Green Converting: Is IML Sustainable?
- Published: March 01, 2011, By By Ron Schultz, In-Mold Decorating Assn.
Although sustainability means different things to different people, it generally includes minimizing use of energy and non-renewable resources as well as reducing the amount of packaging for ultimate disposal. When planning decoration of rigid plastic containers, many choices are available, including the following methods:
- wet glue applied
- heat transfer
- pressure-sensitive (p-s)
- shrink sleeve
- in-mold labeling (IML)
Each of these labeling methods has its advantages and disadvantages, supporters and detractors. When we think of sustainable packaging in the context of labeling, we really are addressing how the labeling method influences the final container.
But not all containers are created equal. Some are very different and more sustainable than the rest.
Before the advent of in-mold labeling, traditional labeling methods all involved attaching a label to an already blow- or injection-molded container with some sort of adhesive. In its most basic form, that adhesive could be wet glue, an old method still used today in large volume.
A step up in sophistication takes us to hot melts and p-s labels, the latter being the largest volume labeling method worldwide.
Heat transfer, another popular labeling method, uses heat to transfer the label image from a release liner or carrier web to the container surface, a little like an iron-on decal used to decorate a T-shirt. Only the layers of ink and overprint coatings are transferred to the container without any paper or film label substrate.
Finally, shrink sleeving covers the entire container with a high gloss film.
No matter which of these labeling methods is chosen, they all share one very important attribute. The label is placed on the surface of the container in an additional operation after the container is molded.
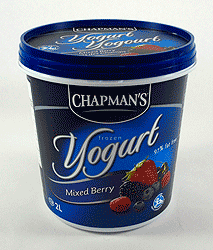
How Labeling Techniques Differ
Let's compare IML to each of the following competing labeling techniques.
Pressure-Sensitive Labeling | For p-s labeling, the container is molded, followed by, in some cases, flame treating before the application of the p-s label. This post-mold operation requires additional equipment, including the flame treaters and labelers, as well as extra labor, floor space, and operating utilities.
The release liner remaining from the p-s labels must be recycled, incinerated, or buried in a landfill.
Functionally, p-s labels can have good graphics, but they are subject to defects on the container, such as flagging, wrinkling, and puckering. Container recycling can be done easily if the label is made of the same material as the container.
Heat Transfer | This is another labeling method that competes with IML. Here again this post-mold operation requires flame treaters and labeling machines plus labor, floor space, and utilities, as well as release liner, which requires recycling or disposal. Heat transfer labels are subject to wrinkling, especially in larger sizes, and are not as durable as in-mold labels. Heat transfer graphics generally are not as good as the photographic quality of IML or p-s.
Shrink Sleeves | This technique increasingly is favored for small- to medium-sized bottles of laundry detergent, fabric softener, and personal care products. Shrink sleeves provide 360-deg, high gloss graphics but require considerably more film material than either an in-mold or p-s label because of their overall coverage.
A label sleeve is placed over the bottle before it travels through a heat tunnel to shrink the sleeve onto the bottle. This heat tunnel and associated conveyor are additional equipment that requires electricity and gas for operation.
Recycling of shrink-sleeved bottles is questionable unless the sleeve and bottle are known to be of the same plastic material.
In-Mold Labeling | This method is quite different in its simplicity. Most new injection or blow molding machines already are equipped with the label magazines, label placement automation, and label pinning equipment required for IML. At the start of the molding cycle, the label-handling robotics pick up die-cut labels from the label magazines and place them in the open mold where they are held in position against the mold wall by either static electricity or vacuum ports.
The mold closes, and the container resin is blown or injected into the mold. The hot resin fuses and encapsulates the label into the wall of the container. Then the mold opens, and the in-mold-labeled container is ejected, ready to receive product.
Which of these choices is the most sustainable? You might be surprised to learn that IML is the most sustainable labeling method, not for what it has, but for what it does not have.
Consider this list of items that IML decoration does not need:
- Post-mold flame treaters
- Post-mold labeling machines
- Utilities, such as electricity and gas, to operate those machines
- Additional wet or hot melt glue
- Extra labor to operate the labeling machines
- Extra floor space for the labeling machines
- Release liner to recycle, incinerate, or bury in a landfill
In fact, an in-mold-labeled container pops out of the molding machine with its label already embedded into the wall of the container. Nothing more is needed to make this container ready for filling with product.
All of the other labeling methods must glue a label onto the surface of a molded container in an additional post-mold operation before it goes to the filler or after it is filled with product. Furthermore, most of them require a release liner.
So for sustainability, IML requires less expenditure of energy, labor, and non-renewable resources than any other competing labeling process.
Ron Schultz is executive director of the In-Mold Decorating Assn., Scottsdale, AZ. He can be reached at 480-473-0301; This email address is being protected from spambots. You need JavaScript enabled to view it.; www.imdassociation.com.
What Is In-Mold Labeling?
In-mold labeling is very different from other labeling methods, and that difference begins before the container is formed. At the front end of the molding cycle, just after the previously formed container is ejected from the mold, in-mold labels are inserted into the mold before it closes.
There they wait for the plastic to be blown or injected into the mold, embedding the labels into the wall of the container during the molding process and displacing container resin equal to the volume of the label, about 15% by weight.
There's the big difference. In-mold labels are in the wall of the container. All others are glued onto the outer surface of the container.
That 15% resin savings is a good place to start keeping score of the sustainability list. Only IML allows the molder to light-weight a container while at the same time reinforcing its side walls.