Coating | Solution Delivery for High-Precision Coating, Pt. 1
- Published: February 09, 2016, By Todd Arndorfer, Carestream Contract Manufacturing
Do the upfront work of characterizing the solution properties and understanding the product requirements to create a well-designed delivery system.
Precision coating encompasses sophisticated, highly controlled functions, including distribution of liquid across a conveying web and control of coating thickness in the down-web direction. Uniform coatings require precise fluid metering, precision coating heads, and tight conveyance speed and tension controls. Thus, an operation’s capabilities are partially defined by the quality and accuracy of solution delivery systems—how the fluid gets to the coating method.
There are pre-metered and self-metered coating methods. In pre-metered methods, including curtain, slide, and slot coating, the coating thickness is determined by the flow rate upstream of the coater (see Figure 1).
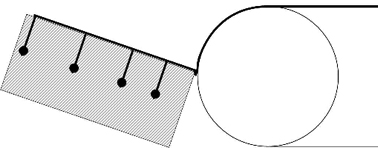
In self-metered coating methods (gravure, forward-roll, and knife), coating thickness is determined by interactions between the fluid and the coating device (see Figure 2). The solution delivery system is much more critical in a pre-metered coating process, so this article focuses on that type.
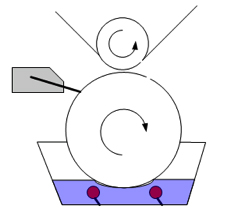
This article series will detail the requirements for advanced solution delivery and provide advice for ensuring optimum product quality and cost control. Each of these goals is satisfied with an operationally sound process that ensures technical efficiency. From pressurizing the solution and purging the system through to mixing and recycling the solution, the steps must be clear and well established.
In Part 1, we will focus on the pre-work and approach to design or adapting a solution delivery system. Part 2 will then cover how to optimize the performance of the system to improve product quality and yield.
Steps for Creating a Solution Delivery System
For precision coating, solution delivery systems should be able to provide accurate flow over a range of rates so the final coated product thickness can be calculated and controlled. The system should be designed to supply the solution free of contaminants to prevent surface defects and avoid degrading product performance. It should quickly and completely purge air or solvent from the lines and coating die, so the solution is homogeneous when coated on the substrate.
Controlling temperature is important to provide uniform viscosity to avoid impacting coated thickness uniformity. For long coating runs, the ability to start and stop flow quickly and change filters and tanks on the fly will help to minimize solution waste.
The recommended steps for creating a robust solution delivery system are to do the following:
- Characterize the solution properties
- Understand the coated product requirements
- Select the appropriate system components
- Define the complete system and control methods
- Define purging and cleaning methods
- Test and optimize the complete system
The first two steps—characterizing the solution and understanding the product requirements—are the foundation for solution delivery design. These first two steps are needed to make trials and initial production runs more efficient with fewer surprises, better safety, fewer filter changes and pumping failures, and ultimately provide faster scale-up and better product quality.
Characterize Coating Solution Properties
Thorough research and lab work on the solution properties should never be skipped; it will help in properly designing each component of the solution delivery system appropriately to avoid scale-up pitfalls. Rheology is the viscosity change of a solution with shear or flow. Consider two solutions that both have high viscosity at low shear; one has a flat Newtonian shear response and the other is shear thinning where the viscosity drops at high shear or pumping rates. The pump pressure and line size required for the Newtonian solution will be much higher than for the shear thinning solution.
Does the solution have dispersed particles? If so, a tight clearance gear pump may not be the right choice since abrasive particles could cause premature pump wear or the gears could damage the particles themselves. What is their size distribution and frequency of the particles? This information will help determine the filtration size and type. Some solutions, in particular aqueous lattices, are very sensitive to pumping, so a low shear progressive cavity pump would be a good choice to avoid coagulation of the polymer.
Understand the Product Requirements
The solution delivery system must ultimately be able to meet the product’s key specifications and quality requirements in conjunction with the coating method. By combining the wet coating thickness, coating speed, and width, one can calculate the solution flow rate to properly size the pump and piping or hoses.
What is the acceptable product thickness variation cross-web and down-web? If a very tight +/- 2% is required, then a high-precision gear pump and finely tuned flowmeter will be required. Also, consider the maximum acceptable size and frequency of point defects. If the product is for an optical application like a touch screen film, then particles as small as 5 microns may need to be eliminated by very fine filtration. Such fine filtration may result in higher pressure loss, so additional pumping capacity may be needed. Also, providing a way to monitor the pressure drop across the filter will enable proactive filter changes rather than unplanned plugging and product loss.
Select Solution System Components and Define the Complete Solution Delivery System
Figure 3 shows a system for precision high-speed curtain coating.
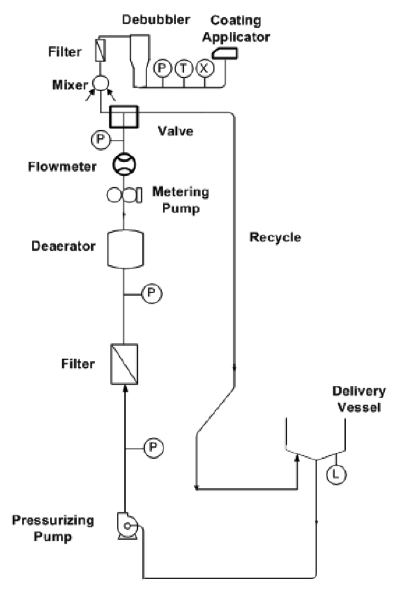
Based on what you have learned from characterizing the solution and understanding the product requirements, choose the components of the system that are critical to your particular needs. Adding components that do not add value to the product or improve process efficiency are unnecessary both for cost and complexity.
