Long-Run Liners
- Published: February 28, 2005, By Edited by Edward Boyle, Contributing Editor
Offset Printing
The next time you’re in a McDonald’s restaurant, take a look at the trayliner—the typically decorative and colorful paper that lines the plastic trays on which the food is served. Chances are it was produced by VOX Printing.
Based in Oklahoma City, OK, the family-owned company has been printing and supplying trayliners and placemats for more than 27 years to fast food restaurants worldwide. The company, established in 1971 as a commercial offset printer, has emerged as a leader in cold offset printing, specializing in trayliners and placemats.
Vox’s press runs can range from a case of just 3,000 liners to multiple truckloads. Its largest single order was from McDonald’s for 17 million liners. In fact, the company reports its annual production of trayliners could circle the world four times over. Trayliners account for more than 90% of its annual sales.
VOX prints on a variety of recycled papers using soy inks, and its trayliners and placemats are tested regularly to meet government food safety requirements. The liners are also an important marketing tool for the restaurants themselves.
"It’s important for our customers’ patrons, when they are in the restaurant, to have a nice-looking trayliner, as it gives them a good impression of the restaurant," says David Reid, president of VOX Printing. "A high quality trayliner conveys the image that the restaurant pays attention to detail and has a high quality of food."
Just-In-Time Delivery
VOX’s customers typically stock two to three weeks’ supply of trayliners, which minimizes the restaurants’ inventory costs and allows them the flexibility to change the design and message. Being centrally located in the US gives VOX a distinct advantage in shipping costs and delivery time to all parts of the country, but more important is VOX’s ability to turn around the product.
"It’s not uncommon for us to get a job approved at three or four in the afternoon, output the negatives for the night shift to print, and ship close to a million trayliners the next day," says Reid.
"We’ve been fortunate to have good sales in the last five years," he says. "During this period, we went to two, then three shifts and were nearing the upper limits of our capacity on our existing three web presses."
VOX prefers to have additional capacity on its existing presses to avoid letting a customer down. "Being a family-owned business, we don’t have to just exclusively look at the bottom line. We take great pride in filling what our customers’ needs are, and sometimes we buy equipment a little before we have to in order to have that extra cushion to meet our customers’ deadlines. Many of the customers we have are as a result of being able to turn around jobs that their existing suppliers couldn’t. We got our first chance with those customers by helping them out of a bind, and they enjoyed the experience, our quality, and the way we worked with them, and they came back with longer-term business."
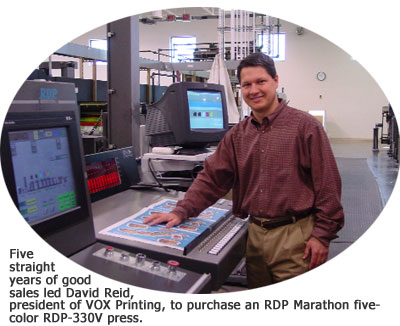
High-End Graphics
About two years ago, VOX’s search for a new press led it to RDP Marathon’s 330V press. The 33-in. press has been designed specifically for printers that want to compete in the long-run and high-end promotional graphics markets.
The press runs at speeds to 1,500 fpm and can be configured to print on stocks ranging from light forms to heavy paperboard. Available in configurations of up to ten standard printing units, the RDP-330V can be combined with flexographic coaters and in-line specialty finishing stations, including high-speed die-cutting and embossing stations.
The RDP-330V’s walk-in-style, 9,500-lb print tower, deep-dish gear side frames, and cylinders reportedly are manufactured with CAD/CAM technology to precise tolerances to ensure smooth operation and accuracy of impression during the most demanding applications.
The Maraflo V 4-form roller commercial inker is designed with an integrated dampener said to ensure maximum ink transfer at all production speeds. Drive train precision is designed to ensure exact register and reliable performance at high speeds, a capability vital to high-end markets.
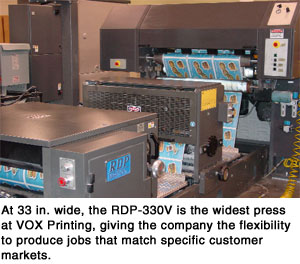
The RDP-330V Smart-Set press control system provides a central control of all press functions on an easy-to-use touchscreen graphic display. The open architecture control system provides job storage and retrieval, modem interface for local and remote systems diagnostics, and is said to integrate seamlessly with most management software, including CIP4.
