Playing the Wrinkle Blame Game
- Published: July 01, 2009, By By Timothy J. Walker Contributing Editor
Imagine you are an unwind operator. You unwrap the next roll of input material, splice it into the machine, and hit the run button. Then you see them — wrinkles.
Wrinkles. Isn't that enough to get your attention? Of all the topics of web handling, only winding defects grab the attention of converters more than wrinkles, especially anyone venturing into thinner, wider, or stiffer webs. Wrinkles mean waste.
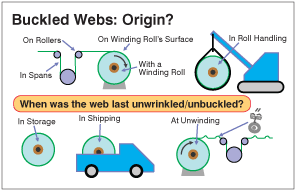
The first step in fighting wrinkles is to find the source. As the unwind operator, there likely isn't much you can do at the slitter to stop the wrinkles. Your first instinct is to blame the supplier or upstream process for the wrinkle waste at your unwind.
To start the blame game, let's review where wrinkles can be created. Moving from where you see wrinkles in the slitter back to the birth of your web, here are the possible sources of wrinkles:
-
Option 1 | Blame the supplier or upstream process. Wrinkles are created between rollers (in spans), on rollers by the supplier or upstream process, or at the outside of the winding roll where the roll is wound. In all these cases, the supplier or upstream process had a solid chance to detect and eliminate (or at least flag) the wrinkles.
-
Option 2 | Blame the source with some empathy. If wrinkles are forming within the roll during winding, handling, or storage, it's not your fault, but it isn't a case of straightforward negligence by the supplier either. Wrinkles and other buckled web defects with rolls are difficult to detect without unwinding the roll (so it's likely you are seeing them first). The fault may lie in many areas.
-
Wrinkles or buckled defects created within rolls, like most winding defects, are complicated to fully understand but form in the perfect storm of material, equipment, and process sins. If the core is too soft or collapses, the layers near the core will buckle. If the product changes over time, relaxing or shrinking, then buckles may form in the roll. If the process conditions form a wrinkle during roll starts, if the winding nip loses contact, if the tension is upset, if taper tension is wrong, then buckles may form within the roll. If you do everything right, but your crossweb thickness or density profile is poor, the web may buckle in the soft lanes.
Looking at this list, it's surprising that all rolls don't have some buckling defects within them.
-
Option 3 | Blame yourself (slitter unwinding and handling). If the product is wrinkle-free within the supplied roll, and you create wrinkles at unwinding or handling over your rollers, then don't blame the roll's supplier. You might be handicapped if their bagginess is too high (another defect that usually develops within the roll), but if you turn a crease-free and wrinkle-free web into waste, cast not the first stone. I've seen at least one case where wrinkle waste was blamed on the supplier, but it was caused by a nipped roller at the slitter unwind. After months of blaming the supplier, when the converter was proven to be the wrinkle source, it would be an understatement to say they were beside themselves.
What to do after playing the blame game? Grow up. It's a good idea to check through this list before making an angry phone call to the roll's supplier. It should be clear that there are various levels of incrimination.
Suppliers and their customers need to be partners. The blame game is about absolving yourself from blame, but that's not a realistic approach. Whatever the source, observation and feedback from the unwinding process is a critical step to eliminating your wrinkle waste. You and your supplier should work side-by-side to find the source of the wrinkles, identify the cause, and work toward a remedy.
Web handling expert Tim Walker, president of TJWalker+Assoc., has 25 years of experience in web processes, education, development, and production problem solving. Contact him at 651-686-5400; tjwalker@tjwa.com; www.webhandling.com.