A King of Shrink Contender
- Published: March 31, 2005, By Yolanda Simonsis, Associate Publisher/Editor
Shrink Sleeves
Decades ago, Elvis firmly established Memphis, TN, as home to where records and kings are made. David Seuss, VP of sales for fourth-generation-owned Color Craft Label Co. (a dynasty in its own right), also in Memphis, has his own hopes and dreams. No more-pleasing music to the ear could be heard than for Color Craft some day to be crowned king of shrink sleeves. As the firm expands into flexible packaging with its new Comco MSP (multi-substrate press) and Stanford slitter/rewinder, seamer, and inspection/doctor machine, Color Craft’s new flexible packaging division is humming right along toward a new destiny, making records of its own.
Established in 1964 as a division of Memphis Engraving with roots back to 1924, Color Craft now has six facilities comprising a total of 110,000 sq ft of manufacturing space. The firm is divided into three business groups: labels and tags; digital printing; and the new 24,000-sq-ft flexible packaging division, formed in 2004 and housing the most recent equipment purchases that Seuss believes will take Color Craft to new heights.
Many in the label converting business have encountered shrinking profit margins, says Seuss, due in part to increasing material costs. Ironically, he sees shrink labels as the industry’s savior. "Your stores, your shops, your Wal-Marts dictate packaging, so other people follow along. Various industries, like the dry creamer industry, have gone all shrink sleeve when they used to be litho label," Seuss observes. And other packaged products, he says, are continuing the trend toward unsupported film labeling.
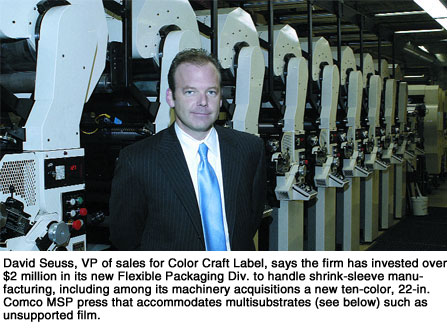
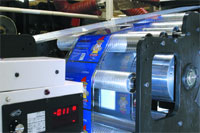
"The 360-degree graphics of shrink sleeve have made a big difference. For just a little bit more than it costs to produce standard pressure-sensitive labels on a press," Seuss says, "you can produce [on the Comco press] a label for the whole container—and you have a lot better look on the shelf." Seuss reveals the company’s investment in its flexible packaging division will be the focus for several years to come, although investment in p-s equipment may come as the result of success with shrink-sleeve labels.
All in the Numbers
Another reason for moving toward shrink-sleeve labels is in the numbers, says Seuss. Saturation of the p-s label market, he claims, is high. "In the United States there are quite a few pressure-sensitive label converters—somewhere around 3,000—but 60 to 80 percent of the shrink-sleeve market is pretty much controlled by six companies. I like the odds of that a little bit better than what I’m competing with daily now. Plus everybody doesn’t have the same type of equipment, so you’re able to compete with machine rates and not necessarily material costs on which the pressure-sensitive market is largely driven.…There’s a need for smaller converters like Color Craft to service multi-skewed product lines."
Seuss feels shrink sleeves will not replace p-s labels, "but I think it will impact them. There are customers we do business with now—maybe 20 percent—using pressure-sensitive [labels] that are already using shrink sleeves. I think we’ll broaden what we can do for our existing client base and then expand to serve other customers as well."
From a materials consumption standpoint, shrink-sleeve labels also are more efficient for both converter and end-user alike. A p-s label converter accumulates a lot of matrix waste that’s typically landfilled at a high disposal cost. As well, for the end-user customer, the silicone-coated release liner also is unusable and thrown away.
"We have our margins we trim off [the shrink film web] for the registration marks, our density bars, and so forth, but we don’t have any matrix to pull off, nor a liner, so we’re eliminating a lot of waste. More material is used, but it’s all usable—assuming we’re not creating bad product."
Minimal Waste
Efficiency and minimizing waste are critical in any converting process, and like any orchestrated effort, the end product is only as good as the instruments used to manufacture it. Prepress begins in the CCL division with an Esko-Graphics CDI Spark imaging unit built specifically for the tag and label industry. Platemaking then is performed by DuPont Cyrel FAST equipment that requires no solvents for digital flexo plate processing in as little as 20 minutes.
