Taming Plastics
- Published: February 28, 2005, By Greg Zimmer, Zimmer Industries
Converting Plastics
Remember the classic scene from the movie "The Graduate," when the new graduate’s uncle provides some career advice by simply whispering in his nephew’s ear, "Plastics!"?
That very well may have been good advice at the time, but through the years, no materials have caused more absolute nightmares for converters around the world than the wild, wacky family of products we lovingly/hatingly call "plastics."
Plastics may be flexible, brittle, or stretchable; thin, medium, or thick; clear to opaque; really easy to tear, easy to tear, tough to tear, or impossible to tear; have excellent "memory" or have no "memory"; react readily to heat or not react to heat at all; allow air to pass through them or actually prevent bullets from passing through them. You get the picture.
So how do you cut, crease, and perforate such incredibly diverse (and perverse) materials?
Options for Cutting
Cutting plastics with steel rules often may require an extremely sharp, sleek cutting edge.
For cutting plastics in "conventional" platen die-cutting, a ground edge usually is recommended over the more popular shaved or skived edge. Not only is the ground edge sharper, its machine lines (grinding lines) run in the exact same direction as the cutting process.
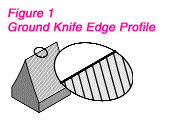
The machine lines of a skived edge run in the exact opposite direction of the cutting action. This can cause problems when cutting plastics. A sleek, ground edge often may reduce cutting pressures and produce cleaner, smoother product edges (see Figure 1).
A pre-nicked cutting rule is another option for cutting and/or nicking various plastics. This rule is very sleek in its primary bevel (a 21-deg centerface) and secondary bevel (a 2-deg double bevel) and comes in various nicking patterns; the most common is 4-microscopic nicks (0.007 in. or 0.18 mm wide)/in. The double bevel is helpful when cutting thicker plastics.
This type of rule produces edges that are as close to "clean" and smooth as possible and also is available with 1 or 2 nicks/in. (see Figures 2A and 2B).
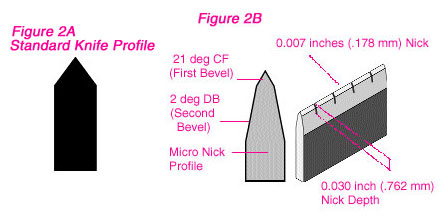
Another effective method for cutting plastics (especially plastic films) uses a specialized serrated rule, again with a sleek, very sharp edge.
Cutting in this manner requires very sharp points and gullets (the valleys between the teeth). The points of the teeth need to be super sharp, or else the blade may tend to stretch or distort the material before the actual cutting begins.
If the gullets are very sharp, this helps create an easy, continual cutting action that allows the points of the teeth to pass through the film totally, thus completing the cut.
When the gullets are not sharp, the cutting action may be hesitant and can stall or "bog" down in the gullets. This also may cause the plastic to stretch and/or distort.
This type of rule usually comes in either a 12- or 16-tooth/in. (TPI) pattern.
This method of cutting requires the serrated teeth to pass through the plastic completely, usually into "air," or a slot (preferably supported) or a dense brush, because the teeth, being so sharp, may be somewhat "fragile" (see Figure 3).
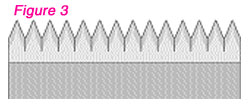
Options for Perfing
There are two ways to use a serrated blade to create a perforation. One way is to control the penetration of the blade, so only part of the tooth is allowed to pass through the plastic (see Figure 4). This creates a perforation of variable strength.
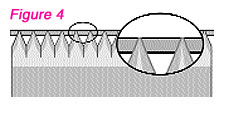
Obviously, the deeper (closer to full penetration) the teeth go into the material, the weaker the perforation.
The second way to use this type of blade to perforate is to create many slots of desired widths in the cutting edge (see Figure 5). The slots produce an uncut area in the material, even if the entire tooth is allowed to pass through the plastic. Increasing or decreasing the size and/or number of slots in the blade allows variations of perforation strengths. Both methods also require the blade to penetrate into air or a brush.
