How Much Misalignment Is Trouble?
- Published: February 01, 2009, By By Timothy J. Walker Contributing Editor
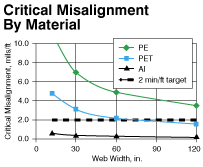
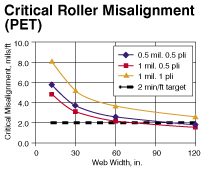
Shear wrinkles are the most common wrinkle mechanism, forming a diagonal crease and appearing to walk across rollers like an inch worm. The way to create a shear wrinkle is to increase the misalignment of a well-wrapped roller until shear stresses within the bending web lead to buckling and a gathered wrinkling web on the misaligned roller. Shear wrinkles have three prerequisites:
-
a mechanism that causes the web to bend between span, usually roller misalignment, but other possibilities include roller diameter variations or web lateral shifting;
-
sufficient friction to bend the web;
-
sufficient friction to hold the web in a buckled, wrinkled shape on the roller.
Roller misalignment by itself will not wrinkle a web without sufficient friction to meet the second and third requirements. If a roller has low friction or traction relative to the web due to low tension, lubricated traction, or a small wrap angle, wrinkles are less likely to form. If the web span is difficult to bend, such as short spans or thicker, wider webs, wrinkles may not form. Since total friction is proportional to web width, narrow webs may not have sufficient friction to meet the third requirement.
I always recommend including roller alignment in any equipment specification, usually advising 2 mils/ft of width. However, in many cases your web is insensitive to 2 mils/ft of misalignment.
The graphs show for various web widths (the X-axis) how much misalignment (the Y-axis) is required to create a shear wrinkle. Any roller with misalignment below the curve would be wrinkle free. Each case is analyzed at the theoretical worst case when span length is 40% of web width.
The first graph shows three materials, each at 1-mil thickness and 1 PLI. For example, at 60 in. wide, the critical misalignment for PE, PET, and aluminum is 5, 2, and <1 mil/ft respectively. What isn't shown is that aluminum probably won't wrinkle at 12 and 30 in. wide because there isn't enough friction between a web and roller to reach the stress required to buckle the curved aluminum. PET and paper webs are a worst case scenario, stiff enough to be sensitive to small misalignments, but not so stiff they can't be buckled with the traction available.
The second graph is for three cases of PET shear wrinkles starting with 1 mil and 0.5 PLI but also showing the effect of moving to 0.5-mil thickness or 1 PLI tension. Increasing the tension of 1-mil PET from 0.5 to 1 PLI almost doubled the critical misalignment, showing the benefit of tension stiffening. Keeping constant stress or strain, you can see 1-mil PET at 1 PLI is less wrinkle sensitive than 0.5-mil PET at 0.5 PLI, showing the benefit of increasing thickness. It is often stated wrinkle sensitivity goes up or down with thickness-cubed based on untensioned beam theory; this is clearly not accurate for tensioned thin-shell buckling.
These graphs give insight into critical variables, but don't use these curves to justify loosening your roller alignment spec to less than 2 mils/ft. Why not? Wrinkle causes rarely come one at a time. If you combine other contributors, such as imperfect webs, deflecting rollers, tension variations, and roller deflection, you'll find a 5x or 10x safety factor in roller alignment is the only good approach to a wrinkle-free process.
Web handling expert Tim Walker, president of TJWalker+Assoc., has 25 years of experience in web processes, education, development, and production problem solving. Contact him at 651-686-5400; tjwalker@tjwa.com; www.webhandling.com.