Get a Grip on Your Web
- Published: November 01, 2009, By By Pete Eggen, Webex Inc.
Whether a converter needs to isolate tension at various zones in a web line, reduce web slippage over a roll, or pull the web at increased speeds and with greater operator safety, vacuum rollers can solve these web handling needs with unique traits not found in nip rollers or “S” wraps.
Vacuum rollers are designed to pull the web into intimate contact with the roll, preventing web slippage in either direction. The result is a highly effective web control device that can handle a wide variety of web tensions and tension differentials.
For companies such as Arkwright and Green Bay Packaging, vacuum rollers are the gold standard in ensuring quality product. (Arkwright produces coated paper and film for the reprographics industry. Green Bay Packaging produces pressure-sensitive laminated structures for the roll label industry.)
Analysis of a Vacuum Roller
There are two essential elements of a vacuum roller:
- A rotating shell with a special surface through which air can pass
- An engineered pathway to evacuate air from inside of the shell
In addition, each roller is designed with a specific vacuum zone that approximates the area of web wrap. Internal seals surround the vacuum zone to help ensure air flow efficiency and minimize air flow noise.
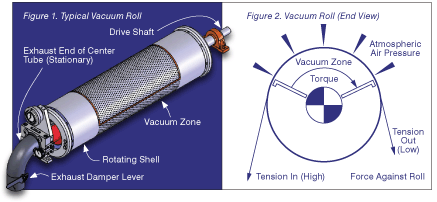
In a typical vacuum roll (see Figure 1), the rotating shell is driven around a stationary center tube that evacuates air. Figure 2 shows the stationary vacuum zone established within the shell. The vacuum zone angle/area is slightly less than the web wrap angle/area to help maintain vacuum (air) forces that act upon the web.
Similarly, the width of the vacuum zone along the length of the roll is slightly less than the web width. Some vacuum rolls are designed with an adjustable vacuum zone width to accommodate changing web widths.
Handling Wet or Coated Webs
A vacuum roller can provide web control while touching only one side of the web. This is especially useful in transporting or redirecting wet and/or coated webs. Nip rolls and “S” wrap configurations have limited use with such webs as each will result in roller contact with both sides of the web.
Pressure-sensitive label stock is produced at Green Bay Packaging by tandem coating a release base with silicone, then with adhesive, and then it's laminated to paper or film. For Green Bay Packaging's facility in Wisconsin, the single-side contact that vacuum rollers provide is critical. Double-sided contact would mar the adhesive and coat the roller. “Vacuum rollers are a necessary piece of equipment because they combine single side-contact and tension isolation,” says Mike Mendolla, special projects coordinator. “We couldn't do it any other way.”
Green Bay Packaging employs 12 vacuum rollers. Vacuum rollers have been in service there for 25 years, mostly to isolate web tension with single-side contact before and after dryers and around coating processes.
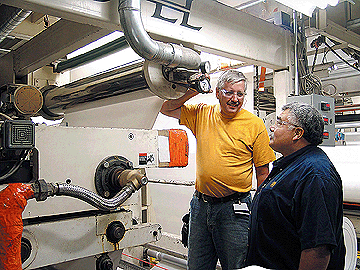
Isolating Web Tension
Controlling or isolating web tension can be critical to various processes, such as coating or laminating. Vacuum rollers often are employed to isolate web tension by either pulling the web or holding it back. In doing so, vacuum rollers can sustain large tension differentials within a single web line. The positive grip and control helps minimize web stretching and resulting web breaks, even with lightweight films at very low tensions.
Page 2 of 2
Giorgio Girardi, plant engineering manager at Arkwright, has found vacuum rolls to be the surest way to maintain proper web tension and consistent coating while avoiding scratches to coated surfaces caused by the double-sided contact of nip rolls or “S” wraps. Arkwright currently employs three vacuum rollers on one coater and two vacuum rollers on another coater.