Pressurize the Solution
Pressurization provides a driving force that enables the solution to flow through system components. First, calculate pressure drop across each system component using solution fluid dynamics models with solution flow rate and rheology as inputs. Then, knowing the desired coating die pressure, it is possible to select the right pump size and the pump type for the shear sensitivity and particle considerations described earlier. Also, be sure to size the pump with surge capacity to deliver enough flow for the purge rates required.
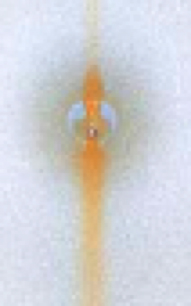
To avoid contaminants, choose pump, filtration, and tubing materials that will not be damaged by or interact with the solution. For example, you’ll need to select the proper grade of stainless steel to withstand acidic and corrosive solutions, or the right filter and hose polymer types to resist the solvents present in the solution or cleaning fluids.
Filter the Solution
Based on the solution particle size and frequency characterization, choose a filter type such as bag, cartridge, or depth with the appropriate micron rating for the product quality requirements and that can handle the expected particle load with a reasonable life. Offline tests can be done to verify filtration effectiveness, plugging rate, and pressure drop.
Particle sizing of the solution pre- and post-filtration is an excellent way to check filter manufacturer claims and to make sure that the canisters are not allowing fluid to bypass the filter media. Effective filtration will help prevent coated defects like the comet shown in Figure 4 and Figure 5.
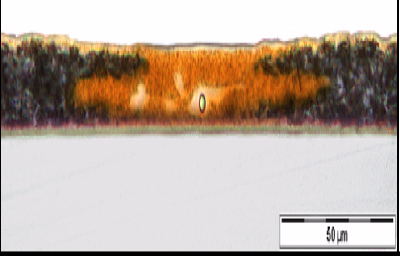
Remove Air
The best way to prevent air bubbles from disturbing the coating is to avoid entraining air during mixing and other upstream solution transfer processes. If bubbles or voids that can cause lines, streaks, and spot defects are of concern for the final product, then consider degassing the solution by applying a vacuum to the solution tank or eliminating bubbles inline via an ultrasonic horn.
It is best to place inline degassing as close to the coating die as possible. Avoid poor line geometries such as abrupt diameter changes, loops, or downward sloping areas that can trap air bubbles. Also, smaller piping diameters make it easier to purge air, but this must be balanced with pressure drop for pumping.
For longer runs where multiple filter and tank changes would be expected, plan to have automated valving to minimize adding air to the system and avoid the associated downtime and waste.
Incorporate Active Ingredients
If a crosslinker or a degradation-sensitive active ingredient needs to be added, consider inline mixing that component just prior to the coating head rather than in the tank. Test whether static mixing is sufficient to incorporate the inline addition or whether powered dynamic mixing will be required.
Control Temperature
Good temperature control of the coating solution (+/- 2 deg C) is needed to regulate solution viscosity and ensure smooth delivery. If the coating die and solution are not at the same temperature, down-web thickness can change as the die heats or cools. Non-isothermal operation of curtain, slide, or slot coating applicators can lead to cross-web anomalies and defects that can be avoided by jacketing tanks and delivery lines and monitoring temperature.
Control Flow
For pre-metered coating, it is recommended to use a flowmeter with a feedback control loop to the pump. This setup will provide more stable flow by automatically compensating for changes in tank liquid level, solution viscosity, and filter backpressure. Such a system can potentially avoid the need for post-coating thickness verification.
Figure 6 is a schematic of a typically closed-loop flow control system.
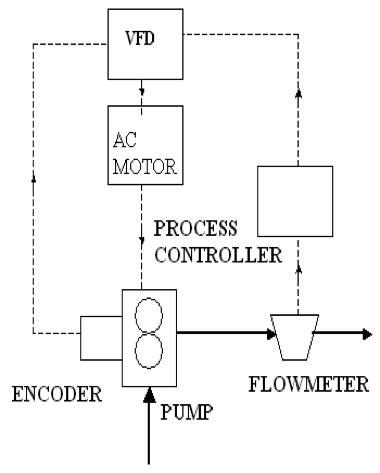
When choosing a flowmeter, be sure to consider how easily it can be cleaned in combination with the contamination potential of the coating solution.
In summary, the upfront work of characterizing the solution properties and understanding the product requirements are the most important steps in creating a well-designed and robust solution delivery system for high-precision coating. Once all the components have been selected and assembled, it is time to test the system functionality. Next month, Part 2 of this article will cover how to get the system up and running, optimize its performance, and maintain it for the long term.
ABOUT THE AUTHOR
As business development manager at Carestream Contract Manufacturing, Todd Arndorfer identifies, attracts, and commercializes new manufacturing business for Carestream's polyester film and precision coating assets. Throughout his previous six-year tenure managing manufacturing operations at Carestream Health Colorado, Arndorfer increased profit and led step change improvements in safety, quality, and delivery. Over the course of his 26-year career, Arndorfer has also held product development and process engineering roles at several other locations, including Ferrania, Italy, and Rochester, NY. Arndorfer earned his B.S. in chemical engineering at the University of Wisconsin-Madison. Contact him at todd.arndorfer@carestream.com,
Part 2 of this article will appear in March 2016.