The PSA Process
- Published: January 31, 2006, By Joe Mausar, Chemsultants Intl.
Part 1 | Part 2 | Part 3 | Part 4 | Part 5 | Part 6 | Part 7
Pressure-Sensitive Adhesives
Pressure-sensitive adhesive products are a combination of several components coated and then laminated together to form a package or PSA construction. It is commonly a combination of facestock (for a label) or carrier/backing (for a tape), optional primer coat, adhesive, and silicone release coating on a protective liner.
The construction is complex and undergoes several coating and laminating processes, including liner release coating, adhesive coating/drying/curing, optional facestock topcoating or primer coating, and lamination of the facestock or carrier to the liner.
Two principal coating techniques are used to deposit adhesive on the web substrate: direct coating, in which adhesive is coated directly onto the facestock; and transfer coating, in which it first is coated onto a release-coated liner and transferred to the facestock during the subsequent lamination process.
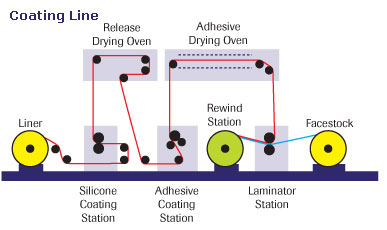
Coating and laminating are accomplished on a coating line (see figure), which creates the adhesive “sandwich.” PSA coaters usually are tandem coaters on which the two separate substrate webs (facestock/carrier) and liner are processed simultaneously prior to lamination.
Processing of the liner often includes application and drying of the release coating. Processing of the facestock may include application and drying of a primer coat. Actual adhesive coating may be by direct application to the facestock or by transfer application to the liner.
A number of methods are used for coating PSAs. They may involve pre-metering, by which the adhesive’s thickness or coating weight is determined prior to its actual application to the web substrate; or post-metering.
Coating technique is dependant on several factors, including the following:
- desired adhesive coating thickness
- viscosity of the adhesive
- PSA technology employed (solvent, emulsion, hot melt, or 100% solids)
- solids content of the PSA package
- required line coating speed
- the web material to be coated and its surface characteristics
- coating weight accuracy desired
- whether direct or transfer coating will be employed.
Once these issues are addressed, the most suitable adhesive coating method can be determined. Typical methods include the following:
Wire wound rod (Mayer rod) coating: A relatively low-cost post-metered coating method normally used for PSAs with good flow properties due to the possibility of “adhesive ridging” that can result from the wire. Because of this concern, wire wound rod coating is used primarily to adhesive-coat opaque web materials.
Knife-over-roll coating: KOR, one of the earliest coating techniques, is a simple, relatively low-cost adhesive method most often used to coat both solution and emulsion PSAs, but it also is suitable for coating hot melts. As with wire rod coating, KOR adhesive coating may exhibit adhesive streaking and adhesive void problems—especially with lower-viscosity adhesives at higher coating speeds. It usually is limited to opaque webstocks and lower-performance applications.
Reverse roll coating: This pre-metered adhesive coating method employs several rolls to pick up PSA, meter the adhesive amount, and apply the adhesive to the web. Adhesive supply may be from a pan for lower-viscosity PSA or from a nip formed by two rolls for higher-viscosity adhesives. This method usually is used to coat solution and emulsion PSAs but also can be used to coat hot melt adhesive from a heated pan. Reverse roll coating is quite common in the US but is less popular in Europe.
Gravure coating: This method includes reverse gravure, direct gravure, and offset gravure. Gravure is a pre-metered coating method that offers very accurate adhesive coat weights at high coating speeds but is one of the most costly methods. It usually is limited to low-viscosity adhesives and the application of low adhesive coat weights. It generally is associated with emulsion PSAs but also is useful for applying solution PSA and release coatings, and since it provides an extremely smooth coating profile, it is very suitable for use with clear film facestocks. Pattern or zone adhesive coating often is accomplished using specially engraved cylinders.
Extrusion slot die coating: This pre-metered adhesive coating method is an outgrowth of the screw extrusion process used in the production of plastic sheets or films. Most often associated with the coating of hot melt PSA because of its ability to handle high-viscosity adhesives, it offers two benefits: the ability to pattern-coat a PSA and the lack of the excess adhesive feed and recirculation issue experienced with most other adhesive coating methods (actual adhesive feed equals adhesive coat weight).
Slot die coating: This method differs from extrusion slot die coating principally in the use of pump pressure rather than screw extrusion for adhesive feed. It is more commonly used for coating lower-viscosity PSAs—hot melts, high solids emulsions, or 100% solids curable—and is very well suited to pattern coating.
Curtain coating: This pre-metered method is based on the creation of a “waterfall” or “curtain” of adhesive using a slot die. The curtain is positioned above—and separated from—the substrate web. Adhesive viscosity is extremely important in forming a consistent curtain to maintain desired coat weight and eliminate adhesive voids. Curtain coating is associated with high coating line speeds. Because of an “overcoating” phenomenon, however, pattern coating is problematic. Curtain coating is quite popular in Europe but is only beginning to gain popularity in the US.
A summary of some of the capabilities and limitations of each of these coating methods is shown in the table below.
Table I | |||||
Coating Method Capabilities/Limitations for Pressure-Sensitive Adhesives | |||||
---|---|---|---|---|---|
Coating Method | Viscosity (cps) | Coat Weight (grams/m2) | Coating Accuracy | Coating Speed (mpm) | PSA Types |
Wire rod | 100-1,000 | 15-100 | ±10% | 100-200 | Solution, emuslion |
Knife-over-roll | 4,000-50,000 | 25-750 | ±10% | 100-150 | Solution, emulsion, 100% solids |
Reverse roll | 300-50,000 | 25-250 | ±5% | 100-400 | Solution, emulsion, hot melt |
Gravure | 15-1,500 | 2-50 | ±2% | 100-700 | Emulsion, solution |
Extrusion die | 400-500,000 | 15-750 | ±5% | 300-700 | Emulsion, hot melt |
Slot die | 400-200,000 | 20-700 | ±2% | 100-300 | Emulsion, hot melt, 100% solids |
Curtain | 50,000-125,000 | 20-500 | ±2% | 100-500 | Emulsion, hot melt |
While the manufacture of PSA products is a relatively simple process of coating and laminating, we see that it entails a number of variables. Not all PSAs can be coated using any, or every, adhesive coating method. Coating methods are not interchangeable because PSAs are available in a variety of adhesive technologies (emulsion, hot melt, etc.), each of which has both viscosity and solids ranges associated with it.
PSAs require specific adhesive coating weights for defined applications and are composed of a number of different constituent materials—each of which can affect adhesive coating requirements.
In summary, the wide variety of identification, decoration, and bonding tasks, and a host of special application-specific requirements, have a direct influence on the choice of adhesive coating and laminating process for pressure-sensitive constructions.
SUPPLIER INFO:
Chemsultants Intl.—PFFC-ASAP 306. chemsultants.com
Joe Mausar is marketing and sales manager for Chemsultants Intl. His experience includes tenure as operations manager for the Pilot Coating Business of Chemsultants, where he was responsible for the operation of three pilot coating and laminating lines, along with finishing operations. He can be reached at 440/352-0218.
Part 1 | Part 2 | Part 3 | Part 4 | Part 5 | Part 6 | Part 7