Label/Tape | PolarSeal’s Custom-Designed Converting Machines Serve Diverse Industries
- Published: May 25, 2017
From auto tape to wound care products, UK converter revels in its reputation as an engineer’s dream.
Founded in 1981, PolarSeal Tapes and Conversions Ltd. has main offices and a production facility in Farnham, England, a town of some 40,000 people about 35 miles southwest of London. It’s a historic area that is also home to Farnham Castle and a number of old Georgian houses. The company has a duplicate manufacturing facility about 150 miles away, in the county of Suffolk.
While out walking several decades ago, the company’s founder, Frank Rich, a former oil-industry executive, spotted the polar star, Polaris, in the skies above Farnham. That supplied the first part of the company’s name. The second part refers to its mission of producing converted tapes and sealing materials. Hence the name: PolarSeal.
“We take a lot of pride in being ‘the engineer’s dream,’” says John Rich, the company’s senior director. “That was an actual comment from a longtime PolarSeal supply partner that we’ve adopted as our motto and calling card. It refers to our ability to take a project from initial concept and design through prototyping and testing all the way to finished product and production.”
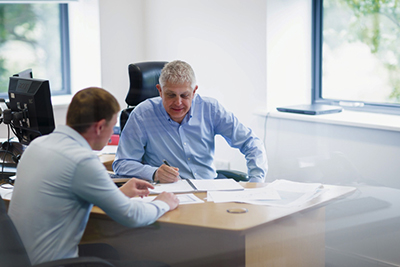
PolarSeal is a privately owned company with about 50 employees. It designs and produces flexible material converting solutions for OEMs and other customers worldwide, including many prominent names and brands. The company supports multiple business sectors, with the medical sector accounting for a sizeable percentage of sales. In that area, the company produces wound care products, incision films for surgical use, primary and secondary ostomy components, IV fixation devices, and diagnostic components.
PolarSeal collaborates closely with its longtime supply partners in order to develop advanced operations and processes. One such supplier is Vancive Medical Technologies of Chicago, IL, a business of Fortune 500 company Avery Dennison. Vancive employs sophisticated adhesive and material technologies to create advanced products for medical devices. PolarSeal and Vancive engineers and technicians often work together with customers to determine the best materials, adhesives, and fabrication methods for their specific device performance requirements.
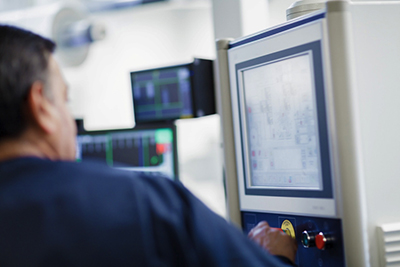
In one case, PolarSeal and Vancive partnered to develop a converting process for an ultra-thin, 30-micron wound dressing film. The process had to automatically remove the film from its release liner, apply non-adhesive areas to the film’s underside, and then return the film to the release liner—all without overstretching the delicate film. Technical teams from the two companies custom-designed a converting machine to accomplish the task.
According to Rich, PolarSeal has ample reason to foresee growth in the medical sector. “We recently successfully completed an audit conducted by the U.S. Food and Drug Administration,” says Rich. “There are a number of U.K. converters that have registered with the FDA, but to my knowledge PolarSeal is the only converter that has successfully completed an FDA audit. That should open the door to further success in the U.S. market.”
Duplicate Production Sites Offer Ultra-Reliable Source of Supply
PolarSeal is unique in having two nearly identical standalone manufacturing sites about 150 miles apart. The dual Farnham and Saxmundham, Suffolk County, facilities feature the same machines and production capabilities. This gives customers an added assurance of reliable supply and the benefits of dual sourcing from a single supplier. In the event of a storm, flood, power outage, or other emergency affecting one plant, the other site can quickly swing into action and complete the job.
“We’ve devoted several years of R&D to the goal of refining our converting accuracy,” says Rich. “As a result, we’ve been able to develop market-leading machines capable of extremely tight tolerances unmatched by standard machines.”
The Farnham and Saxmundham facilities each boast custom-made, fully intelligent servo-driven converting machines that deliver consistent, accurate results with precision web control and optical cut-to-register capabilities. The machines achieve down web tolerances of +/- 50 microns across a 300mm width.
In addition, PolarSeal offers clean, high-accuracy perforation capabilities for medical, aerospace, and other demanding applications. The company can perforate plastic films, foils, laminates, adhesives, wovens, and nonwovens. It can perform standard perforations or execute custom patterns including invisible perforation for breathability.
The Farnham and Saxmundham facilities have multiple cleanrooms that are validated and maintained to ISO 7 (Class 10,000) in accordance with ISO 14644-1:1999. They are accredited to international standards for medical device manufacturing and regulatory compliance.
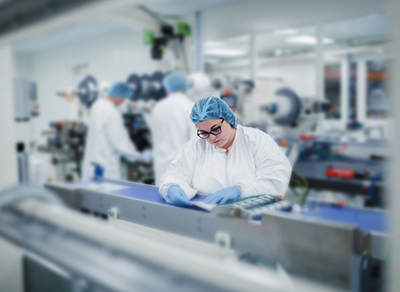
PolarSeal also operates an in-house testing laboratory to support its production and quality control efforts. The lab conducts a variety of tests such as peel testing and burst testing to provide customers with optimal quality assurance.
Supporting a Host of Applications in Diverse Industries
PolarSeal’s capabilities range well beyond the medical sector. The company also develops tapes, adhesives, and sealing materials for aerospace, military, automotive, and general industrial applications. Its aerospace products cover cargo fire barriers and materials for leading-edge protection and vibration and sound dampening. Military and defense offerings include seals and gaskets, thermal and electrical insulation materials, and weatherproofing materials.
In the auto sector, PolarSeal develops adhesive and sealing solutions for automotive electronics systems, airbag assemblies, interior trim, and other components. In one example, a major auto manufacturer approached PolarSeal after the redesign of a top-selling vehicle. A component near the car’s back wheel arch was found to be overheating, causing the rear passenger cabin to become overly hot. The problem created a comfort and safety issue for passengers and could have led to a huge loss of sales.
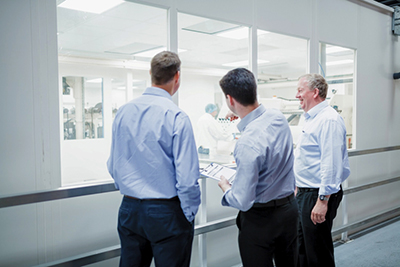
A technical team from PolarSeal was immediately dispatched to the manufacturer’s production line. Over the next few days, the team devised a solution consisting of a reflective foil with self-adhesive backing to deflect and dissipate the heat. The team designed a prototype part that was properly sized and could be installed without any changes to the existing production process. The next step was creating a tool that would die-cut the part. Within a week, the new part was in production at PolarSeal and shipments were on their way to the auto manufacturer.
It was business as usual for a company known as “the engineer’s dream.”