Coating Matters | Pre-Metered Fluid Flow Analysis with Computational Methods
- Published: November 28, 2016, By Mark Miller
By taking a finite section of fluid flow within a slot die, one can understand the flow as it is affected by a number of factors.
If you'd like to hear from Mark Miller's own lips rather than read his column, titled "Coating Matters | Pre-Metered Fluid Flow Analysis with Computational Methods," click on his podcast below:
{mp3}pre-metered-fluid-flow-voice{/mp3}
As the world of liquid coating has advanced, so has the design and manufacturing of the equipment. In the world of pre-metered coating, slot die technology has progressed rapidly since its early years because of computer simulation. The ability to take the rheological fluid characteristics and the process set points to properly design the internal manifold of the slot die is now not only possible, but sometimes necessary.
There are four areas that are of interest to the fluid coating operator
- Analysis of process conditions for stable flow.
- Internal flow conditions that cause defects.
- Coating window determination and when defects occur.
- Start and stop phenomenon.
A computer model does better with boundary conditions, so the study of internal flow within a coating head is easier than coating behavior outside the coating head. In the study of flow within an enclosed coating head, the fluid can be studied as a smaller section and expanded across the full coating width. This small section analysis is called Computation Flow Dynamics or Finite Element Analysis (FEA).
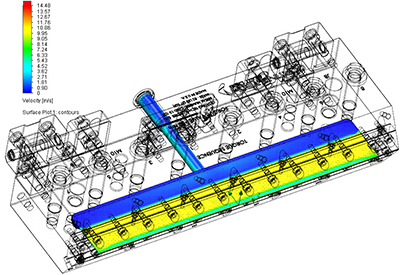
By taking a finite, defined section of fluid flow within a slot die, one can understand the flow as it is affected by volumetric changes, shear of mechanical spaces, pressure differences, and velocity gradients. FEA takes the sections determined by the computer, and a mesh of these sections is formed, and the effects of the flow are determined. This can take a high-powered computer hours to complete for accurate understanding.
Within the multi-factorial analysis, the simulation can tell a trained designer where the shape and design of the coating head’s internal flow geometry needs to be adjusted in order to control flow as it exists in the slot die. Geometries such as fluid inlet sweeps, manifold end sweeps, and transitional radii are not easily accounted for unless three-dimensional flow modeling is employed.
Within the slot die manifold, a particle study can provide an understanding of residence time, agglomeration of suspended particles, and potential dead zones for fluid flow. For some fluids, the dead zone areas can lead to particle build up or excessive temperature issues. The manifold study with a computational method takes the basics of finite element analysis and applies them to a strong understanding of flow control.
In a perfectly uniform coating flow, two-dimensional steady flow would be all that is required to develop a model. However, if a coating defect is created at a set process condition, the use of three-dimensional computational studies allows for an understanding of the fluid effects of mechanical dimensional changes. The final point of the slot die exit is the slot gap, where the fluid should be moving at constant velocity, pressure, volumetric flow rate, and viscosity.
After the fluid exits the slot die, more empirical equations need to be utilized because of the lack of boundary conditions and the effect of the production environment. Determining the coating window includes the simulated optimum coating condition at the slot die exit in addition to the effects of the moving substrate and the air barrier between the fluid and substrate. Considering the flow outside the slot die as you do within the slot die does not work as well as one would expect, but it is a good starting point.
The most complicated coating issues are typically associated with the start and stop of coating onto a substrate. Whether the start and stop is associated with a splice of the substrate or a planned intermittent coating pattern, the need to reduce scrap and control flow is still there.
While no single computational algorithm has been presented to understand all the coating effects with various fluids on substrates in all environmental conditions, the control of the flow of fluid out of the slot die is the best starting point. Maintaining consistent viscosity, velocity, pressure and volumetric flow rate across the full coating width of the slot die will lead to better start and stop control.
Prior to the use of computer modeling of fluid flow, experimentation was the only option. Slow and expensive, empirical modeling based off past experience did not allow for exacting design and manufacturing. In addition to being costly, the experimental variation makes multi-factorial understanding difficult. The precision developed through computer simulations allows for coating nanowire suspended fluids and optically clear coatings without the guesswork. As coating production goes faster and thinner with more complex fluids, computer simulation and design is sometimes the only option.
Mark D. Miller, author of PFFC's Coating Matters column, is a fluid coating expert with experience and knowledge in the converting industry accumulated since 1996. Mark holds a Bachelor's degree in Chemical Engineering from the Univ. of Wisconsin-Madison and a Master's degree in Polymer Science & Engineering from Lehigh Univ. and a Juris Doctor from Hamline Univ. Mark is a technical consultant and CEO of Coating Tech Service LLC. He has worked in web coating technologies and chemical manufacturing operations and is a certified Six Sigma Black Belt trained in both DMAIC and DFSS disciplines. Coating Tech Service provides process troubleshooting and project management for precision coated products. Mark has extensive process knowledge in high precision coating applications including thin film photo voltaic, Li-Ion battery, and optical systems technology. Mark has been integral to new developments and technology that minimize product waste and improve process scalability.