Static Beat | Use Static Splices with Metallized Films
- Published: May 22, 2018, By Kelly Robinson
Static splices suppress sparks from metallized webs and films with conducting traces when splices pass over metal rollers.
Films with metallized layers and conductive traces are important because metallized layers provide excellent barrier properties and conductive traces enable electronic functionality. Metallized ribbons increase security of many financial certificates and currencies. However, these high value conductive layers and traces complicate our roll-to-roll operations by causing sparks when splices pass over metal rollers. These sparks have ignited fires when splices pass through solvent coaters.
Ground conductive layers to suppress sparks. When metallized layers are exposed, touching metal idler rollers grounds the conductive layers. Designing products to have “Safe Edges” (see Static Beat | Static Control for Films with Conductive Layers) is the most reliable way to suppress sparks. For products that lack safe edges, we can use “Static Splices” to suppress sparks from splices.
To see how sparks occur at splices, let’s look at the metallized film in Figure 1 where the metallized layer will be coated with an adhesive prior to lamination. The BOPP or PET film is wider than the metallized layer so that the edges have no metallized layer. For this product, the adhesive coating is wider than the metallized layer so this product does not have a safe edge (see Static Beat | Static Control for Films with Conductive Layers). The metallized layer is fully encapsulated by the adhesive coating.
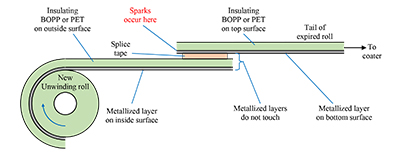
Prior to coating, the metallized layer is grounded by touching metal idler rollers. However, once the splice passes over the last metal idler that touches the metallized layer prior to coating, the metallized layer becomes ungrounded. The splice prevents the metallized layer in the tail of the expired roll from touching the metallized layer in the new roll. The idler rollers in the dryer touch the uncoated side, and once the adhesive cures, the metallized layer is fully covered. The ungrounded metallized layer is now prone to charging, and sparks may occur as the splice in Figure 1 passes over metal rollers.
One way to suppress sparks at splices is to ensure that the metallized layer in the tail of the expired roll touches the metallized layer in the new roll. Splices that accomplish this are "Static Splices." The leading edge of the web on the new roll is folded to make the static splice in Figure 2 that allows metal-to-metal contact. The challenge is to both make this splice strong and make a splice that allows metal-to-metal contact.
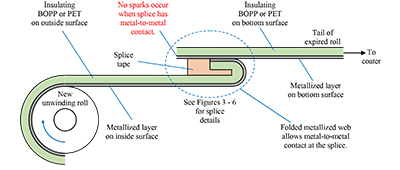
To prepare the 12-in. static splice in Figure 3, apply splice tape as usual to the 8-in. splice area. Extend the splice tape about a half tape width into the 4-in. fold area. Next, apply two more strips of splice tape that will secure the folded web. Apply the first strip at the leading edge of the 4-in. fold area. The second strip is half way between the leading strip and the large, 8-in. splice area. The gaps on either side of the second strip should be about a tape width plus ¼ in.
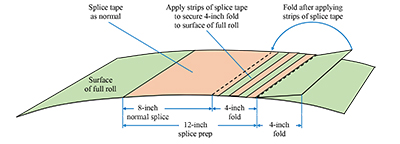
Fold the 4-in. section of the leading edge of the web of the new roll in Figure 4 onto the strips of splice tape. The splice tape should secure the folded web.
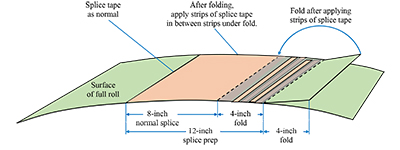
Finish the static splice in Figure 5 by applying two more strips of splice tap on top of the folded web so that the metallized layer remains exposed. Apply the two additional strips of splice tape in the gaps between the strips under the web.
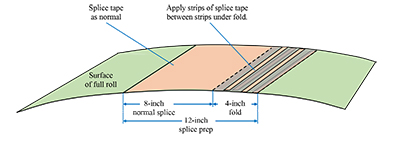
The cross section of the static splice in Figure 6 shows that metal-to-metal contact between the expired web and the new web is achieved by folding the new web onto the splice. The metal-to-metal contact suppresses sparks as the static splice passes over metal rollers.
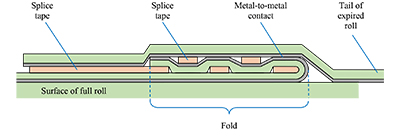
Metallized layers have many benefits including providing excellent barrier properties. Conducting traces on films enable electronic functionality and valuable security features. Using static splices ensures that sparks are suppressed as the splice passes through solvent coaters.
Feel free to contact me if you have any questions or if you would like additional information. My email address is Kelly.Robinson@ElectrostaticAnswers.com.
Static control expert Dr. Kelly Robinson, president of Electrostatic Answers, has 27+ years of experience in problem-solving and consulting. Kelly writes PFFC's Static Beat column and the Kelly on Static blog. Contact him at 585-425-8158; kelly.robinson@electrostaticanswers.com; www.electrostaticanswers.com.