Coating Matters | Computational Methods Beyond Fluid Flow Analysis
- Published: December 07, 2016, By Mark Miller
If coating equipment has been tested in the computational world, the design will be more robust and the equipment will be more capable.
If you'd like to hear from Mark Miller's own lips rather than read his column, titled "Coating Matters | Computational Methods Beyond Fluid Flow Analysis," click on his podcast below:
{mp3}computational-methods-voice{/mp3}
Finite Element Analysis is commonly utilized in understanding, designing, and manufacturing pre-metered coating equipment. But the use of FEA is not limited to understanding fluid flow. It also can be utilized to determine the structural strength of the equipment and the temperature effect of a heated slot die. Outside of fluid flow analysis, FEA is utilized to understand static and dynamic stresses in structural design, linear and nonlinear functionality, heat transfer, and acoustics.
Prior to computational methods, the understanding of the structural stresses of a designed piece of equipment was limited to simple mathematical analysis of one variable at a time. FEA allows the designer to visualize multiple effects at once. In slot die coating application, the effects of the fluid, heating or cooling, and physical stresses need to be considered to develop the precision required in modern coating applications.
Similar to fluid flow analysis, a section of the design is developed into a mesh and the potential stresses are placed on the equipment to see the effects. The design can then be altered to reduce the resultant stressors. The goal is to understand all stresses that are acting on a mechanical design at once. This multi-factorial understanding is difficult without computational methods. The resultant study can provide insight into axial stress, bending, shear, and torsional effects.
Unlike fluid flow analysis, the use of FEA is more straightforward because of the inherent boundary conditions in the equipment. Whether the study is looking for physical strain or temperature effects, the equipment is a closed system of study. The designed geometry is broken into equivalent sized sections (finite elements) that share common boundary lines. These similar sections, sharing a common boundary, can then be assessed for the limits the equipment will see on the production floor. The design can be modified and re-analyzed as the stress vectors are realized.
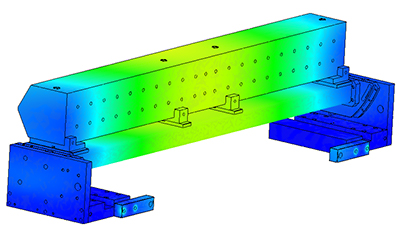
To say that FEA of structural components is simple is not true, however. As pre-metered coating is requiring the equipment to coat fluids thinner, faster, and more precise, the effects of physical or temperature effects need to be more accurately understood. The geometries of the mechanical components can be more complicated and the effects on minor and major components need to be considered in addition to the interactions. Prior to computational method development, the use of simplified models and simplified mathematical equations were utilized with less precision. With FEA, the study of irregular shapes, geometries, boundaries, various loads, and different materials of construction can be completed. Computational studies also take a tremendous amount of time for study and analysis in addition to assessment, re-design, and further analysis.
Not all materials can be studied easily, however. Irregular materials, compounds, or deformation of rubbery items are difficult to understand via FEA. The more rigid the materials and more solid the geometry, the more easily the FEA study is to complete. With these complicated materials or geometries, an incremental and iterative approach may be required.
The use of computation methods to design mechanical equipment, as coating equipment requires more precision, leads to more confidence in the design and use of the equipment. If the equipment to be utilized has been tested in the computational world, then the design will be more robust and the resulting coating equipment will be more capable.
Mark D. Miller, author of PFFC's Coating Matters column, is a fluid coating expert with experience and knowledge in the converting industry accumulated since 1996. Mark holds a Bachelor's degree in Chemical Engineering from the Univ. of Wisconsin-Madison and a Master's degree in Polymer Science & Engineering from Lehigh Univ. and a Juris Doctor from Hamline Univ. Mark is a technical consultant and CEO of Coating Tech Service LLC. He has worked in web coating technologies and chemical manufacturing operations and is a certified Six Sigma Black Belt trained in both DMAIC and DFSS disciplines. Coating Tech Service provides process troubleshooting and project management for precision coated products. Mark has extensive process knowledge in high precision coating applications including thin film photo voltaic, Li-Ion battery, and optical systems technology. Mark has been integral to new developments and technology that minimize product waste and improve process scalability.