Weight Control
- Published: June 30, 2004, By Edward D. Cohen, Edward D. Cohen Consulting
The quality and performance of a coated product depend on obtaining the desired coating weight and maintaining its uniformity in all the rolls of manufactured product.
A coating's functional properties — adhesion level, permeability, diffusion, color, durability, light sensitivity in imaging products, and electrical properties of thin film batteries — all require a constant uniform coating weight. In addition, manufacturing properties — maintaining line speed, uniform drying, raw material costs, and wound roll quality — are influenced by coating weight uniformity.
The control of coating weight in a web coating process often is viewed as a basic variable that's relatively easy to define and control. However, it is actually a complex variable to define and requires the integration of several technologies and good manufacturing practices to achieve the desired performance economically. Following are the process factors you need to ensure success.
- Accurately characterize the coating weight and its variability.
- Establish product and process specifications.
- Select the correct coating method.
- Measure coating weight on-line.
- Use appropriately designed coating applicator and station.
- Provide uniform solution properties to the coating applicator.
Coating Weight Characteristics
The starting point in obtaining a uniform product is to characterize the average value and the uniformity within the coated roll accurately.
A web coating line produces a roll with coated widths from 30 in. to more than 100 in. and is wound in lengths from 5,000 linear ft to more than 20,000 linear ft. Therefore, additional characteristic values — the coating weight profiles in the transverse direction (TD) and in the machine direction (MD) — are needed to describe the uniformity in these rolls.
These profile values are as important as the average values, since a customer can receive product that comes from varying locations in the web, and it is essential all locations in the web are similar, since most webs are slit into narrow widths for use by the customers.
It is also a significant factor if the wide web is slit onto several narrow webs. A wide variability either across the web or down the length of a roll can lead to poor product performance. A wide variability also can affect the drying behavior because the dryer must be able to dry the heaviest area. A nondried area in the wound roll can lead to the loss of the entire roll.
The TD and MD profiles are determined by measuring the coating weight across and down the web. There are a variety of statistical functions that can be used to describe the variability in these profiles and to permit comparison of various profiles as follows.
- 1 sigma/average expressed as percent
- 2 sigma/average expressed as percent
- 3 sigma/average expressed as percent
- (high-low)/average expressed as percent
There is no agreed-to convention for reporting on uniformity so a given percent variability can have different meanings depending on the calculation.
The preferred characteristic value for the coating weight uniformity is (high-low)/average expressed as a percent. It gives the best indication of overall uniformity and product performance. Profiles can give the same numeric values for uniformity and be entirely different. Figures 1-3 show three profiles with the same numeric uniformity, and it can be seen that the distributions are entirely different. The preferred profile from a product and product performance is to have a smooth profile with a minimum of spikes in the profile (Figure 3). Spikes in the profile, either high or low, will affect the process efficiency adversely. They can lead to poor winding because the spikes prevent the base from laying flat and winding a uniform roll. They also influence drying because the dryer conditions must be set to dry the heaviest area. This can lead to speed reduction and over drying of the lower coating weight areas if there is an abnormally high coating weight in the web. Figure 4 shows the MD profile for the same TD location in a roll.
Establish Product and Process Specifications
A key need in obtaining a uniform coating weight is to establish specifications for the product and the process conditions needed to manufacture it on the coating line. Following are the characteristics that need to be specified.
-
Average within roll, measurement method, and sampling pattern.
-
MD and TD uniformity within a roll.
-
Acceptable variation between rolls.
The specifications should be based on the performance needed by the customer and the capability of the process to achieve them at a competitive cost. If a uniformity of 2% is needed, then the key process variables such as line speed, pump speed, and solution viscosity must have the capability to achieve the specification. Also, with expensive raw materials, you do not want to apply more than is needed. A high uniformity profile often can permit a lower average coating because it is not necessary to compensate for low coating weight areas by increasing the average.
Measure Coating Weight In-Line
Continuous measurement of coating weight as the rolls are being coated will help to ensure uniformity. Recent technology advances have resulted in cost-effective instruments that continuously measure coating weight in-line in the coater and calculate all appropriate characteristics. This new technology can provide continuous single point or profile measurements, which can be rapidly displayed for use in process control and as part of a process control loop. The hardware cost for in-line gauges is higher then the classical methods of off-line measurement but is justified by cost savings and in improved product quality.
There are a wide range of sensor technologies available, each having its own specific advantages. The properties of the product to be measured will determine the appropriate method.
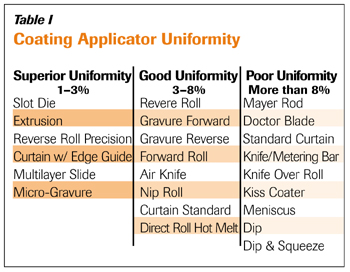
Select Correct Coating Method
There are a wide variety of coating methods that can be used to coat a product. Each method has an inherent uniformity it can attain. Typical values are summarized in Table I.
Often the wrong method is used and the desired uniformity cannot be achieved. For example, if a uniformity of 2% is needed and a method with 10% uniformity, such as Mayer Rod, is used, then the desired uniformity will not be obtained. The coating method must be selected that has the capability to provide the needed uniformity.
If the needed method is not available on your coating line, it is more profitable to install the appropriate method then it is to produce a defective product.
Coating Station Design
To help ensure uniformity, the coating station support design must ensure the applicator is rigid and can maintain the needed tolerances and applicator settings during production. The normal operation of a coater imposes severe stresses on the coating station, and it must be sufficiently rigid to avoid distortion. If the stations distorts, then the coating weight variability will increase. The mechanical hardware that controls important process variables, such as applicator to roll gap and roll speed, needs to be designed and fabricated to maintain desired settings during production. Any extra cost needed to have superior design will result in significant cost savings and improved product.
Reproducible Solution Properties
The delivery of consistent solution properties to the coating applicator is essential for all applicators. The viscosity and percent solids are critical variables in controlling coating weight in all coating methods. These variables must be controlled within very tight limits for all rolls coated. For the self-metered and doctored coating methods, the viscosity is one of the variables that controls the coating weight. In these processes, the viscosity can change due to evaporation of solvent, change in percent solids, reaction of ingredients, temperature, or the incorporation of bubbles. In pre-metered coating methods, while all of the solution is coated on the web, a change in percent solids will change the coating weight.
Measurement of viscosity after a batch of solution is prepared is not sufficient to control the process. In-line measurement of viscosity is needed and can be coupled with a solvent addition system to adjust viscosity within control limits. A good temperature control system will help maintain uniformity.
Edward D. Cohen is a technical consultant for AIMCAL. His expertise is in coating/drying of thin films, coating process development/scale-up, polyester base development, film defect mechanisms, and defect characterization techniques. He has 40+ years of experience in research and manufacturing technology and has many publications in the field. Contact him at 480/836-9452; cohened146@aol.com
This article, along with future articles by other authors, is provided as a cooperative effort between PFFC and AIMCAL. Authors contribute to AIMCAL's technical and education offerings, which include the association's Fall Technical Conference, Summer School, and Ask AIMCAL.
The views and opinions expressed in Technical Reports are those of the author(s), not those of the editors of PFFC. Please address comments to author(s).