Flexo Printing | Evolution of the Chambered Doctor Blade System
- Published: February 26, 2016, By Wallace Nard
New chamber technology will propel the printing industry to the next level of quality and savings.
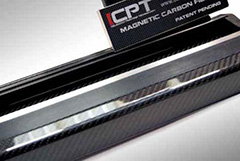
Chambered doctor blades are now a standard on all central impression (CI) flexographic presses and high definition (HD) corrugated post printers. High definition flexo corrugated post printers have evolved from the rubber fountain roll to 100% reverse angle chamber systems, as have flexo CI presses for the flexible packaging industry. The reason for this has been higher print quality.
On press automatic wash up systems are also standard on flexo CI presses and now are following suit on corrugated post printers. The next big feature coming is how to improve the performance of the chamber and reduce ink and cleaning solution waste. On average, 50% of ink purchased is not applied to the board or film. This can be a large financial burden on printers.
Environmental regulations will continue to get stricter, calling for better ways to reduce the cost to deal with this waste stream. A large proportion of this ink is in waste cleaning solution, and in order to dispose of this, the majority of plants have ink cleaning (or flocculation) plants. The average cost can run up to $100,000 annually depending on the total print volume. The costs for the chemicals to clean the ink are also expensive. Then you have the residual waste, which goes to landfill.
It is clear that these additional costs not only reduce the profit of a plant significantly, but also lead to higher maintenance of all of the equipment.
What is the industry looking for in Chamber Technology?
There are some key points that will help propel the printing industry to the next level of quality and cost savings, which include the following:
- High flow rate of ink and coating to significantly reduce micro bubble formation in order to fill the anliox cells with less aeration of ink or coating.
- Ink level inside chamber must be controlled in order to reduce air entrapment in the ink, while at the same time not over-pressurize the chamber, which can cause leakage.
- Small chamber cross section to reduced end-sealing area to minimize leakage. End seal leakage of the chamber is the number one problem associated with chambers.
- Back doctoring of the containment blade, in which the containment blade scrapes off the residual ink on the anilox roll as it re-enters the chamber.
- Ink saving due to the reduced volume of the chamber and the special treatment of the carbon fiber surface with an antistatic resin, allowing a savings of a high percentage of the ink placed in the printing circuit.
- On-press cleaning with no contamination during color changes.
- Reduced production downtime through faster on-press cleaning.
- Faster press speeds with less chamber bounce.
Historically, the standard ink chamber system has been made from aluminum, mainly due to its light weight and lower cost. However, due to maintenance and corrosion problems over time, the industry is now looking at carbon fiber chambers as the cost continues to come down. Anti-corrosion carbon fiber is not subject to any type of corrosion caused by water-based inks, solvents, and glues. It offers the best resistance against corrosion long term.
Main Advantages of Woven Carbon Fiber Chambers
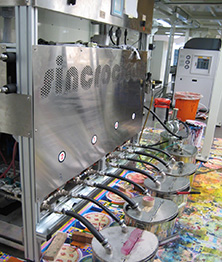
Carbon fiber is 300% stronger than aluminum, and it does not expand with heat. It offers the best contact adherence to the anilox roll and reduces vibrations, even on wide machines. Carbon fiber is 70% lighter than aluminum, and because of the lightweight nature of the carbon fiber, press speeds can run at a higher rate.
Carbon fiber is coated with a resin with excellent antistatic properties in order to easily remove any ink trace. As a result, the cleaning of the chambered doctor blade is very quick and easy. This also leads to a considerable reduction in water or solvent consumption while washing the ink circuit. There will be a noticeable ink savings due to the reduced volume of the chamber and the special treatment of the surface with antistatic resin, which allow saving a high percentage of the ink placed in the printing circuit. Blade replacements are made more safely and quickly through magnetic coupling (patent pending).
Managing Your Pressroom Efficiencies
When companies run up against machine capacity problems, they often consider working overtime, adding shifts, or purchasing new machines at great cost. Instead, companies should consider improving the performance of existing flexo presses. By minimizing changeover times and improving operator performance, print quality is also optimized. In all this, the “devil is in the details.”
For the older central impression presses producing flexible packaging and for the corrugated market, the big push is for high definition flexo post printing, which can be realized through upgrading to carbon fiber chambers and automatic wash up systems.
About the Author
Wallace Nard is president/owner of KYMC America, Carol Stream, IL. His career in the printing and converting industry spans more than 55 years. He started his career in flexo in 1957 working for Porter and Dugas, becoming general manager in 1964. He then became VP of Reilly Lake Shore Graphics in the 1970s. He joined Anderson & Vreeland in 1973, working his way up to marketing manager. In 1989, Nard formed Novaflex, a printing and laminating sales/service group.
He was elected to the FTA Board of Directors in 1979 and again in 1982; he also served as chairman of the board of FFTA. He was chairman of the FTA Annual Forum in 1983 and has spoken at numerous gravure and flexo association meetings. He was an editor for Flexography: Principles & Practices and the holder of several patents related to the graphics industry. Nard was inducted into the FTA Hall of Fame in 1988 for his lifetime contribution to the industry.