Web Exclusive: Flat Die Technologies Emerge as Keys to Innovation in Solar Electric Systems
- Published: May 14, 2009, By By Mark D. Miller, Extrusion Dies Industries LLC www.extrusiondies.com
Flat die extrusion and coating systems already play a role in the manufacture of solar energy components. Now they promise to be essential for the development of next-generation products enabling solar-generated electricity to be cost-competitive with energy from fossil fuel-burning power plants.
Much of the world has viewed solar and other alternatives to fossil fuels as desirable but costly and ultimately not widely applicable. This view is fast disappearing. The global surge in demand for crude oil, the intensifying debate about possible "peak oil," the national security concerns of nations that rely heavily on oil imports--these forces have increased the urgency for developing solar power and improved its economics relative to fossil fuels. At the same time, technological innovation has driven down the real cost of solar power--a trend that continues.
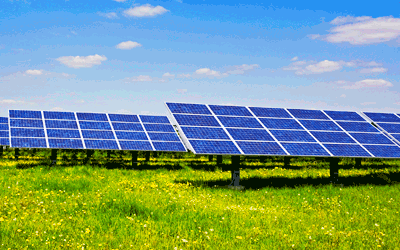
Flat die systems are in commercial use for components in traditional rigid solar panels (see Figure 1) and promise to help make possible flexible photovoltaic structures that would reduce the cost and simplify the installation of solar modules on rooftops everywhere. These will be complex, multilayer products whose manufacture will call for high-precision systems for both film extrusion and web coating.
Development of such flexible or thin-film solar systems represents an extension of technologies already in use for other applications that, like solar energy, require thin-gauge, optically clear, close-tolerance films and coatings with critical functionalities. One example is optical films and coatings for use in applications like flat panels displays. Another is flexible batteries--particularly relevant, since solar cells are a kind of battery.
In a project funded by the US government (http://pffc-online.com/news/paper_edi_awarded_us/index.html), for example, a process has been developed to produce lower-cost electrolyte and cathode films for batteries that power portable electronic devices used by soldiers. The technology has led to production of very thin films for high-energy rechargeable and primary disposable batteries. Potential nonmilitary applications include cell phones, notebook computers, and batteries for hybrid electric vehicles.
Roles for Plastics and Coatings in Solar Systems
The photovoltaic (PV) cell that is the functional heart of a solar electrical system consists of two thin layers of semiconductor materials, typically silicon-based. One is boron-"doped" so that it functions as the positive layer, and the other is phosphorus-doped to make it the negative layer. When photons strike these materials, they dislodge electrons, and because the layers are connected to a circuit, an electrical current results.
In conventional solar electrical systems, a single cell is usually quite small and produces only a few watts of power, so multiple cells are connected in series to form modules. The solar panels seen on rooftops typically consist of one or more of these modules. In turn, a large number of modules can be connected in arrays that generate many kilowatts for multiple users (see Figure 1).
Conventional solar modules are rigid flat-plate panels with several layers enclosed within a rectangular frame:
- The top or sunward layer, often called a front or cover sheet, can be made of glass or plastic;
- Inner layers consist of solar cells, typically protected by a plastic encapsulant, and a conductive grid or metal foil layer that closes the electrical circuit; and
- a glass or plastic back sheet that provides support or protection from the elements. Since there is always some space between the PV cells in a module that allows light to fall directly onto the back sheet, a reflective coating on this sheet is useful for reflecting photons back to the cells.
Slot die coating systems have been supplied that apply ultraviolet (UV) blockers, protective hard coats, antireflective substances, and other functional materials to the polycarbonate, ethylene vinyl acetate (EVA), or aluminum foil layers in these PV modules. For example, because the silicon layers inside are highly reflective, the underside of the cover sheet typically is coated with an antireflective material to reduce photon losses. Several solar manufacturers have used slot die systems that apply such coatings to glass or polycarbonate cover sheets.
Page 2 of 3
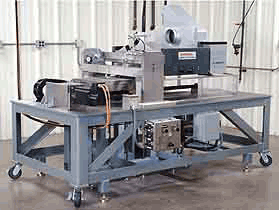
This use of slot dies is called "patch coating." (See Figure 2.) In this type of coating, materials are applied intermittently, at controlled intervals along a continuous web or onto discrete sheets or panels. In an automated process, special valves start and stop coating application; this action is coordinated with movement of the die toward and away from the substrate to promote a clean break in the coating and prevent formation of edge beads. Like other slot die systems, patch coaters are closed systems that apply coating materials in amounts pre-determined by the action of a pump that meters material into the coating head.
Few solar manufacturers have been aware of slot die coating and its advantages over other coating methods, such as spray, roll, and spin coating. In comparison with these systems, slot dies provide greater control over coating weight and distribution because they are closed systems into which coating material is pumped at closely pre-determined rates; in turn this greater control makes possible thinner coatings. Since material in the conventional systems is exposed to the atmosphere prior to being applied, slot dies also present less risk of contamination and reduce emissions into the workplace.
Tomorrow's Solar Systems: Continuous Thin Film
As an offshoot of the semiconductor industry, the solar electric industry until now has had little contact with the roll-to-roll, continuous-web production methods familiar to flat die builders and their customers. The ultimate reason for this is the batch process used to fabricate the PV material in most of today's solar applications: crystalline silicon semiconductor. It literally must be sliced into wafers, which are then paired to form cells. The discrete rigid panels that are today's most recognized solar electrical devices reflect the need to interconnect many discrete cells to form a module.