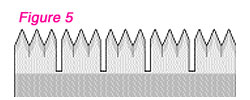
In platen die-cutting, a desirable alternative to conventional perf rules is a microperforating rule. These rules perforate various plastics effectively because they have the seemingly contradictory abilities to create perforations having anywhere from 10% to 70% hold strength, yet they (all) tear very easily and produce product edges that look and feel vastly superior to edges produced by conventional rules.
For example, one pattern is 50 TPI with a 0.007-in. (0.18 mm) tie (or space) between the teeth. This pattern creates a 35% hold or burst strength (35% of the material is left uncut), yet tears very easily because each uncut area being torn is only 0.007 in. (0.18 mm) wide (see Figure 6).
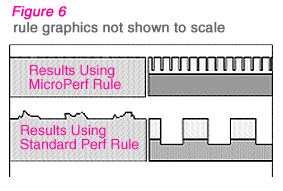
Invisible microperfs are made with a V-shaped tooth, are available in tooth patterns from 30–120 TPI, may be made with ties as small as 0.002 in. (0.05 mm), come in either coil form or lengths, and are an economical alternative microperf, often ideal for thinner gauge plastics.
The finer (more teeth) the tooth pattern is, the thinner the sheet that can be perforated and vice versa.
Creasing and Scoring
The last element of converting plastic is creasing or scoring. Historically, a great deal of scoring of plastic has been done using radio frequency (RF). This is an effective, yet costly process.
Other methods of scoring or creasing plastics often employ heat in various manners. Again, this is somewhat effective, yet costly.
For more than 15 years, microperfs have been used successfully to "cold" crease plastic with tooth patterns normally ranging from 30–70 TPI. Cold creasing with microperfs may be achieved by expertly controlling the depth of penetration of the perf into the plastic (see Figure 7).
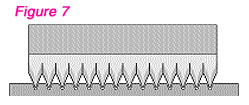
One way this can be accomplished is by reducing the height of the perf rule in a die [for example, using a 0.930–0.934 in. (23.6–23.7 mm) height microperf in a die with a 0.937-in. (23.8-mm) cutting rule].
Originally, this process tended to create creased product edges that were judged to not be "smooth enough" to the eye or to the touch. With the advent of 100- and/or 120-TPI "invisible" perfs, very "smooth" edges now are possible.
By making sure the rule doesn’t fully penetrate through the plastic and by effectively employing the different gullet depths to create the required levels of "strength," it is now possible to produce an effective, consistent, smooth, economical, cold crease.
Another possible method of scoring plastics calls for the use of a new creasing rule. This rule actually waves or "corrugates" the face of a conventional crease rule (see Figure 8).
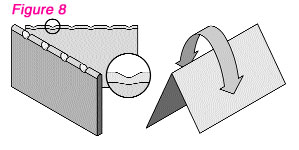
The application of this type of crease creates a somewhat similar effect to that achieved by the use of microperfs and also eventually may be aided by varying gullet depths and the possible addition of heat to the converting process. This process is less costly than microperfing.
So, to all those plastics we love and hate, I say, "Look out, we are coming to tame you, armed with products that will finally get you to behave (convert) exactly the way you should!"
SUPPLIER INFO:
Zimmer Industries—zimmerindustriesinc.com
Greg Zimmer is CEO of Zimmer Industries, Hawthorne, NJ, a 125-year-old, family-owned steel rule manufacturer. He is a graduate of Rochester Inst. of Technology, Rochester, NY. Zimmer is a 37-year veteran of the converting industry and holds three US patents. He can be reached at solution@zimmerind.com" or by phone at 973/427-8000.
The views and opinions expressed in Technical Reports are those of the author(s), not those of the editors of PFFC. Please address comments to author(s).