Static Beat | Control Static on a Winding Roll
- Published: November 08, 2017, By Kelly Robinson
Suppress static sparks on winding rolls to protect operators from shocks, release layers from damage, and labels from blocking.
Static sparks on a winding roll can shock operators, damage thin coatings such as release layers, and deposit spots of static that can cause stacks of labels to block. To suppress sparks on the winding roll and to have low static when the roll is unwound in the next operation, make certain that the web entering the winding roll is as charge-free as possible.
However, even with good charge control upstream of the winder, the web entering the winding roll will carry some static. This small amount of static accumulates in the winding roll causing sparks.
The best practice is to install a static bar on the winding roll to suppress sparks. Good static control upstream of the winder is the key to having low static when the roll is unwound. Make sure that the web entering the winding roll is as charge-free as possible.
Let’s suppress sparks on the winding roll in Figure 1 and make sure that it has low static when we unwind it in the next operation. To effectively control static, keep track of which web surface carries static charges.
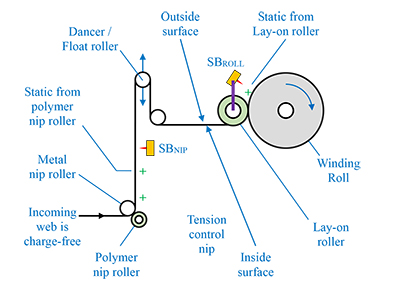
The web entering the winding roll has two sides. The outside surface is exposed on the winding roll. This inside surface is the other surface. Static bar SBROLL deposits neutralizing charges on the outside surface, so the inside surface of the web entering the winding roll must be static free.
This winder has 3 important elements:
- a nip to control with winding tension,
- a dancer (float roller) to control with winder motor, and
- a lay-on roller to improve wound roll quality.
Initially, to keep things simple, we’ll assume that we’ve done a good job controlling static upstream of the winder and that the web entering the tension control nip in Figure 1 is charge-free.
Nip rollers can deposit a large amount of static on the web. And, we know that the static will be on the web surface that touched the polymer nip roller. For the winder in Figure 1, this is the inside surface, so we must dissipate this static before the web enters the winding roll.
The best practice is to locate active static bar SBNIP in Figure 1 on the web span exiting the tension control nip facing the web surface that touched the polymer nip roller. With SBNIP, the web entering the dancer is nearly charge-free.
Dancer (float) rollers normally deposit only small amounts of static on webs. When roller alignment is imperfect, sliding contact with the roller charges the web. The static charges deposited on the web by the dancer in Figure 1 will be on the bottom or inside surface of the web. Check to be sure that the roller is well aligned to ensure that the inside web surface in charge-free.
A lay-on roller often is used on a winding roll to improve winding. The lay-on roller also deposits static charges on the web surface that touches the roller, which is the outside surface. The best practice is to locate active static bar SBROLL to dissipate static on the outside surface of the winding roll. The bracket holding SBROLL may be attached to the lay-on roller frame so that the static bar moves with the lay-on roller.
Static bar SBROLL in Figure 1 achieves our first static control goal of suppressing sparks on the winding roll. SBNIP and good alignment of the dancer roller achieves our second goal of having low static when the roll in unwound in the next operation.
I invite you to ask questions about this column and to suggest future topics. My email address is: Kelly.Robinson@ElectrostaticAnswers.com.
Static control expert Dr. Kelly Robinson, president of Electrostatic Answers, has 27+ years of experience in problem-solving and consulting. Kelly writes PFFC's Static Beat column and the Kelly on Static blog. Contact him at 585-425-8158; kelly.robinson@electrostaticanswers.com; www.electrostaticanswers.com.