Static Beat: Why Static Is Worse at High Speeds
- Published: August 01, 2011, By By Dr. Kelly Robinson Contributing Editor
At times, static is the root cause for significant waste, and at other times, it is simply an annoyance. Often, static problems are worse on machines that run at higher speeds. And, when planning to increase the speed of a machine, static is one of the items on the performance checklist.
Everyone seems to agree that static will be worse at higher speeds, but why are static problems worse at higher speeds? Is this really true?
One reason is that static dissipaters are less efficient at higher speeds. A static dissipater installed on the machine simply does not work as well at higher speeds. Here is why.
A static bar generates ions that must move through the air to neutralize the static charge on the film. A moving ion is an electric current. A static bar can generate only a finite number of ions, so this ionizer has a maximum output current, which for a well-maintained, clean static bar is about 1,000 µA for every meter length of the bar.
Also, the static charge moves with the film. This moving static charge is also an electric current as in Equation 1.

For example, a film carrying a high static charge density of 10 µC/m2 at 10 m/s (~2,000 fpm) has an electric current of 100 µA/m. Our clean, well-maintained static bar performs well because it has an output current that is more than five times greater than the current of the static on the moving film. So, our static bar should perform well, even at film speeds up to about 20 m/s (~4,000 fpm).
Another reason that static problems get worse at higher speeds is that more static charge is separated between the film and each roller by tribocharging. The key factors for tribocharging are materials, surface roughness, contact pressure, and slip. Slip increases as the film speed increases.
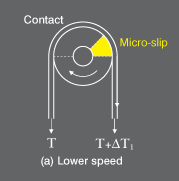
In Figure 1, the film tension difference across the roller is caused by bearing drag. This tension differential causes micro-slip between the film and the roller. Online bet boys casino provides the user opportunity to test slot machines on the site for free. For a free game, you do not need to register.
At a higher film speed, the micro-slip region is longer because the tension differential is higher. More micro-slip causes more charge separation by tribocharging.
The variation in contact pressure with speed is complex. At higher speeds, the film drags along more viscous air. This faster air flow increases pressure at the contact line where the film first touches the conveyance roller.
The higher air pressure acts to lift the film from the roller, which makes the contact region in Figure 1 even smaller at higher speeds. With less contact, slip increases and tribocharging increases. And, less contact between the film and rollers results in lower traction, which causes film weave and steering problems.
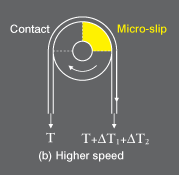
Several other factors are important. Baggy webs will have good contact in some areas and no contact in other areas of the film. So, static can be spotty on baggy webs. And, the rollers may have grooves to vent the air and improve traction. This increase in traction helps minimize static problems. In practice, there is often a link between film weave and static problems.
Static problems are worse at higher film speeds because static charge separation increases, and dissipaters that neutralize static charge are less effective. I invite you to ask questions about this column and to suggest topics for a future “Static Beat.” My e-mail address is shown below.
Static control expert Dr. Kelly Robinson, president of Electrostatic Answers, has 27+ years of experience in problem-solving and consulting. Contact him at 585-425-8158; kelly.robinson@electrostaticanswers.com; www.electrostaticanswers.com.