Increasingly the solar energy industry is looking to continuous thin-film technology as the key to bringing down the manufacturing costs of electric systems. What makes such roll-to-roll production possible is the replacement of rigid crystalline silicon with amorphous silicon supplied in a high-solids slurry that can be deposited onto a substrate by means of web-converting processes such as slot die coating. Though lower in PV efficiency than crystalline silicon, the amorphous semiconductor material is less costly, and this, combined with the automation made possible by roll-to-roll production, can bring down the cost of solar electricity generation. At the same time, the more extensive installations made possible by the thin film form helps offset the losses in PV efficiency.
One of the ultimate goals of thin-film solar technology, for example, is to produce PV film in large quantities of rollstock that can be sold to general contractors for installation atop houses and commercial buildings.
PV systems like these are a logical next step, as techniques already have been refined to apply conductive slurries onto a range of substrates in high-specification applications, including flexible batteries. For example, patch-coating techniques have been developed for simultaneously applying anode and cathode slurries to both sides of films or metal foils for lithium ion batteries. And for continuous-web products like thin film solar systems, "lane coating" methods have been developed to apply conductive and semiconductive materials.
While patch coating involves uncoated intervals in the transverse direction, lane coating leaves continuous uncoated lanes in the machine direction, alternating with coated lanes. Using two dies, systems have been developed for simultaneously coating two sides of a substrate with up to 48 separate lanes, each 20 mm wide and separate from other lanes by 10 mm gaps. The coating fluid has been applied in register on both sides--a critical requirement for preventing short circuits.
A typical thin film solar system would include polymer films, foil substrates, and up to six active coatings, each of which would require curing and thus could not be applied simultaneously with any of the others. One possible structure, from sun-facing side to back side, might look like this: polyethylene terephthalate (PET) film with UV-block coating; EVA protective layers; PET barrier film; a multi-component PV sandwich; a spacer film; a reflective film; an aluminum foil layer; and an EVA back layer. The PV sandwich would include amorphous silicon semiconductor, electrode, and other layers, including special coatings.
Page 3 of 3
Flat Dies Provide Many Solutions to Solar Industry
The solar-energy potential for film, sheet, and coatings that can be produced or applied with flat dies is remarkably diverse. To get a sense of the sheer breadth of possibilities, consider the range of materials offered by companies that have entire programs dedicated to photovoltaic applications. One supplier, for example, offers multiple front sheet materials, encapsulants, metallization pastes, substrates, structural materials, and back sheet films for both thin film and crystalline-silicon types of solar system. Other plastics raw material suppliers also have programs focused on the solar industry.
Flat die systems are available for processing virtually all of these material types:
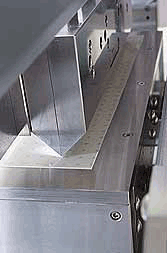
* Fixed-lip slot dies are well suited for patch coating and lane coating, in addition to continuous coating, because material is pre-metered and then applied by being drawn down in thickness as it passes from the die exit to the substrate. Some fixed-lip slot dies, for example, can offer optically clear coatings as thin as 1 micron, and edges at the 'start' and 'stop' positions are clean and well defined. (See Figure 3).
* Adjustable-lip slot dies have a flexible lip that is the key to controlling the lip gap profile and thus the coat weight. This is an important advantage in applying slurries such as those used for coating flexible battery or photovoltaic components, since slurry viscosity changes over the course of a production run and the die needs to be adjusted accordingly. An adjustable-lip slot die can be controlled manually or by means of a gauge profiler. In this case, the die lip is used to "wipe" the coating fluid onto the substrate. The minimum wet-coating thickness achieved is typically 10¨C12 microns.
*'Constant-deflection' dies for cast film are particularly valuable for critical optical and electrical applications because they eliminate the transverse cross-sectional distortion called "clamshelling," often encountered with conventional dies, and yield a uniform layer structure in coextrusion. The cause of both clamshelling and interlayer distortions is the deflection of the die bodies (the upper and lower halves of the die) caused by the very high pressure from molten polymer in the flow channel between the bodies. By reducing or eliminating this deflection, the die makes it possible for precise fine-tuning of film gauge to be carried out quickly at the die lips through use of manual or automated gauge profilers. Unlike previous ¡°constant deflection¡± dies, a new type achieves this dimensional control without sacrificing flow streamlining and throughput.
In an era when sourcing of fossil fuels has become a security issue and finding alternate energy sources is seen as a key to combating climate change, solar-generated electricity is one of the most promising alternative energy sources. The innovations necessary to reap its full benefits will generate new companies and new jobs. Flat die technology provides a range of resources to help innovators make their solar-energy visions a reality.
Mark D. Miller is manager of the New Development Group at Extrusion Dies Industries LLC (EDI). He joined EDI in 2006 as project and manufacturing engineer. Previously he spent nine years with 3M Co., where his responsibilities included R&D on applications involving slot and extrusion coating dies. Miller holds a Master's degree in polymer science and engineering from Lehigh Univ. and a Bachelor's degree in chemical engineering from the Univ. of Wisconsin. Contact him at 715-726-1201.
Supplier Info:
Extrusion Dies Industries LLC | www.extrusiondies.com
Reduce & Reuse | http://pffc-online.com/coat_lam/extrusioncoating/reduce_reuse_1208/
EDI's New Tech Center | http://pffc-online.com/news/edi_tech_center_0205/index.html
Extrusion Dies | http://pffc-online.com/mag/paper_extrusion_dies/index.html
Die Hard Innovation | http://pffc-online.com/mag/paper_die_hard_innovation/index.html
Dual-Deckle System for Trouble-Free Web Width Variation | http://pffc-online.com/the_place/paper_dualdeckle_system_troublefree/index.html
Extrusion Coating Evolves | http://pffc-online.com/mag/extrusion_coating_evolves_0905/index.html