Nu-Coat chooses Vetaphone Corona for pioneering UV coating line
- Published: November 09, 2020
Tucked away in a quiet industrial estate in Cwmcarn, near Caerphilly in South Wales, is a small but fast-growing company that has set about revolutionising the sign and wide format markets with UV polyacrylate adhesives. Already widely used in industry sectors from medical to food, automotive, and labels, the creation of a dedicated coating line by
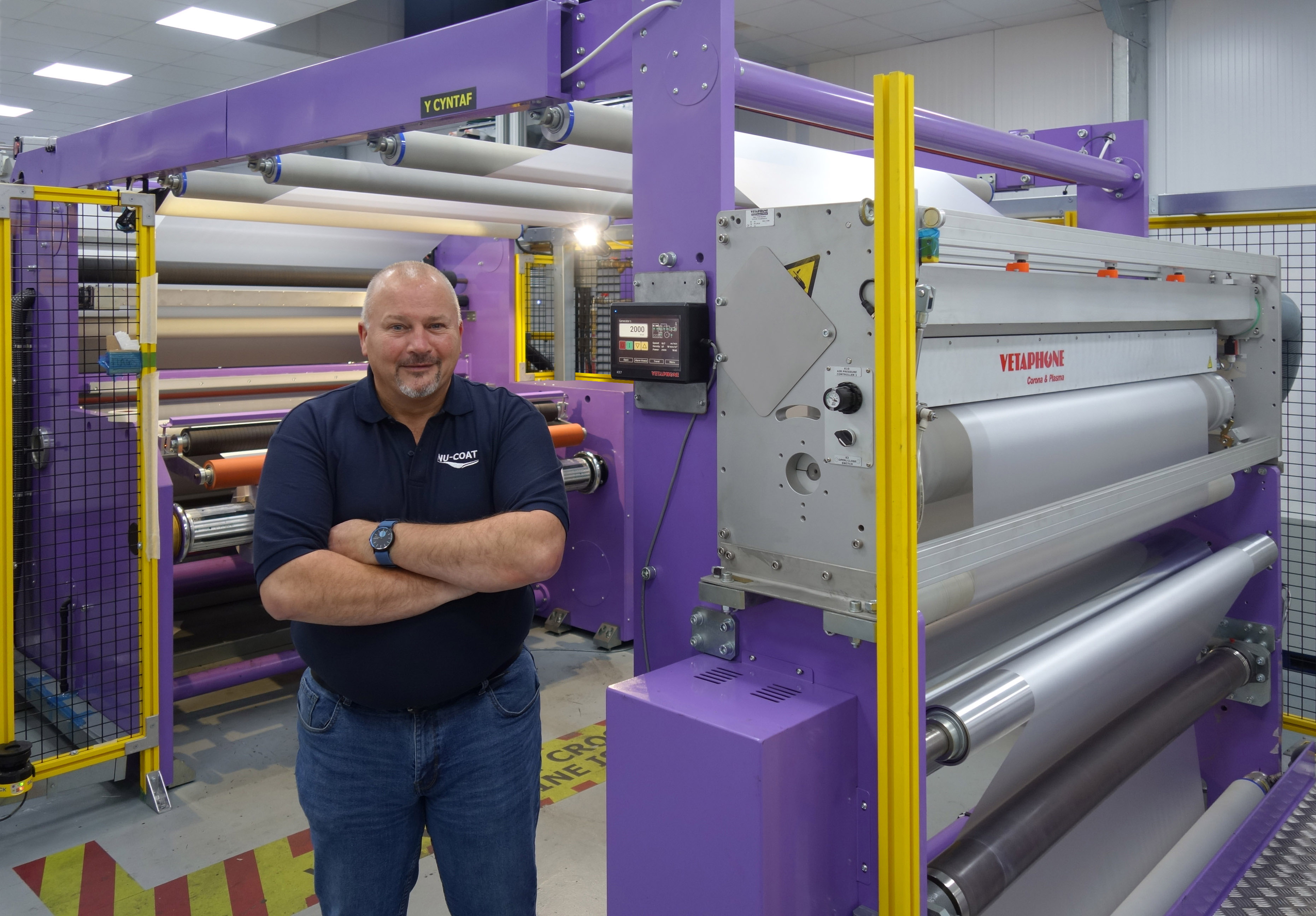
Nu-Coat that uses solvent-free, non-aqueous adhesives cured by UV-C light brings the exceptional qualities of this technology to a broader field of applications.
