High-End Paper Production: Coating System Uses Pneumatic Control
- Published: November 07, 2018
By John Bridges, head of marketing at AVENTICS Corp.
In the age of digitization, printed materials continue to face new challenges. Today, virtually personalized media tailored to individual users' behavior are in demand, along with the special machines to produce them. Matti Technology offers such a solution with its ultra-precise coating system designed for paper finishing. The GP Tinter SG-150 inks paper on one or two sides, while AVENTICS pneumatics ensure perfect roller contact pressure, as well as actuation of the ink pumps and safety controls.
Tinters are universal machines for coating paper with layers measuring in the micrometer range. Matti Technology designs and builds tinters that can be used as a stand-alone solution or integrated into digital printing presses. Depending on the customer’s request, ink changes and washing and cleaning processes are performed automatically.
The recently designed customer-specific machine is a first for the Swiss company. It weighs nine tons and the paper is accelerated at a speed of 100 meters per minute, in a width of 1,540 millimeters and guided through the tinter over different rollers. The end-user inks the paper on both sides with four colors, with ink changes taking place automatically. Due to the high speed, the wet paper must be dried on just a short section.
Thomas Amrein, owner and managing director of Matti Technology AG, explains the task: “The speed and contact pressure of the rollers is crucial for the print and thus the product quality. However, certain parts in the coating system are explosive areas due to the alcohol-based inks, which poses a major challenge.”
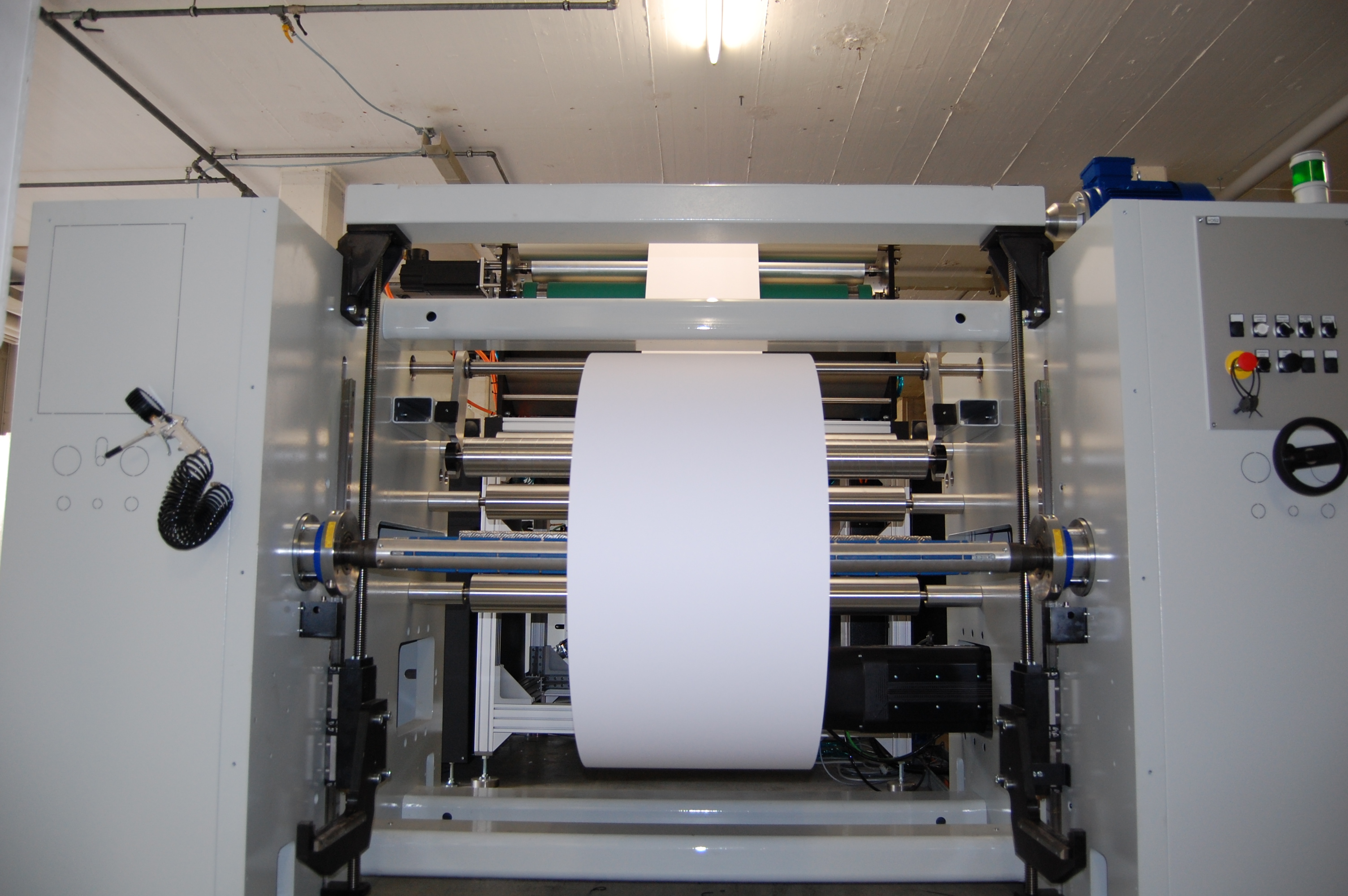
Matti Technology
AV valve system meets high precision requirements
The pneumatic components apply contact pressure to the rollers and control the ink and cleaning agent pumps from a total of seven containers, all while performing additional control functions. The core of the valve technology is formed by an AVENTICS AV03 Advanced Valve system connected to a parent programmable logic controller (PLC). It meets the high requirements for precision necessary to correctly apply the pressure to the paper web. The AV03 controls not only cylinders and
The 12 AVENTICS PRA series pneumatic cylinders in the tinter play a crucial role in the quality of the print: Controlled application of
The
Thomas Amrein summarizes the success of the construction designed in collaboration with AVENTICS, “The new pneumatics system allows us to optimally meet high expectations for this customer-specific coating system. Furthermore, we can standardize the system so that we can find and build a solution more quickly when we receive a request for special machines.”
