Plastics Recycling: Reclaim & Reuse
- Published: September 01, 2010, By Edited by Claudia Hine, Managing Editor
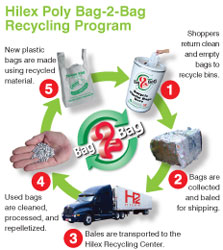
Hilex Poly's pioneering development of postconsumer recycling began with its Bag-2-Bag in-store recycling program, launched in 2005. Since then, the company has placed more than 30,000 collection bins in stores and other locations throughout the US. Today, the company's “Grey is the New Green” bag, with a minimum of 30% recycled material, is an industry standard of success, and the bag itself is an emblem of environmental responsibility that can be carried proudly by environmentally concerned consumers across America.
On January 7, Hilex Poly cut the ribbon to an expansion of its North Vernon, IN, facility, first opened in early 2005. The expansion includes more room for reclaim storage and staging as well as more production muscle. It also brings 21 new jobs, for a total of 270, to North Vernon.
In this facility, material from strategically located collection centers is sorted, shredded, washed, and processed. To ensure quality bags, Hilex Poly worked with EREMA North America, a company dedicated to plastics recycling with more than 3,500 systems in operation throughout the world.
Mark Daniels, Hilex Poly VP of marketing and environmental affairs, says, “We knew EREMA equipment and were comfortable with it and especially appreciated how easily our older equipment could be integrated into a new configuration. We also value EREMA's global recycling experience under a large diversity of conditions and were confident their expertise would deliver the quality we require.”
In the basic EREMA system, scrap material is fed into a vertical densifying unit that uses friction to compress and preheat the plastic. The preheated, densified material is then fed directly to the extruder screw. Compression and melting occur gradually, at a precisely controlled temperature, adding minimal heat history to the reclaim, which significantly contributes to the quality of the finished material. This especially important with postconsumer waste because some of it may be reprocessed over and over again.
Working with EREMA, Hilex Poly took its standard system and custom-configured a model TVE arrangement with a self-cleaning laser filter. Along with the vented extruder that eliminates gases produced by inks and other contaminants, the laser filter effectively and continuously separates remaining larger solids, contributing to the high quality of the reclaim.
The filter discs, which each contain approximately a half-million laser-drilled holes, form a sandwich-like configuration in which the contaminated melt flows from the middle out. The contamination is held back on the disc while a rotary scraper wipes it clean and extrudes the contaminated waste out of the laser filter assembly. The laser filter is engineered to maintain a stable pressure beyond the filter, thus ensuring consistent production flow.
The result is a system proficient at removing the small amounts of contamination that survive Hilex Poly's inspection and washing processes and that is able to deliver the type of pellets Hilex Poly's commitment to quality requires. The final, effective removal of minute quantities of contamination ensures a film and bag free of structural flaws that can reduce strength and reliability.
“The last thing we want is one of our bags in the hands of a customer failing in the parking lot. The EREMA system's ability to filter lingering contamination and protect the quality of the material by imparting minimal heat history are critical to our production of the top quality, useful, reliable bags our customers require,” Daniels says.
There's More to It Than Hardware
According to Daniels, in addition to deploying effective technology, much of what makes postconsumer recycling sustainable comes from less easily defined practices, including a fine-tuned approach to collection that ensures a continuous, relatively clean volume of raw postconsumer material. This fine-tuning includes carefully located and diligently maintained collection stations, a carefully crafted, ongoing public and store employee education process, and cost-effective transportation. To be effective, a postconsumer recycling program needs to be disciplined with every aspect examined and every bit of unnecessary cost eliminated.
“Our recycling program is easy to use for our customers and their customers. We work continually to remind customers about the importance of keeping contamination out of the bins. Over time, as the program is in place and the public is educated, the waste stream quality improves, and our production practices become more efficient. For a smooth operation and long term success, our efforts at every stage must be smart, diligent, and disciplined,” Daniels says.
“People like plastic bags. After they unpack the groceries, they use them for any number of things from storage to can liners to pet waste containment. For those plastic bags that are not reused, more and more people are bringing their bags back to our bins. People believe recycling is the right thing to do, and we help them do it.
“When it comes to carbon footprint, plastic has a real advantage over the alternatives. For example, it takes seven truck loads to bring a store the same number of paper bags as the recycled plastic bags we can bring in one truck.”
Converter Info
- Hilex Poly Co. | 101 E. Carolina Ave., Hartsville, SC 29550 | 843-857-4800 | www.hilexpoly.com
Supplier Info
- EREMA North America | www.erema.net
Circle 303 or visit
www.freeproductinfo.net/pff