Then plates are brought to the flexible packaging division for mounting on the company’s new ten-color, 22-in. Comco MSP multisubstrate press. Seuss was impressed with the versatility and flexibility of this press, capable of accommodating substrates from 0.5-mil unsupported film to 24-pt boardstock, although Color Craft concentrates on thinner materials from 0.5–4 mils. If required, Suess can run both p-s and shrink-sleeve materials on this press, although he plans to fill it primarily with shrink-sleeve jobs serving multi-skewed markets in the food, beverage, and automotive aftermarket. Polyvinyl chloride (PVC) and modified polyethylene terephthalate (PETG) comprise the lion’s share of the shrink-sleeve labels produced on this press. Water-based inks are used in either case from Environmental Ink, Monarch, and Wikoff. While servo technology is offered on the MSP from the manufacturer, Color Craft opted for a line-shafted system with auto- register, extended high-speed dryers, and a dual-chambered doctor blade system. Capable of speeds to 500 fpm, the MSP also is equipped with Enercon corona treaters to assure appropriate surface tension levels for application of water-based inks.

Heart and Soul
The heart and soul of the new division’s recent equipment purchases includes a slitter/rewinder, seamer, and inspector machine from Stanford Products. As with the Comco MSP press, speed, efficiency, and minimal waste are the hallmarks of these new investments, says Seuss. After printing, rolls are moved to the Stanford Model 738 slitter/rewinder in preparation for subsequent seaming. The cantilevered duplex differential center winder can accommodate 3- or 6-in. cores, reaching speeds to 1,500 fpm at 350 lbs/shaft with the unwind taking 700 lbs fully cantilevered. The slip differential feature is especially attractive for film webs, says Seuss, as it allows Color Craft to compensate for caliper variations or gauge bands due to print buildup or laminations in the product since each web is being wound at its own individual tension. A splice table allows convenient in-register splicing and the ability to easily set the razor-in-air knives.
After slitting, rolls move onto the Stanford Seammachine with patent-pending technology that allows increased speed and minimal waste. This equipment essentially is what makes or breaks a shrink-sleeve converting operation. Seuss explains the seamer "started off great at 1,000 feet per minute, but by the time Stanford finished its installation, it was up to 1,500 feet per minute. The last thing we wanted was to start off this business and fight the equipment the whole way through. So we opted for a more expensive product that would produce a better result without our running into equipment problems."
One of the unique features of the seamer that sets it apart from its competitors is an oscillating rewind that enhances the controllability of the machine, says Seuss. While an oscillating rewind is fairly standard among most seamer manufacturers, Stanford’s patent-pending version offers a new level of control. What makes the Seammachine exceptional is its ability is correlate the solvent seaming process—or rate of solvent delivery—to the web speed during production, including ramp-up, run time, and ramp-down. With the solvent delivery needle within only 1 mm from the material, and delivering as little as 2–3 mm of solvent, the operator is able to use only the amount necessary to achieve a solid bond and dispenses any need for an exhaust system to eliminate fumes.
In addition, the Seammachine allows the user to select various patterns of oscillation. Some theories in the field suggest certain patterns serve certain functions under specific circumstances, depending on such things as web width and material type. For example, one option is a square wave believed better suited to provide support for rolls on their side during shipping.
The machine, says Seuss, minimizes dependence on the skill of the operator, allowing automatic control through use of a touchscreen to designate how much solvent is used. The machine then takes care of metering the solvent at optimum speed, both at startup and the end of a run.
Closing the Loop
The final process for producing quality shrink-sleeve labels involves Stanford’s Model DM10/16 Inspector/Doctor machine, performing 100% inspection at speeds to 1,000 fpm. A finished layflat tube of shrink-sleeve labels is inflated and runs unremarkably on the Inspector unless it encounters a bad seam. At this point, a high-pitched noise is heard as a result of the air blowing across the deflated web. Additionally, a camera is used in combination with a black light to illuminate an optical marker in the solvent, providing the operator another means for checking the integrity of the seam. After removing any noncompliant material, the operator can splice the tube together and re-inflate the tube to continue inspection. An oscillating rewinding process assures a smooth and flat finished roll, says Seuss.
Color Craft has set a target to raise sales for the flexible packaging division to realize a 40% company-wide increase in sales within 18 months. It’s ambitious but not unrealistic for a company that’s no stranger to record-making in the land of rock ‘n’ roll. "At that time," says David Seuss with a smile, "we’ll look at buying more equipment."
CONVERTER INFO:
Color Craft Label Co.
15B Vance Ave.
Memphis, TN 38103
901/525-4762; colorcraftlabel.com
SUPPLIER INFO:
Comco—comcointl.com
Stanford—stanfordproductsllc.com
Esko Graphics—esko-graphics.com
DuPont Cyrel—cyrel.dupont.com
Environmental Inks and Coatings—envinks.com
Monarch Color Corp. —monarchcolor.com
Wikoff Color Corp. —wikoff.com
Enercon—enerconind.com