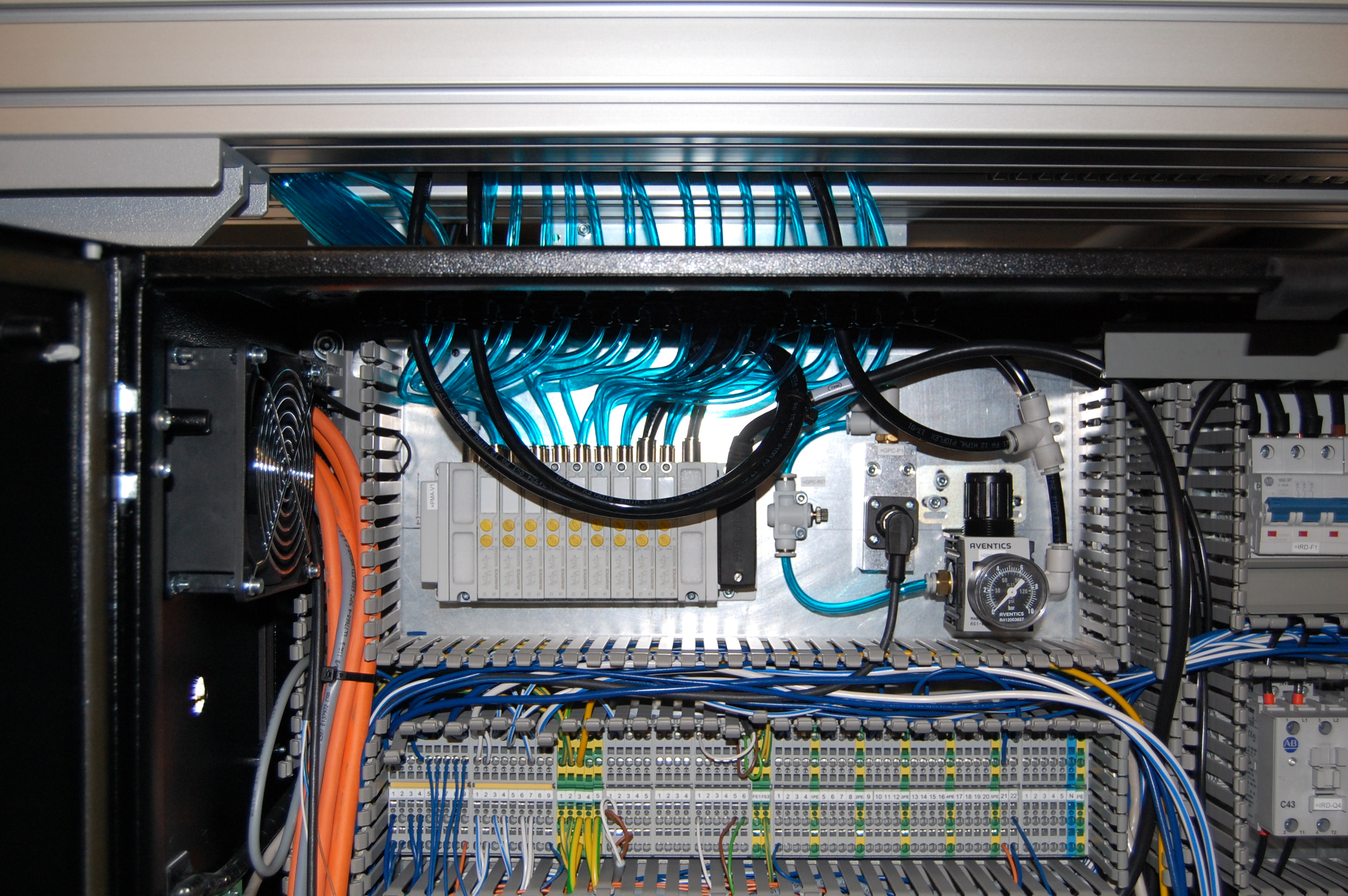
About the Author
John Bridges is the head of marketing at AVENTICS, a global pneumatics manufacturer, providing pneumatic valves, cylinders, actuators, air preparation, fittings and tubing,
Do not forget to visit the online copy of our monthly print magazine and sign-up to subscribe.