Roller Coverings: Built 'TPU' Tough
- Published: October 01, 2009, By By Nsenga Thompson, Associate Editor
With plant operations running 24/7, 365 days a year, PPC Industries requires rollers that not only are safe and cost efficient but durable enough to endure the long run times this busy operation demands. The privately owned converter of films, bags, and tubing, with facilities in the US and Costa Rica, has more than 30 blown film extrusion lines and a Class 100,000 clean room for medical tubing production.
PPC's engineering, production, and maintenance teams decided to investigate thermoset polyurethane (TPU) plastic-coated rollers to see how much additional longevity they could provide. They turned to Menges Roller Co. for the replacements.
The TPU Advantage
TPU plastic is designed to provide the toughness and abrasion-resistance needed by most applications while also allowing the latitude to make the coating as hard or soft as the application requires.
Some of the properties available by various TPU formulations include superior abrasion resistance, chemical resistance, cut resistance, impact resistance, high tear strength, flexibility, and a broad temperature operating range.
“The whole idea behind this [change] was to get more life out of the rollers because they are expensive to replace, and changeover requires a very big effort,” says Tom Gussarson, PPC purchasing manager. “So, we're hoping to get two to three times the service life out of these TPU-coated rollers as we do from a standard rubber roller, which is about a year.”
Initially PPC installed Menges's Tiger Max TPU-coated nip rollers on one of its blown film systems. Since then, the bag machine nip roller and winder nip rollers also have been replaced with Menges's Tiger Max TPU models.
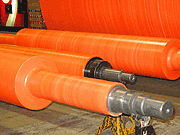
“We produce several different plastic bags with writing on them,” says Gussarson. “These bags are used for medical and food customers who require that messages be printed on the film. Any time you have printing on bags, that film must be treated through a corona system. The corona treatment causes added ozone, some of which lingers in the plant, especially in the area of the top nip roller, which is 60 feet in the air.”
Gussarson also comments that the ozone exposure will deteriorate standard plastic- or rubber-coated rollers, causing them to dry out and become brittle and crack. This condition normally would accelerate the need for roller replacement.
“The TPU rollers hold up much better when exposed to ozone,” Gussarson says. “In fact, they are almost immune to the problem.”
Safety First
In addition to productivity, another major goal in adopting the TPU-coated rollers was avoiding replacement of large, heavy rollers that are sometimes at considerable heights and can increase safety hazards for operators. For example, the rollers on PPC's top nip section are 60 ft up, 5-10 ft wide, and can weigh between 4,000 and 6,000 lb.
“That size makes the effort to change the rollers a major one,” says Gussarson. “Plus, there is also a safety consideration. While we are very safety conscious, avoiding accidents requires reducing the exposure to incidents, so if we can reduce the frequency of changing those rollers, that is also a significant benefit.”
With proven durability, cost efficiency, and increased safety for its operators, the investment of TPU-coated roller covers appears to be a permanent addition to PPC production plants.
Converter Info
PPC Industries Inc. | 10101 78th Ave., Pleasant Prairie, WI 53158 | 262-947-0900 | www.ppcind.com
Supplier Info
Menges Roller Co. | www.mengesroller.com
Circle 307 or visit www.freeproductinfo.net/pff