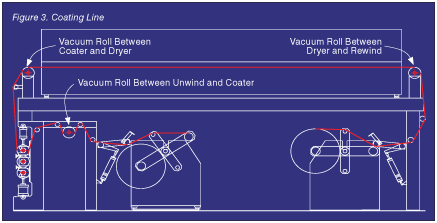
Coating operations, like those at Arkwright and Green Bay Packaging, use vacuum rollers to isolate web tension in floatation dryers and prevent web flutter, ensuring consistent drying of web coatings (see Figure 3). Mendolla explains, “At Green Bay Packaging, one vacuum roller pulls the coated web right before the dryer. There's another vacuum roller at the exit. This way we regulate web tension inside the dryer from end to end.”
Safer Alternative to Nip Rolls
Nip rolls are a potential source of worker injuries. This factor alone has led some web processors to specify vacuum rollers wherever possible.
Unlike nip rolls, vacuum rollers will not produce scratches, imprints, and wrinkles in the web that result in unusable material. Moreover, vacuum rollers save operator time by eliminating nip adjustments for web thickness, by providing better access for web threading, and by avoiding the need to manually close nips before starting a line.
Users like Girardi often appreciate the improved safety, reduction in scrap, and savings in operator time that come from replacing a nip with a vacuum roller. “The feature I like most about vacuum rollers is not having to run the web through a nip,” says Girardi, “In fact, we are now planning to install two more vacuum rollers on the coating machine at our Rhode Island facility to replace existing nips.”
Guiding Webs
Vacuum rollers are gaining popularity as part of web guides. This application takes advantage of the vacuum roller's ability to keep a good grip on the web, even as path adjustments are being made by the guide.
When used as edge guides, vacuum rolls not only serve to guide webs but also to isolate tension at the same time.
Mendolla says one of the coating machines at Green Bay Packaging uses a vacuum roller as part of an edge guide. Here the roller is configured as part of a web guide with a conventional edge detector to monitor web shifting. “The vacuum roller continually pivots to keep the web in line throughout the machine so it never drifts to one side or the other,” he states.
Design Considerations
To calculate vacuum roller specifications, most manufacturers will need the user or machinery builder to provide the following operating specifications:
- Maximum and minimum web width
- Wrap angle
- Substrate types/thicknesses
- Line speed
- Tension and tension differential ranges
- Orientation of the center of the vacuum zone
- Operating environment, including web temperature, air temperature, explosion-proof requirements, clean room considerations, elevation, and electrical power available
Among all the input specifications, the least understood and most important is tension differential. This is not the range of tension at which the web line can run but the difference between the tension zones preceding and following the roller. This is the net tension value the roller will either have to pull or hold back. This is also the value that will drive the sizing of the roll and the air system.
“When it comes to managing Arkwright's tension differential, we use eight-inch and ten-inch vacuum rollers because our specific tension differential determined the diameter of the roller,” Girardi says.
Other considerations also can drive the specification of a vacuum roller, such as the substrate, how the roller will be driven, where it will be mounted, and locations of adjustments or connections.
Vacuum rollers have been used successfully in coating and converting for many years. Still, those who seek to create a better coating or converting process or a better web product continue to apply vacuum rollers in creative ways.
Those who understand the characteristics of vacuum rollers usually are the ones who achieve greater results in using these unique rollers for enhanced productivity and safety. The possibilities are many when you consider all the ways vacuum rollers can control a web.
Pete Eggen has more than 20 years' engineering experience within the converting industry in process analysis, product design, and applications engineering for web process rollers. He is currently roll product manager at Webex Inc., Neenah, WI. Contact him at 920-729-6666.
Supplier Info
-
Webex Inc. | www.webexinc.com
Circle 320 or visit www.freeproductinfo.net/pff
The views and opinions expressed in Technical Reports are those of the author(s), not those of the editors of PFFC. Please address comments to the author(s).