Edelmann and Codimag Web Offset Semi-Rotary Web Presses Are for Short Runs
- Published: March 01, 2009, By By Chris Davis, Matik North America
In the evolution of print, there have been many discoveries, inventions, and improvements that have shaped the industry as we know it. There are a variety of processes from which to choose, depending on technology, substrate, economies of scale, quality of print, in-line efficiencies, format, consumables, and other reasons linked to the final printed product. The result is that many processes have gray areas where it can be challenging to answer the question: Which is the best way to print this job?
What is clear is that each process has developed strongholds, and now these are being challenged by pricing pressures on production costs, logistics, raw materials, obtainable margins, and perceived quality. This means non-mainstream processes now are being accepted as platforms of high efficiencies for market sectors such as short-run labels, for example. One such technology is a semi-rotary (intermittent) web press.
Semi-Rotary Press
Developed in the 1970s, the semi-rotary process was used in the forms business and simplified label applications that used one cylinder size to capture many different repeats by using a web that shuttles backward and forward. An infeed and outfeed in tandem produce a festoon. The reverse stroke of the web creates differing amounts of web travel, which equates to differing print repeats.
Letterpress was the print method of choice until the 1990s when offset was introduced into the world of semi-rotary. The main reason was that quality expectations of buyers and designers alike became more demanding. Fine vignettes and text on the same plate as a solid caused many production hurdles for flexography and letterpress.
Offset provides excellent image reproduction in CMYK with the full range of screens available. In tandem with the substrates that were being developed, for example, clear stock, image reproduction required the more refined process of offset.
The achievable quality now has led to semi-rotary web presses being used to print for the health and beauty aids and personal care markets, which are well known for their exceptional standards. Wine and spirit labels were the entry point for many semi-rotary presses in the 1990s. The labels printed today must be more eye-catching and have the necessary aggressive shelf appeal that offset can produce.
Offset also introduced cost reductions when compared to flexo. Offset plates typically are 15% the cost of flexo and are easier, quicker, and more accurate to mount.
Waste is reduced, as a semi-rotary press has a straight-through web path, not looped through the press to accommodate driers and pull groups. A straight-through web path also allows register to be maintained more readily. The overhead needed for running flexo presses — cleaning the anilox, mounting plates, etc. — is a cost that offset avoids.
Most semi-rotary presses have web widths between 10 in. and 17 in. and generally repeat from 2-17 in., depending on which machine is being considered. Regardless, this size of machine is directed toward the short-run market, which starts at 1,000 ft and goes to 30,000 ft.
The result is a press with one fixed size of print cylinder that can print a multitude of sizes without having to change anilox/plates/gears. This not only reduces costs but simplifies the process. Depending on the manufacturer, both conventional and waterless offset are used.
Waterless offset brings another refinement to the process — one less adjustment to make (the ink/water balance). It lets the converter print up to 300-line screens, as the dot is sharper and better defined.
The most standardized process worldwide is offset. Consequently, inks and consumables are readily available, as are operating personnel that understand standard colors and how to maintain them.
Technology has further enhanced the semi-rotary offset press with the addition of servo drives. As a whole, these drives have had a big impact on the industry and have provided basic platforms for lean manufacturing, quality standards, workflow, and so on.
New Inking System
A recent development in the semi-rotary world has married the ink feed system of flexo to the stable image carrier of offset (see figure below), and in doing so, has removed all rubber rollers from the ink train and their incumbent setting/replacement/maintenance costs. This system utilizes a temperature-controlled anilox, which feeds a form roller, and in the tradition of offset, inks a plate, transfers the image onto a blanket and then onto the web against an impression cylinder. A clear advantage is that ink profiles are fixed and do not need to be adjusted, and as there are no rollers, the press is up to color very quickly, thereby reducing waste.
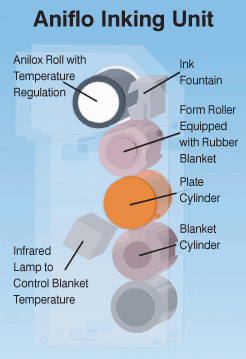
Repeating the theme of short run, low waste, and quick to makeready, the semi-rotary press uses magnetic cylinders for the converting stations, so the combination of low plate costs and quick mounting continue to remove costs from the traditional flexo process of printing short-run labels.
Digital web presses have been tackling the ultra-short-run sector (less than 1,000 ft) very successfully. They have simplified the process considerably and are very flexible to the converter.
The quality produced is very high, and a multitude of substrates can be run, but depending on how the label needs to be converted and its application, there are restrictions or further processes that need to be considered in the cost. Maintenance and “per click” charges can make the monthly overhead on this platform considerable, and that makes runs of more than 1,000 ft uneconomical.
The up-and-coming inkjet technology is showing great promise for short-run labels. The general consensus seems to be that the quality is not quite there yet, but it will be in the short term. The concern with inkjet is the cost of ink, and early indications show it is comparable with digital regarding economical run lengths.
Gravure generally is not considered in this market sector due to the considerable costs of the image carrier. In a price competitive situation, even for noncommodity items, it is a tough sale.
In recognizing that each process has strengths, a number of manufacturers allow processes to be ‘mixed’ to open the real potential of the semi-rotary press for a variety of substrates with different characteristics — from metallized paper to clear pressure-sensitive stock. Offset, letterpress, silkscreen, and flexo are offered in the same press to allow the other processes to add embellishment to the strengths of offset.
One example would be laying down a white footprint on a clear stock or a strong hit of a PMS color, which is then varnished and/or laminated. Combination printing is nothing new, but in the short-run sector, it reinforces the commercial advantages of a semi-rotary machine.
It is widely known that the majority of run lengths are now less than 35,000 ft in North America. This means that converters are considering all technologies to tackle this market sector, and semi-rotary has generated a lot of interest, resulting in machine sales.
Chris Davis is sales manager of offset technologies at Matik North America, West Hartford, CT. Formerly an aero engineer at Rolls Royce, Davis joined the printing industry 14 years ago, initially selling Edelmann web offset presses in the UK. Now a US resident, he promotes the offset range at Matik (Edelmann and Codimag semi-rotary presses) in harmony with his flexo colleagues. Contact him at cd@matik.com.
Supplier Info
-
Matik North America | www.matik.com
PFFC-ASAP 344
The views and opinions expressed in Technical Reports are those of the author(s), not those of the editors of PFFC. Please address comments to the author(s).