Coating Matters | Fluid Delivery System Design for Coating Control
- Published: May 24, 2016, By Mark Miller
Choosing the right pump for the application can make or break your coating application.
If you'd like to hear from Mark Miller's own lips rather than read his column, titled "Coating Matters | Fluid Delivery System Design for Coating Control," click on his podcast below:
{mp3}fluid-delivery-system-design-voice{/mp3}
There are five variables that determine coating capability:
- Coating head (design and precision)
- Backing roll (precision)
- Positioner (repeatability)
- Substrate (speed, control, and quality)
- Fluid delivery system (precision and stability)
One of the variables that is commonly overlooked is the back end of the system—the pump. Choosing the right pump for the application and making sure the right auxiliary equipment is utilized can make or break your coating application.
In pre-metered coating methods, like slot die coating technology, the need for a precise and stable feed of fluid is critical. This narrows the decision for the pump down to equipment that is strictly positive displacement. There are a number of positive displacement pumps available in the marketplace:
- Gear pump
- Progressive Cavity pump
- Pulseless Diaphragm pump
- Pressure Pot
- Syringe pump
The reason to choose one pump over another is based on an understanding of the fluid, application, and process needs. As an example, a gear pump is great for many positive displacement applications, but it fails for many UV curable fluid systems. UV curable fluids can cure due to light energy, heat, or shear. The shear imposed by the gear pump can quickly turn your fluid into a solid and your pump into a boat anchor.
In addition to choosing the right pump for the application, consideration of flow control needs to be reviewed. A fluid delivery system can be simple or complex. For many applications, the pump and feed lines, along with a pressure gauge prior to the coating head is all that is required for optimum coating. However, complex flow sometimes requires complex fluid delivery systems and additional equipment.
The path of fluid delivery can start at a tank, go through the pump, and end at the pressure gauge prior to the coating head, but here is a list of all potential equipment for a more robust (and complex) fluid delivery system:
- Tank
- Mixer
- Temperature control
- Pump
- Hoses/piping and recirculation
- Flow meter/viscometer
- Filtration
- Air removal
- In-line injection/static mixer (and pressure gauge)
Now you can imagine that the cost associated with the system grows with complexity, so it is important to know what is critical to your coating application, and what is nice to have but not necessary.
Tank
Material of construction and sizing of the tank are important parameters to consider for the fluid coating application. In addition, reduction of air entrainment is critical for improved performance. The size should work for a full shift of operation and multiple tanks should be considered for non-stop operation. Pumping fluid into the day tank typically requires some settling time, in terms of air reduction (bubble rise time) and temperature stability.
Mixer
Agitation of the fluid to keep homogeneity is important, but excessive mixing can lead to introduction of air. Air is the ultimate evil in coating, so finding the right type, size, and speed of mixing is important for proper operation at steady state for fluid coating. A large mixing element run at low speed produces larger flow with less shearing action. Inversely, a smaller mixing element run at fast speeds creates less flow with more shearing action.
Temperature control
Maintaining a fluid at a constant temperature is helpful in maintaining flow control. If you have every completed rheological curves for your fluid, you can see the difference a few degrees of temperature can provide. Consideration of the tank volume and mass of fluid is important, but also the fluid flow path between the tank and the coating head should be analyzed for temperature variation in the process.
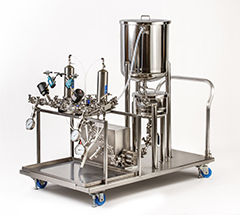
Pump
As previously mentioned, the choice of the pump is important for the application because of the method in which the pump moves the fluid forward. In all positive displacement systems, the fluid is constantly moving forward. However, the fluid may be pushed, sheared, or handled differently. Regardless of the pump you choose, the key is to develop consistently smooth flow. A pump operates within a range of flow rates. The best operating window for the pump should be maintained, and if you play too close to the edge of the optimized range, the results could be detrimental to the coating performance.
