistive materials will dissipate static effectively. What is the maximum roller resistivity for your application?
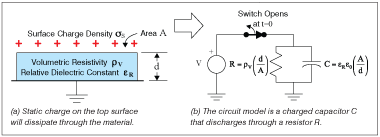
The volumetric resistivity (ρv) of a material determines how fast static charge dissipates. Figure 1(a) shows a slab of thickness (d) and surface area (A) with static charge on the top surface. Static charge dissipates faster from materials with lower resistivity. From the circuit model shown in Figure 1(b), the charge dissipates exponentially and the RC time constant of the circuit is given in Equation 1.
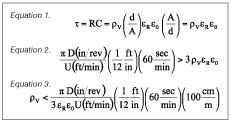
This is an important and an amazing result! The charge relaxation time (τ) does not depend on the thickness (d) or the surface area (A) of the material. The charge relaxation time depends only on the volumetric resistivity (ρv) and relative permittivity (εR) of the material. The parameter (ε0) is the permittivity of free space, which is a universal constant.
To determine the upper limit on roller resistivity, we need the roller charge to dissipate within one revolution. Taking the dissipation time to be 3τ so that 95% of the charge will have dissipated results in Equation 2.
And solving for the maximum roller resistivity gives Equation 3.
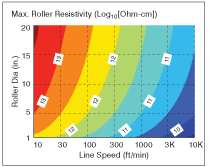
The maximum roller resistivity as a function of roller diameter and line speed is shown in Figure 2.
For higher line speeds, the resistivity must be lower so that charge on the surface of the roller will dissipate more quickly. For example, if the line speed increases from 300 fpm to 1,000 fpm, the maximum resistivity for a 5-in.-dia roller decreases from about 3 × 10+11 to 1 × 10+11 ohm-cm. Also, at a given line speed, larger diameter rollers turn more slowly so that the maximum resistivity is somewhat higher for larger rollers.
It is important to dissipate the static on rubber- or polymer-covered rollers to minimize contamination and prevent sparks. Using static dissipative materials is an excellent way to get rid of roller static. The key to achieving good performance is selecting a static dissipative material with a volumetric resistivity that permits the static to dissipate within one roller revolution.
Please contact me if you have any questions on this article. Also, please let me know if you would like me to cover a specific topic in a future Static Beat column. My contact information is below.
Static control expert Dr. Kelly Robinson, president of Electrostatic Answers, has 27+ years of experience in problem-solving and consulting. Contact him at 585-425-8158; kelly.robinson@electrostaticanswers.com; www.electrostaticanswers.com.