Green Converting: Leading the Pack
- Published: September 01, 2010, By By Nsenga Byrd Thompson, Associate Editor
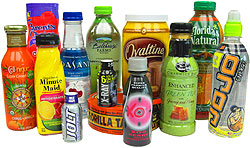
For New York-based Hammer Packaging, leadership means staying ahead of the curve, adopting new technology, and valuing its employees. As the recipient of the city of Rochester's 2010 Environmental Leadership Award, it also means demonstrating a significant commitment to environmental stewardship.
The award is sponsored jointly by the Rochester Inst. of Technology/Golisano Inst. of Sustainability, the Greater Rochester Enterprise Business Council, and the Rochester Business Journal. Hammer Packaging's recognition focuses on its commitment to recycle, reuse, and reduce all materials, supplies, waste, and energy and to use renewable resources when economically feasible in the management of its business and in fulfilling the needs of its customers.
“We are very proud to be honored with this award,” says president and CEO James Hammer. “It reflects the fundamental business ethics that drive this company, whether it's regarding our employees, customers, business partners, or the broader community.”
A Commitment to Green Practices
Hammer Packaging currently recycles 84% of its waste, materials, and supplies companywide. The company also utilizes ultraviolet (UV) and electron beam (EB) technology. “By offering UV and EB inks and coatings, we are able to reduce 80 to l00 percent of the volatile organic compounds produced when printing versus other types of inks and coatings,” Hammer says. “And compared to aqueous inks, UV and EB inks use 50 percent less energy for curing. We also eliminate the need for laminates and adhesives by using our mono-web, EB print process.”
As another example of the company's dedication to sustainable practices, Hammer Packaging reduced carbon emissions from interbuilding trucking by consolidating three locations into one in 2008. “Sustainability is one of four pillars that support Hammer's strategic business planning. It's also an attitude at Hammer. We see it as an extension of our commitment to continuous improvement,” he says.
Breaking New Ground
In developing an effective sustainability program, Hammer Packaging recognizes the importance of investing in equipment that's innovative and maximizes efficiencies without increasing its environmental impact. The company's most innovative achievement has come in its web offset division with two 35.5-in., nine-color variable sleeve offset presses (VSOP) from Muller Martini. With shrink sleeve and roll-fed label production being a hot market for the company, the two VSOP presses generate 20% of Hammer Packaging's current business.
“By having this VSOP technology, for the very first time people in the sleeve market have the ability to come to us and say we want to mix and match our items and combination on the press,” says Lou Iovoli, VP of sales and marketing.
Iovoli describes the presses' print quality as “exceptional” but says the critical differentiating factor of its VSOP presses is in the platemaking process. “There are no upfront costs for cylinders and plates, which can be in six figures quickly, depending on how large a line of products you are trying to produce,” he says.
Another critical element is the sleeve technology. “Prior to this technology, you had a fixed repeat, so if you printed a 10-ounce label and then you had to print a 32-ounce label, the length of the label changed, and if it didn't fit around your cylinder perfectly, you would have a gap,” Iovoli explains. “You would have to change the whole mechanical unit out of the press and put a new unit in. Today, we change sleeves in seven minutes.”
Flexo Expansion
Along with recent investments in its web offset division, Hammer Packaging recently expanded its flexo division with the addition of a ten-color Nilpeter UV press. This press is targeted to complement Hammer's customer base and expand its presence in pressure-sensitive markets. The investment, along with the installations of its Muller Martini VSOP presses, reinforces the company's commitment to innovative, state-of-the-art printing technology.
The servo-driven Nilpeter press is said to be ideal for handling an extremely broad range of multisubstrate packaging materials and features extensive printing options, such as high rotary silkscreen, lamination, hot stamping, and cold foil capabilities. The press also features easy-load sleeve technology that provides super-fast makeready.
“Its printing capabilities are just great. We are very happy with the results that come off it,” says Iovoli. “It's a great complement because its about half of the width of our VSOP. So we can take work that we are printing offset and complete it in our flexo division.”
“This new flexo print capacity allows Hammer to offer exceptional flexo print quality as well as superior registration with low waste and setup times, providing multiple solutions for our customers' package decorating needs” adds Hammer.
Continue to Page 2: The Final Piece
The Final Piece
Although the company's web offset and flexo divisions have been key in differentiating Hammer Packaging from its competitors, Iovoli describes the company's sheetfed division as its “bread and butter.”