Hoses/piping and recirculation
Material choice and pressure calculations are critical in determining the path of flow control for the fluid. To reduce air defects that occur through air entrainment, make sure the path of fluid flow is always uphill. Any dip in the hose/pipe path is a potential place for air bubbles to sit and slowly bleed off into the process. Any bends in the pipe flow is a curved settlement area where air will slowly leak into the coating head, showing up as random and difficult to diagnose bubble defects. If a curve is necessary in the pipe path, a relief valve will help. In addition to the choice of rigid versus flexible piping, the consideration of fitting types should be scrutinized. Every connection is a seal where air could be introduced. Sanitary fittings are typically the best choice for ease of use and reduced air seal leaks. Finally, consideration of the distance traveled is important. Reduce turns, move uphill, and reduce the path traveled. Now, once you reach the coating head, it is a good idea (in some applications) to design the flow path as a recirculation loop back to the tank. This allows the fluid to constantly be in motion, and at steady state, when the applicator is turned on and coating occurs.
Flow meter/viscometer
A flow meter can be essential for some coating applications. The ability to measure the inline flow and adjust accordingly with the pump rate allows for a process control loop. This process control loop can provide the necessary data points to troubleshoot a coating defect or improve coat weight uniformity on the fly. Some simple systems allow for an obstructive flow measurement, but utilizing a non-obstructive flow meter is preferred to reduce potential contamination. More complex flow meters also can measure viscosity in-line. This can have the added benefit of developing a deeper understanding of the rheological characteristic of flow and adjust via a control loop. If a set viscosity needs to be maintained, an in-line injection port can be added to introduce solvents and maintain viscosity.
Filtration
Air is the ultimate enemy in coating applications, but unfiltered debris is a close second. Contamination that filters pick up allows the fluid to be processed as a clean coating and common defects are avoided. Filters are not always required in coating applications, but determination of the proper size and filter type can make large improvements in the fluid flow to the coating head. In the worst case scenario, a tight mesh filter can clog quickly and obstruct flow to the coating head. In the best case scenario, the filter will capture contaminates and maintain a steady state flow to the coating head. It is always a good idea to run filters in parallel to allow for changing filters while maintaining fluid flow. It is not economically feasible to shut down the line to change filters. Filtration choice depends on the material compatibility, particle size, and pressure differential expected.
Air removal
Air removal as a separate unit operation in the fluid delivery system can be considered if fluid settling time in the tank is not an option. Temperature and pressure can be considered to encourage bubble rise time and air removal. Ultrasonic measures have been utilized to reduce bubbles, but these have had mixed results. Ultimately, time at fluid preparation is the best option, but in-line systems can be helpful.
In-line injection/static mixer (and pressure gauge)
The coating station should be the highest point of the fluid delivery path. Prior to the entrance to the coating head, a pressure sensor will allow an understanding of all the effects of the equipment installed prior to the coating head. Pressure gauges can be utilized throughout the fluid delivery system, but the most critical point is prior to the coating head. An air relief valve also will be able to be installed to make sure the system is free of air prior to entrance to the coating head. The relief valve would not be necessary if the coating head is installed at an angle and the fluid releases out of the coating head at the highest flow path point. Prior to the pressure gauge and air relief valve, a static mixer can be introduced to allow for a homogenous fluid prior to coating. This is most critical if the fluid is heated, higher in viscosity or viscoelastic in nature, and exhibits a low Reynolds number. Because of the resultant laminar flow, additional mixing may be required. In-line injection is helpful to provide additional solvent to obtain proper viscosity or to add a reactive ingredient prior to coating. In-line injection and a static mixer typically are utilized in combination for optimum effects.
Now, all the components listed here are great to consider for your fluid coating application, but they are not all necessary. Make a practical consideration of the fluid coating requirements, the equipment to best fit your application, and install what will allow you to be successful. The fluid delivery system needs to be a precise and accurate tool so your coating will perform and meet the tolerances required. Placing these pieces of equipment in the proper order and control scheme will create an optimum flow path for your application.
Mark D. Miller, author of PFFC's Coating Matters column, is a fluid coating expert with experience and knowledge in the converting industry accumulated since 1996. Mark holds a Bachelor's degree in Chemical Engineering from the Univ. of Wisconsin-Madison and a Master's degree in Polymer Science & Engineering from Lehigh Univ. and a Juris Doctor from Hamline Univ. Mark is a technical consultant and CEO of Coating Tech Service LLC. He has worked in web coating technologies and chemical manufacturing operations and is a certified Six Sigma Black Belt trained in both DMAIC and DFSS disciplines. Coating Tech Service provides process troubleshooting and project management for precision coated products. Mark has extensive process knowledge in high precision coating applications including thin film photo voltaic, Li-Ion battery, and optical systems technology. Mark has been integral to new developments and technology that minimize product waste and improve process scalability.