Static Beat: Corona Treaters & Ionizers Compared
- Published: June 01, 2010, By By Dr. Kelly Robinson Contributing Editor
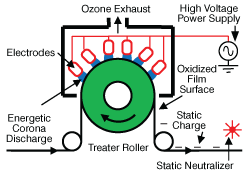
To prevent static problems such as coating defects, dust attraction, and sparks, static neutralizers may be installed along the film conveyance path. Commercially available neutralizers include brushes, tinsels, ionizing strings, static blowers, and static bars (pin ionizers). Each of these neutralizers generates ions using an electrical discharge — a corona discharge. In addition to neutralizing the static charge, do these corona ions change the physical properties of the film?
Corona discharge treatment (CDT) is a surface treatment technology that uses an electrical discharge to oxidize the surface of polymer film. This chemical change increases the surface wettability and promotes the adhesion of subsequent coatings. Figure 1 shows the key elements in a typical CDT unit.
The film to be treated is wrapped around a relatively large diameter treater roll. Several electrodes are positioned near the treater roller so the gap between the electrodes and the roller surface is typically in the range 0.05-0.15 in. When the AC high voltage (7-15 kV, 5-30 kHz) is applied to the electrodes, an energetic electrical discharge is struck between the electrodes and the film surface. The electrodes usually are longer than the width of the film to ensure the entire film surface is treated. So, the roller surface near each end of the treater roller is exposed directly to the electrical discharge.
To prevent a short circuit, an electrical insulator is needed. The roller surface must be covered with an electrical insulator such as silicone rubber; the electrodes must be covered with an electrical insulator such as ceramic; or both surfaces may be covered.
Corona discharge treatment is very different from static neutralizers. Two key differences are the power dissipated and the exposure of the film surface to the electrical discharge. The power supplies for CDT treaters are typically in the range of 5-20 kW. The power dissipated by a commercial CDT treater is comparable with the power dissipated by a residential house. The power dissipated by an active static bar is typically 5-20 W or about 1,000 times smaller than the power dissipated in a CDT. Knowing the film width and transport speed, the energy dissipated per unit area of film surface is given in Equation 1.
For example, a CDT treater operating at a power (P) of 1 kW treating a film width (W) of 1 m moving with a speed (U) of 1 m/sec has treatment energy density (E/A) of 1,000 J/m2. This is a typical treatment energy density for a polyethylene film to improve the wettability for printing or for increasing the adhesion of subsequent coatings.
The comparable energy density of a static neutralizer is about 1,000 times smaller. The low energy density of a static neutralizer is insufficient to even warm the film much less drive chemical reactions on the polymer surface.
The second key difference between CDT treatment and static neutralization of a film surface is the exposure of the surface to the electrical discharge. In Figure 1, note the electrical discharge in CDT treatment touches the film surface. This is very different from the static neutralizer in which the corona discharge is located at the sharp metal points in the ionizer. In static neutralization, the corona ions must drift across a large air gap to reach the film surface. This is a gentle, low energy process when compared with the energetic CDT process.
An unwanted by-product of CDT treatment is a high level of negative static charge on the film surface. So, it is common to locate a static neutralizer just downstream of the CDT unit as shown in Figure 1.
While it is sensible and common to group CDT and static neutralizers together as “surface treatments,” they are very different. CDT units are energetic chemical reactors, while static neutralizers are relatively benign, low energy devices.

Equation 1: E[Joules]/A[m2] = P[Watts]/U[m/sec]W[m]
I invite you to e-mail your questions and to suggest topics for future “Static Beat” columns.
Static control expert Dr. Kelly Robinson, president of Electrostatic Answers, has 27+ years of experience in problem-solving and consulting. Contact him at 585-425-8158; kelly.robinson@electrostaticanswers.com; www.electrostaticanswers.com.