Slitting Rewinding | Waste Not, Want Not
- Published: May 14, 2018, By Sharon Spielman
Time Is Money, So Efficiency, Production And A Good Roi Tend To Be The Driving Factors For A Successful Slitting Rewinding Operation. How Are Slitter Rewinder Manufactures Making This Happen For Their Customers?
Because slitting/rewinding is the last part of the process in flexible packaging production, it is important that this department runs efficiently to get the converted product out the door and to the customer.
“I visit many flexible converters on a global basis and am always surprised by the amount of work in process (WIP) that is accumulated prior to slitting,” Barrie Homewood, Titan sales and marketing director at Atlas Converting (atlasconverting.com), recently told Converting Solutions magazine. So, what’s the solution? “Make the slitting department efficient and eliminate any backlog,” he says.
This seems to be a must for the industry. Randy Wolf, director of business development at Kampf Machinery Corporation (kampfusa.com) in Windsor, Conn., says that their customers are looking to incorporate and embrace automation and technology on a slitter rewinder that is designed to be operator friendly to reduce downtime, decrease waste and increase efficiencies. “Recent innovations have enhanced the performance of slitter rewinders substantially,” he says. “They include the use of programmable logic controllers (PLCs) for product datafilesorslitjobstoragerecipesettings.”Thesesettings can include but are not limited to controlling and saving tensions, contact roll pressures and overspeed settings and slit width patterns involving automatic knife positioning systems. “The PLC job storage feature puts all of the operators on the same page so that they all can operate the machine within the same window of success after proper training,” Wolf says.
Albert Torrent, slitting brand manager at Comexi (comexi.com), agrees. “All customers want to achieve a high return on investment (ROI). To achieve it, they look for reliable equipment that provides the best possible slitting quality. Time is money, so converters and customers also look for a high productivity ratio in order to reduce dead time or waste time. The packaging and flexible packaging market tends to ask for more automated solutions.”
Torrent adds that customers want solutions that increase the added value of the slitting process. “Currently, they appreciate doing one shot laser perforation and re-closure labels while they are performing the slitting process.”
Chris Vaneman, president of Focus Optical Alignment Inc. (focusOAI.com), agrees with Torrent. “Product quality and system speed definitely impact ROI. Precision alignment is a driving force to ensure proper equipment setup, so these dynamics can be achieved,” he says. Focus provides the installation and maintenance support as well as management-related services to ensure components get placed where they are designed to be placed and within the tolerances defined by the industry, designer and manufacturer. Vaneman explains, “This is the service that allows designed maximum operating speed, product quality, reduced waste and reduced down-time to be achieved. We methodically troubleshoot web issues, such as wrinkles, baggy edges, product consistency, uneven coating, print station coordination and poor tracking.”
WHAT’S TRENDING NOW?
When asked about what trends they are seeing in the slitting and rewinding part of the converting process, Wolf and Torrent agree that productivity and profitably are key. “There is a big trend at the moment to focus in on material handling,” Wolf says. “Included with your slitter rewinder should be material handling features and options that will increase the pure productivity and profitability of your slitter rewinder. You could have the fastest slitter rewinder available in today's market, but if you can't get the finished rewind rolls off and reload the new cores onto the rewind shafts then the money you spent for that speed is totally lost." He explains that the material handling options can include rewind shaft finished roll pushers that will automatically push the finished rewind rolls off thecantilevered rewind shafts onto a rewind unloading unit that can automatically marr yup to the rewind shafts and then automatically pivot away and turret over for the proper unlaoding height. "These rewind unloading units can even be designed to marry up to a conveyor or a robitc roll handler that incorporates palletizing and wrapping," Wolf says.
Torrent agrees with Wolf about material handling. "Machine upgrades can be improved if we automate all the steps that occur after slitting such as labelling, wrapping or palletizing, using robots connected to our slitters. This improvement is one of the main ways to reduce drastially any downtime. In that sense, it is possible in the tuture that all machines installed in a plant will be connected to a cloud system that will help the companies to improve their efficiency and performance - not only on giving them different key performance indicator (KPI) ratios but also giving them recommendations on how to produce the jobs."
Torrent also sees a few other emerging trends in the slitting, rewinding and flexible packaging arena. "Things such as shorter printing runs, automation, the current explosion of new market niches, a demand for personalized and differentiated products, the emergence of eco-friendly packaging, and packages that are more sustainable and legthen the useful life of food or any other product are some of hte trends we are seeing," he says. "But above all, slitting equipment that offeres the highest productivity and the ability to respond efficiently to the latest market needs is what customers want."
Vaneman adds that line speed and product diversity are the most veneficial advancements to the industry. "Along with that increase in speed comes an increased need to consider precision alignment for optimizing line performance. We are of the opinion only the imagination of the engineers that design these units and the unique desires of the end user will limit what rewinders and slitters can accomplish in the future.”
Torrent says, too, that the demanding market for more customized products and better products in terms of shelf life and usability means that they need more complex structures with added value solutions, like easy openings.
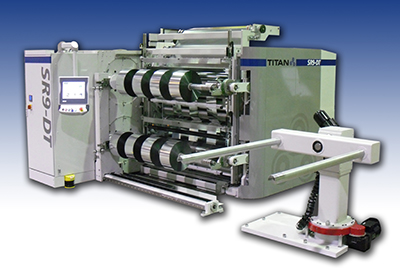
"Companies are being forced to lead with complexity and a rise of stock keeping units (SKUs),” Torrent says. “So, companies need slitters and rewinders that are able to deal with more complicated jobs and able to avoid being stopped and downtime. Changeover is critical.”
Regarding this, a machine’s runtime can be improved dramatically if value-added solutions such as double turret rewinders, automatic knife positioning, automatic core positioning or automatic taping, are used.
Wolf explains that a converter must understand that there are two very distinct cycle times associated with a slitter rewinder. First is the rewind cycle time, which is related to the time required to remove the finished rewind rolls and re-core the rewind shafts for the continuation of that specific slitting job. Second, and as critical, is the job change over cycle time, which is associated with the changing of slit width patterns and usually materials. “Many converters fail to account for the time it takes to accomplish this task. Here again the use of automation and technology and also similar job scheduling plays important roles in minimizing this job change over cycle downtime. The PLC with recipe storage along with other options such as automatic knife positioning units will minimize the time required to change over a slitter rewinder. The settings from when you last ran that job successfully are stored in a recipe and in conjunction with an automatic knife positioning unit can reduce job changeover downtimes by up to 75 percent.”
WHAT’S CHANGED
Kampf’s Wolf reiterates that automation and technology have changed dramatically the slitting and rewinding process over the years. “Most duplex slitter rewinders of today incorporate the use of differential cantilevered rewind air shafts which remain in the machine at all times. Nearly all machines couple this design with rewind shaft finished roll pushers. They also include shaftless floor pick-up driven unwind stands.” Wolf says that these features result in no lifting of shafts and rolls or the need for overhead hoists. He continues, “These developments increase efficiencies and improved ergonomics and safety for the operators while working around the machine. The loading of master rolls and unloading of the finished rewind rolls and the handling of shafts are areas which have caused headaches and potential injuries for converters for years. The machines of today have solved these issues.”
Along with the cantilevered differential rewind air shafts there are now means to locate the rewind cores thru laser core positioning systems, Wolf says. “This feature is extremely helpful during rewind set Cycle Times. This allows the operator to place the new rewind cores properly and correctly onto the rewind shaft after unloading of the rewind shafts. Again, it increases efficiencies of the machine and reduces both the time in setting of the rewind cores and reduces waste.”
Contact Company