Blown Film | Which Applications Are Most Suited for 7/9/11 Layers? Part 2
- Published: June 06, 2017, By Tom Bezigian
In Part 2 of this three-part series, polymer processing expert Tom Bezigian explains the advantages of one- and three-layer lines.
What are the uses and advantages one- and three-layer lines? To be sure, one, three- and five-layer films are not going to disappear anytime soon. The installed base of these machines is very large, and the adhesive laminators that they feed is likewise so large that it is difficult to imagine these lines disappearing.
In addition, one- and three-layer lines are perfectly suitable for commodity, non-barrier products such as institutional liners, T-shirt bags, garment bags, stretch films, construction film, and agricultural films. They also require less capital outlay, less floor space and ancillary equipment (such as material handling) are easier to operate, and the overall cost of the equipment is less than five, seven, nine, or 11-layer lines.
In those applications requiring some degree of barrier properties, especially those that are adhesively laminated to metallized films, five-layer structures as shown in Figure 1 are more than adequate for many applications.
Figure 1. Typical Five-Layer Coextruded Structures
Three-layer film blown lines are capable of either a two-layer or three-layer structure in the form of an A/B/A or A/A/B structure by simply using the same material in two extruders. These structures are commonly used as frozen meat and fish packaging films, frozen vegetable bags, cereal liners, forming webs, modified atmosphere packaging (MAP) for fresh cut produce and poultry, boil-in bags, and much more [3].
Three-layer film capability also provides the option to "bury," or sandwich in between, a low-cost material or post-industrial waste in the middle layer to reduce cost, or to bury a pigmented layer between two layers of virgin polymer to reduce cost, increase gloss, or meet regulatory requirements.
It has long been recognized that three-layer films have limits, such as with oxygen barrier or print quality. To solve this issue, many three-layer films were used as part of an adhesive lamination to reverse-printed films to achieve higher quality structures, either to other three-layer films or to metallized-oriented films and foil for improved barrier properties.
Conventional wisdom would say that if three layers are good, five layers must be better. Though this is not necessarily true, it can be said that five layers can offer more options and flexibility over three layers. Figure 1 shows a typical five-layer film structure, showing a core layer of ethylene vinyl alcohol (EVOH) as a barrier layer, inner and outer layers of linear low-density polyethylene (LLDPE), and "tie" or adhesive layers to join together the otherwise incompatible LLDPE and EVOH. This structure is ubiquitous today and is used in many applications.
For the many basic package structures, a five-layer film obviates the need for an adhesive lamination step. Figure 2 shows a typical five-layer coextrusion blown film line. Some might argue that the modulus of oriented polypropylene (PP)and polyethylene terephthalate (PET) films are greater than unoriented nylon films, and that laminations are superior to unoriented blown films, and that the film structure shown in Figure 1B above is inadequate for many packaging applications.
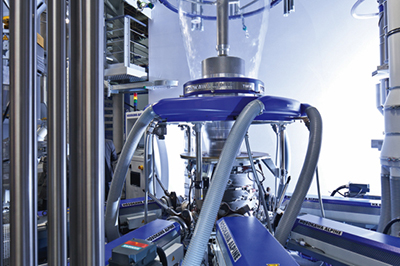
However, careful examination of data [6] shows that the secant modulus of nylon is greater than polypropylene and about 10% less than PET. This difference is easily replaced by the traditionally thicker nylon abuse layer, and in practice, nylon-based packages exhibit good toughness and stiffness.
In Part 3 of this series, we'll cover the benefits of 7/9/11 layer lines.
Bibliography
1. US Patent 2820249
2. US Patent 3308508
3. "Blown Film Training", The Dow Chemical Co.
4. "Rethinking Technology Innovations for High Barrier Applications", Kurt Freye, Reifenhäuser Kiefel Extrusion
5. "Properties, Processing and Handling of EVALTM EVOH Resins", Medlock, G., AIMCAL Fall Technical Conference, October 2014
6. "The Influence of Sealant Modulus on the Bending Stiffness of Multilayer Films", Morris & VanSant, DuPont Packaging White Paper, 2009
7. "Coextrusion - The Pros and Cons of More Layers", Bill Hellmuth, Gloucester Engineering
8. "Nano-layer - Micro-layer Structural Advances in Shrink Films, Schirmer et al, 2013 SPE International Polyolefins Conference, Houston, Texas, USA
9. http://plasticsengineeringblog.com/2013/01/04/new-technologies-in-stretching-and-touching/
10. US Patent number 8870561, issued 28 OCT 2014
11. From: Medlock, G. (Kuraray), “Properties, Processing and Handling of EVALTM EVOH Resins”, AIMCAL, Oct 2014
Tom Bezigian holds a B.S. in Plastics Engineering from the University of Massachusetts–Lowell. He has been affiliated with the converting industry for more than 30 years and writes a blog, Tom's Poly Ploys, for PFFC. It focuses on the field of polymers, laminations, and coatings with emphasis on R&D, quality assurance, manufacturing, marketing, operations, finance, and expert witness experience in the blown film, cast film, orienting, extrusion coating, and converting industries. He is owner of PLC Technologies consultancy with over 30 years experience. Contact him at This email address is being protected from spambots. You need JavaScript enabled to view it..