Running concurrently with the Smart-Set press control system is RDP’s Optim+, a real-time press and job performance automated data collection system.
Designed to provide an analytic view of the printing process, Optim+ optimizes waste and performance management by allowing printers to track press run speed, average speed, bad count, good count, total count, and amount of web run, all automatically. Plant management also has the ability to remotely access and export the data log to a CSV file that can be read by most spreadsheet and database programs, including Microsoft Excel and Microsoft Access.
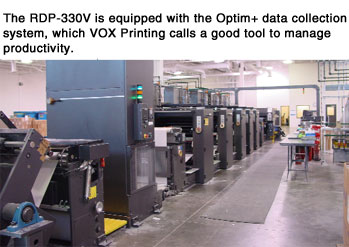
Ease of Use and Flexibility
VOX opted for a five-color RDP-330V press—to print four-color front and one-color back—configured with a butt splicer, high-speed commercial sheeter, ink key control, automatic register control, blanket washers, the Smart-Set press control system and Optim+ print performance management software. In addition to the RDP press, Vox operates three older Didde presses, ranging in size from 11–24 in., all up to five colors.
"We decided on the RDP for its quality, speed, mechanical stability, and reliability, plus the service and response from RDP was exceptional," says Robert Reid, production manager, VOX Printing.
As soon as the press was installed, a two-week training session was held for the VOX operator crew at their Oklahoma City facility. The learning curve on the RDP press was very quick.
"No one had problems learning how to use the touchscreens, learning how to inch it, etc.," says Reid. "We can put employees with less experience on the RDP, as it’s more forgiving. The oldest press we have is the hardest to set, and each press gets easier and easier. By far, the RDP is the easiest and most operator-friendly. The RDP is a very well engineered press both for operations and maintenance."
He adds, "The press itself has lots of bells and whistles, including recalling jobs with the parameters and registration control already set, and a web cleaner that cleans the paper to eliminate hickies and produce a better looking trayliner. And we like [Optim+] to look at how the press ran during the night. It’s a good tool to manage productivity; the most critical thing is that it logs and tracks production problems automatically, relieving employees of spending time logging when they are busy addressing the issue."
Speed, Quality, and Customization
VOX trayliners are shipped out boxed in what the company refers to as four-packs and six-packs, consisting of either four or six different trayliners to a case where customers can pick one, two, three, four, or six trayliner designs. This is in response to customers’ specific needs to promote existing products, or advertise contests, or where prior to doing a national launch, they want to test market acceptance and fine-tune the final product.
Prior to the RDP press, VOX’s widest web was 24-in. Didde model, and all the presses were fixed size, running two-up, at a speed of 1,000 fpm. With the RDP VOX can convert three 11-in. trayliners at one time at a speed of 1,500 fpm.
"The RDP press, because of the wider web, makes it easy for us to produce combo packs that match specific customer markets," says David Reid. "Customers that look at quality think that our quality is better. Price is always competitive, and we can save our customers a lot of money because we specialize in trayliners and have high-speed presses.
"But we position ourselves more on quality than price. You can get cheaper presses and cheaper paper and cheaper ink. Throw it all together, and you have a cheaper product. We take pride in what we print. If something’s out in the field and doesn’t look good, it’s embarrassing. We don’t look for the cheap solution. Where we make up for the high quality of paper and inks we use is with the efficiency of our presses and production folks. That way we can ensure a first quality printing, with the shortest possible turnaround time, at an affordable cost," says Reid.
Says Robert Reid, "The RDP is our first variable insert press that has also been really nice for scheduled maintenance—to pull out the insert, check the stripes, check the rollers, and change the rollers. It’s much more convenient than our fixed-size presses. Something that would have taken us days to get to, now we would just pull the insert out and fix the problem immediately. It’s really nice.
"We haven’t had to address the flexibility issue yet, but it’s also nice to have it in the back of your mind, that if the 14-inch market dies on us, we can go into another size market for a minimal cost and not be out the entire cost of the press. We were planning for the future when we bought the RDP."
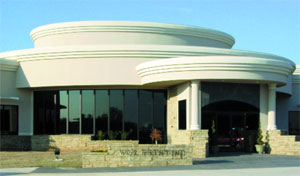
CONVERTER INFO:
VOX Printing
400 E. Britton Rd.
Oklahoma City, OK 73131
405/528-0151; voxprint.com
SUPPLIER INFO:
RDP Marathon—rdpmarathon.com
Didde Press Systems—didde.com