Hot Melt Adhesive Use
- Published: February 28, 2005, By David J. Bentley, Jr., Contributing Editor
PLC Probe
Hot melt adhesive use continues to grow due to unique properties including ease of use, adhesion to a wide variety of surfaces, strength properties, aging characteristics, etc.
The applications already using hot melts consume increasingly larger amounts of the materials, and new applications continue to materialize in which they are the adhesive of choice.
By some measurements, hot melts are among the fastest growing adhesives in the industry.
Hot melt adhesive application temperature is perhaps the most important variable users must consider when choosing these materials. The hot melt products arrive for use at room temperature when they are solids or extremely viscous fluids, as in the case of some hot melt pressure-sensitive adhesives. To use the adhesives, one must melt them. The melting process makes them less viscous and allows application by coating equipment, extrusion, guns, etc.
All the possible application methods require heating the adhesive to an elevated temperature. So, what is the proper application for a hot melt adhesive?
All manufacturers of hot melt adhesive products suggest a temperature range for the use of their materials. For an individual product, this may vary from 10–50 deg F.
Note that all hot melt adhesives do not have the same recommended application temperature range. The best practice for any user of a hot melt product is to stay well within the range provided by the manufacturer. The manufacturer knows the ingredients of the product and how to use it and is therefore the best source of the temperature range for a hot melt adhesive. The range provided takes into consideration such things as the effect of excessive heat, oxidation, and other detrimental factors the product can undergo when exposed to heat.
Users of hot melt adhesives need to know what effects temperature has on the materials. Using a material at a low temperature means the product will have a high viscosity. Because it is not very fluid, it will have poor wetout and flow. This can cause poor adhesion to the substrate onto which the hot melt adhesive is being coated. It also can cause poor coating weight control.
Another disadvantage of excessively low application temperature is a short open time. This means the adhesive may provide poor or low bond values because the adhesive simply is too cool and too viscous to transfer to a secondary substrate.
Excessively high temperatures can cause other problems. First, the hot melt material will exhibit excessive flow characteristics, causing it to penetrate into the substrate. Depending on the substrate, this may influence it detrimentally. Insufficient adhesive may remain on the surface, so the bond values will be lower than desired.
High application temperatures for hot melt products will accelerate degradation of the product. At almost any temperature, the materials will begin to degrade. Additives in the hot melt materials can keep this tendency to a minimum. At increasingly higher temperatures, the adhesive will degrade more rapidly and more completely. Eventually it can even reach a point where it is simply a very fluid, dark-colored material that is totally unsuitable for use.
Therefore, at a high temperature all hot melt products will have a greater tendency to form char particles. Their presence is especially disadvantageous because they can clog dispensers and coaters easily, causing streaks, low or zero bonds, and similar problems.
Converters that use hot melt products must be especially careful when applying them. Staying well within the application temperature range suggested by the manufacturer will ensure the problems mentioned above do not occur. Converters that push the envelope by using a temperature outside the recommended range run the risk of serious problems.
The primary lesson here applies not only to the use of hot melt adhesives but to the use of all products in the converting industry. Always follow the instructions of the manufacturer. In the case of hot melt products, this is especially true for application temperature. For a laminating adhesive, it might be crucial to follow the instructions for drying temperature; for a heat seal coating, the proper coating weight can be critical.
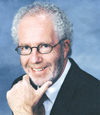
David J. Bentley Jr. is a recognized industry expert in polymers, laminations, and coatings with more than 30 years of experience in R&D and technical service. Contact him at dbentley@unm.edu.