Established in 2018, Nu-Coat’s business has been three years in the making at the hands of its two Directors, Chris Martin and Rob Musto, who saw the benefits of creating a flexible and agile production facility that could respond quickly to changes in market demand and also handle short run jobs profitably. “We have developed an extensive range of adhesives specifically for the requirements of our industry. They can be coated onto a wide range of films such as PVC-based, PET, and other non-PVC films,” explained Musto.
Production is carried out on a compact 1.7m wide coating line capable of speeds up to 100m/min depending on the coating level required for each job, with converting handled by two slitter rewinders. Work can be supplied in standard or custom size rolls in runs as short as 1000 linear metres, which is where Martin sees niche market opportunities. “We are adept at developing new and bespoke products that we test thoroughly before putting into commercial production. Our flexibility allows us to respond easily to rapid campaign changes, and our compact line is ideal for fast turnarounds.” Currently, working a single shift, output stands at around 30% of the capacity of the 64,000 sq/ft plant which employs a team of 9 experts, according to Martin.
When researching the market for the best equipment to fulfil its production criteria, Nu-Coat turned to Vetaphone for surface treatment advice and assistance. Kevin McKell, VP of Technical Sales at the Danish manufacturer was instrumental in this and takes up the story: “As the inventors of Corona treatment we have a vast knowledge base that we like to share with existing and potential customers, so when Nu-Coat approached us we were keen to be involved in what is an exciting new venture in this field. We advised on the best technology for their pilot line, and subsequently supplied and installed one of our 4kw VE1C-C 1920mm Corona units on the coating line when it went into commercial production.”
One of the key advantages of Vetaphone Corona systems is the precision control they offer. Far from a ‘set and forget’ technology, the sophisticated iCorona generators provide a degree of adjustment to the treatment level that is not available elsewhere. With Nu-Coat looking to push its own pioneering technology into new markets, it was vital that all pre-coating operations could be guaranteed for accuracy and reliability. “I chose Vetaphone because of my previous experience with the company and the fact that they are acknowledged as the market leader in surface treatment. Not surprisingly, we’ve had no issues with their Corona system, and this gives us peace of mind as well as production efficiency,” explained Musto, who added that the ease with which Vetaphone technology can be upgraded to meet the challenges of constantly changing market demands was another deciding factor.
As the Covid-19 pandemic shows no signs of relinquishing its grip on public health and business, Martin explained his company’s position: “With the hospitality and events sectors badly hit, which are traditionally good markets for us, we were initially concerned, but the rapid increase and ongoing demand for floor graphics and face visors has in fact opened new areas of opportunity for us, especially with our flexible capability. Our expertise in graphics with the necessary slip rating approvals and the creation of a new wipe-clean laminate for shop counters and door plates has kept us really busy.”
Conscious that the ‘green lobby’ see PVC as an undesirable, he points out that Nu-Coat does all it can to mitigate the substrate’s effect on the environment in a world where plastics and oil-based products are essential. The company’s process involves no dilution, no solvents, no drying ovens, no post-production handling of chemicals, and no VOCs. “Our coater requires up to 65% less power than a conventional line and has a smaller footprint that allows us to use space more efficiently. Even the PVC we use is 25% thinner than is customary, with no compromise in its performance. And, we recycle everything we can!”
At a time when environmentalists believe the world is at a tipping point with regard to pollution, it’s companies like Nu-Coat with innovative ideas and solutions that will make the difference. “This is the reason that Vetaphone is so actively engaged with both OEMs and production plants in a drive to redress the potentially harmful impact of plastic material,” stated McKell, adding: “the closer we work together as a cooperative partnership and share our expertise on a transparent basis, the better it is for all parties.”