Packaging Buzz at Drupa Was Large - Very Large
- Published: August 01, 2008, By By Jörg Dähnhardt, Heidelberg USA
Packaging was certainly a hot topic at Drupa this year, with new technologies on display for all areas. Perhaps the most buzz came from the largest machines — very large format (VLF) presses that are defined as larger than 41-in. sheet width but typically 50 in. and more.
It's important to utilize time efficiently in the pressroom while gaining greater control over the entire printing and manufacturing process. This is where VLF comes in. The productivity increase potential for shops that invest in the latest VLF technology is astounding, despite the upfront cost. Major technology innovations can deliver benefits to converters due to their impact on three areas:
- Faster makereadies
Digital integration has a significant impact on makeready time. The latest VLF technologies recognize factors such as paper weight and size and are designed to automatically adjust air settings from feeder to delivery based on this information. They can store specific job functions for repeat jobs and automatically adjust dryer settings. For color and register adjustments, new in-line measurement systems use photospectrometry to read the color bar and even handle spot colors. Once jobs are complete, new technology allows for simultaneous wash-up procedures for blanket cylinders, impression cylinders, and inking units — resulting in major time savings.
- Higher and more reliable productivity on a broader range of substrates
Benefits from new technologies can be seen when the press is running. Air settings are available that are speed compensated and even can be dynamic, meaning air is adjusted based on the distance from paper to sheet guide plate. Wash-up cloths can be changed during production for improved uptime. Then there is quality control of the printed sheet at full press speed. New camera systems can detect even the smallest print defects and mark defective sheets for later analysis. All of these features add up to greater productivity.
- Improved ease of use
Many older VLF presses are being operated via a keyboard where the operator has to jump from function to function. In the latest systems, touchscreens and process-oriented software eliminate this process. New software can determine the setup of the next job based on presets from the previous job and create an optimized makeready sequence, delivering greater consistency from job to job, shift to shift, and plant to plant.
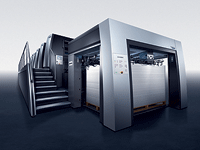
What do all of these technology advances ultimately mean for package printers? The answers can be found in the bottom line. New technologies have the potential to shorten a six-color makeready (including wash-up) on a VLF press to less than 30 min. For an average shop, 1 min of makeready time saved can mean an annual savings of $25,000; 15 min saved on each makeready can mean annual savings of up to $400,000. When you consider the combination of benefits from all new innovations, there's a savings potential equating to several million dollars over the life of the press.
Workflow also plays a major role in optimizing the process. Today's VLF presses are fully JDF/JMF-enabled and allow for an immediate analysis of every shift. This is what packaging manufacturers need to identify bottlenecks and other problem areas and to keep shops running at optimal speed.
To realize the full potential for savings and productivity in package printing, converters must remember that changes in the pressroom mean changes on the finishing side. Companies should evaluate their postpress equipment to ensure they have the ability to keep up with larger platform sizes (upgrading the width by a little over an inch can allow up to 10% more images/impressions on the sheet) and increased productivity. Replacing even four- to six-year old equipment with the latest VLF innovations can increase productivity by more than 20%. JDF-enabled automated cutters, die-cutters, and folder/gluers make the most of increased volume associated with VLF presses for both operator efficiency and maximum uptime.
Jörg Dähnhardt is director of sheetfed product management, Very Large Format, for Heidelberg USA. An engineering graduate of the Technische Universität Hamburg-Harburg, Dähnhardt earned his master's degree at the Instituto de Empresa, Madrid, Spain, and the Pontifícia Universidad Católica de Chile, Santiago de Chile. Contact him at 770-794-6196; joerg.daehnhardt@heidelberg.com.