“In that area, what makes Hammer truly unique is that there is no company in the world that has the range of press configurations that we do to accommodate our customers' needs. We have two 64-inch rollfed KBA presses, two 56-inch sheetfed presses, and a whole fleet of 40-inch presses,” Iovoli describes.
The company's most recent investment in this division was the addition of the second 64-in. press from KBA, featuring in-line sheeting capabilities, which has allowed the company to reduce its energy consumption compared to the more conventional sheetfed processes.
“We started doing the Campbell Soup label business about a year and half ago, and when we started that business, we only had one of the KBA 64-inch presses. We knew right away we needed two, because the work we were running on the other format presses really should be run on this press, and with that, we can be faster and get more out the door,” says Iovoli. “We can give them shorter lead times. We can be more customer-oriented.”
Iovoli believes that investing in the KBA press, along with its diverse portfolio of presses that also includes Heidelberg, provides the company with a competitive edge.
“Jim Hammer tends to invest in technologies that are the best. He believes that you get what you pay for. We want to be the best operation out there,” says Iovoli.
Through innovation, core organization values, and a strong commitment to environmental practices, Hammer Packaging takes pride in being a leader in the industry it has served for nearly 100 years.
“‘Lead, don't follow’ is a personal motto or mantra by which we do business,” says Hammer. “We lead the industry by investing in state-of-the-art technology, which allows us to deliver an exceptional brand image and speed-to-market.”
Converter Info
-
Hammer Packaging | 200 Lucius Gordon Dr., West Henrietta, NY 14586 | 585-424-3880 | www.hammerpackaging.com
Hammer Packaging's sustainability program includes the following highlights:
- 100% of the ink and 99% of the coating remaining from the printing process are reprocessed and reused.
- 100% of coating totes, skids, end boards, core plugs, and H-channels are reused.
- No solvent-based inks or coatings are used.
- A home computer recycling program is offered to employees.
- Non-recycled waste has been reduced 69%, which is sent to a burn facility over three years.
- R&D efforts helped reduce the paper weight by 15% for several large customers.
- Up to 20% post-consumer waste on certain grades of paper stock is used and up to 10% post-consumer waste for wet-strength paper.
- An extended color gamut option (Hexachrome) is offered, which reduces time and energy in the production, setup, and cleanup process.
- Renewable-certified paper is used whenever possible, based on customers' requirements.
Best Workplace Winner
Through nearly 100 years of experience, ingenuity, and innovation, Hammer Packaging is proud to stand as a leader in the package printing industry. Founded in 1912 by Herman J. Meyering (as the Genesee Valley Lithographic Co.), the privately held package printer utilizes ISO 9001:2000 practices to produce high quality printed labels and package decoration for the global beverage, food, horticulture, and household products industries.
The company's extensive product line includes a variety of label structures — cut and stack, in-mold, shrink sleeve, roll-on/shrink-on, roll-fed, and pressure-sensitive — as well as other printing specialties such as box wraps, hang tags, and premium packets.
As the fourth generation of the family to lead the company, president and CEO James Hammer has served Hammer Packaging for more than 27 years, growing it from 60 employees and $4 million in sales in 1983 to nearly 400 employees and $100 million in sales in 2010. The company also includes three plants and a wholly owned company, J. MacKenzie Ltd., a custom paper sheeting and converting operation.
Jim Hammer attributes the company's growth and success to its organizational culture, which is based on a commitment to five shared values: integrity, respect, trust, credibility, and continuous improvement.
“Our culture is unique, and this strategy has allowed Hammer to grow consistently over the years and has validated our approach to placing people first,” he says. “It is a driving reason for Hammer being consistently recognized by our industry as a ‘Best Workplace in America.’ It's also how Hammer has earned the continued loyalty of 97% of our customer base.”
Supplier Info
-
Muller Martini | www.mullermartini.com
Circle 312 or visit www.freeproductinfo.net/pff -
Nilpeter | www.nilpeter.com
Circle 313 or visit www.freeproductinfo.net/pff -
KBA | www.kba-usa.com
Circle 314 or visit www.freeproductinfo.net/pff -
Heidelberg USA | www.us.heidelberg.com
Circle 315 or visit www.freeproductinfo.net/pff