Fluid Coating & Extrusion Coating: What Is the Difference?
- Published: November 04, 2011
Here are a few tips to help you choose the best coating method for your product.
There seems to be some confusion when it comes to the terms "fluid coating" and "extrusion coating" in roll-to-roll processing. We can clear this up, but first we have to confuse you. Fluid coating is a general term that refers to applying a fluid to a substrate. Extrusion coating refers to applying a fluid to a substrate. What?
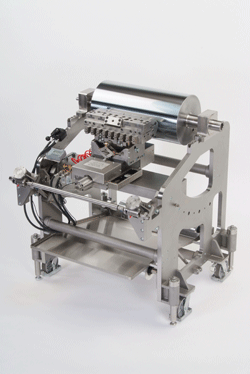
In a fluid coating operation, fluid is pumped from a tank to the coating head and distributed across the width of the substrate. Photo courtesy Extrusion Dies Industries (EDI).
Fluid Coating
In a fluid coating operation, the fluid can be room temperature or heated. The fluid is pumped from a tank to the coating head and distributed across the width of the substrate. This fluid is then cured through application of some type of energy (oven heat, ultraviolet light, etc.). The final construction in a coating application is a cured fluid on a paper, film, or foil--imagine a roll of tape.
Extrusion Coating
In an extrusion coating application, the fluid is an extruded polymer. Pellets of a given polymer are compounded in an extruder and processed to the extrusion die. The extrusion die is positioned above a substrate, and the polymer melt (fluid) is cast onto the paper, film, or foil to form a film--imagine a wax-coated paper.
So the main difference between fluid coating and extrusion coating starts at the raw material handling. The liquid in a fluid coating operation is pumped, while the "fluid" of an extrusion coating operation is compounded. But it’s not that simple. Some liquids in a fluid coating operation can benefit from compounding elements in an extruder prior to transport to the coating head. So the presence of an extruder does not mean that the process operation is extrusion coating.
How about the arrangement of the extrusion/coating head? In extrusion coating, the extrusion head is positioned above the system and cast down on the substrate. However, in a curtain coating arrangement, a slot die also would be positioned above the substrate. So how do we keep it straight?
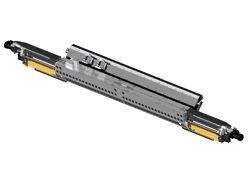
In an extrusion coating application, pellets of a given polymer are compounded in an extruder and processed to the extrusion die. Photo courtesy Extrusion Dies Industries (EDI).
Lamination
Lamination of layers may be where we can understand the difference. Let’s say you have a multilayer package with the first substrate of paper, the second polyethylene (PE), and the third foil. How can we put this together?
With fluid coating, we could coat the paper with adhesive, coat the foil with adhesive, and sandwich the PE via a nip. If we opted for extrusion coating, we could cast a PE film directly to the paper and foil at a nip operation. The final structure would functionally be the same, but the process involved would be drastically different.
While the extrusion-coated package has a paper and foil, with the PE acting as the tie-layer, the adhesive-coated package has paper, foil, and PE as substrates, while the two adhesive coatings act as tie-layers.
So why choose extrusion coating over fluid coating or fluid coating over extrusion coating for this product? The extrusion coating of PE would have fewer process steps but also limit the flexibility of changing out the PE chemistry, which may limit the performance of the final construction. The fluid coating of adhesive would provide for flexibility in developing bonds of various strength between the layers but would require purchase of a PE substrate in addition to paper and foil.
The final answer is: It depends! What are you trying to accomplish in the final product construction? What equipment do you have? How vertically integrated is your operation? The list goes on. The final destination may look similar, but the paths of fluid coating and extrusion coating are drastically different.
Happy coating--with whatever method you choose!
Roll-to-roll coating industry expert Mark Miller, owner of Coating Tech Service, has 14+ years of slot die coating experience and troubleshooting. Contact him at 612-605-6019; mark@coatingtechservice.com; http://www.coatingtechservice.com.