Best of Both Worlds
- Published: August 01, 2008, By By Edward Boyle, Contributing Editor
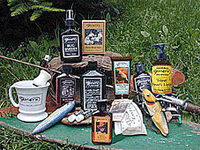
With the price tag on a standard digital press approaching $750,000 without a finishing unit, many converters consider it an investment they simply can't afford to make. However, one Westfield, MA, label converter found that it couldn't afford not to buy one — or even two!
Randy Duhaime, general manager of Dion Label Printing Inc., says that even with seven flexographic presses running two shifts at its 35,000-sq-ft facility, the company continually saw its efficiency hampered by the need to convert runs of fewer than 5,000 ft on presses designed for the long haul. Putting it mildly, he explains, “Taking three hours to set up a job that takes 20 minutes to run simply wasn't advantageous to us.”
So in April 2005, Dion installed its first HP ws4050 digital press. It prints seven colors on a wide range of substrates, including metallized papers and films, as well as pressure-sensitive and unsupported shrink-sleeve materials, at speeds to 50 fpm for four-color process work. Dion Label added a second ws4050 less than a year later, this one with a re-inserting option that allows the company to print two-sided sheets in perfect register.
Capacity Filled Up Fast
Duhaime explains the need for a second digital press quickly was apparent, since 90% of the work run on the first press had been moved over from its 10-in. and 13-in., eight-color Nilpeter and Propheteer flexographic presses — all of which perform exactly as they were designed to perform. However, with even more orders coming in as current and potential customers learned of Dion's newfound digital capabilities, he says the purchase of a second press not only was justified but required!
“We were definitely able to go after work that our existing customers had because we knew it was better suited for digital, and we promote [our capabilities] that way,” says Duhaime. “We also got new work, because when people heard that we had digital, they called us and said, ‘Do you think this would run on digital?’”
“We're adding new customers regularly,” adds graphics director Sue Hebert, “but some of our existing customers are excited about the digital environment because they feel they have more options with quicker turnaround, lower set-up costs, and no plate costs.”
Duhaime says that prior to installing the digital equipment, Dion Label met its customers' short-run needs by running multiple shifts on its high-speed flexo presses “and spending a lot on overtime just to get the work out the door. We always made that happen, but the digital press did make it easier. Some of those jobs had a lot of color changes, as well as die and plate changes, and we were only doing three jobs a day off our flexo presses, even on short runs of 10,000 to 15,000 labels. We can get nine of the exact same jobs off our digital presses.”
Digital Versus Flexo
Hebert says Dion Label never got caught up in the debate among label converters over “digital versus flexo,” preferring instead to realize the advantage of “one complementing the other.” She notes that companies offering only one of the two technologies “badmouth each other,” much the same way that converters who use “only offset or only [ultraviolet] flexo always say their way is better.”
Adding the short-run advantages of digital, says Hebert, “actually has spilled over to make our conventional environment more efficient and more productive. The conventional presses are spending more time producing labels and less time on setup. The digital presses allow Dion to continue to meet customer demands for short runs that wouldn't have been nearly as efficient if they were produced flexographically.”
Yet, Duhaime says, run length isn't the sole consideration when deciding whether jobs should be printed flexographically or digitally. The particular nuance of a digitally printed product — dead-on register — sometimes makes it beneficial to forgo speed for quality, he says. Because both technologies have different strengths and offer distinct advantages, every new job is evaluated when it comes through the door.
“Initially it was touted as a short-run press,” Duhaime says of the HP, “but we changed our thinking on that. Now, we do some long runs digitally because of the quality. And we're honest with our customers about that. Some of our customers are willing to pay a bit of a premium to keep it on the digital press for longer runs to meet their exact standards. The option is open to them.”
Hebert notes the HP digital presses rarely are used for runs of more than 10,000 ft, with one rare exception: When a customer has long runs of multiple items — and any number of those items are changed within the run. That would hardly be feasible with the cost and time necessary to create conventional flexo plates. With digital, products can be changed “on the fly.”
Says Hebert, “We could do a 20,000-foot run when there are 30 items, because in the digital environment, you can queue up a second, third, and fourth item with no new set-up charges and no new set-up time.”
Next Up: Flexo Investment
Much in the way combination presses changed the quality and efficiency of the converting industry two decades ago, Duhaime believes converters using a combination of flexo and digital presses will be best suited to meet the changing needs of the marketplace in the years to come. “I think digital is going to be an increasingly higher volume of our total business, but obviously we are not going to be giving up on flexo,” he says. “Our next large machinery investment is going to be in the flexo world.”
Adds Hebert, “Both environments are growing, and certainly each has a strong place in the labeling market. So we think we have the best of both worlds.”
Apparently, so do their customers.
Converter Info
Dion Label Printing Inc. | 539 North Rd., Westfield, MA 01085 | 413-568-3713 | www.dionlabel.com
Supplier Info
-
Hewlett-Packard Co. | www.hp.com
PFFC-ASAP 301 -
Nilpeter | www.nilpeter.com
PFFC-ASAP 302 -
Propheteer Intl. | www.propheteerintl.com
PFFC-ASAP 303
Contributing Editor Edward Boyle, based in Reading, PA, has covered the converting industry for more than 23 years. Contact him at EJB Communications; 610-670-4680; ejbcomm@aol.com.
Proof Perfect
In addition to its short-run advantages, the HP ws4050 digital press also serves as an ideal proof press, says Dion Label's graphics director, Sue Hebert, since color remains consistent from run to run and label to label. Proofs also can be coated or laminated to offer a true prototype of the finished product, “and you can't get any better than that.” She says it is particularly helpful when printing on a clear or silver substrate because it is difficult to visualize the true effect in conventional proofing formats.
This characteristic is especially important when launching new products, says Hebert. They initially may be converted as a short run on the digital press and ultimately transferred to the high-speed flexo presses, cutting costs without sacrificing quality.
“There are some items that are clearly digital jobs, because we have perfect registration in the digital world as opposed to a slight shift in the flexo world,” explains Hebert. “You can produce complex designs with very small knock-out areas in multiple colors, including hi-fi colors, that meet the needs of clients who really want a splashy label. When practical, we strive to create designs that also can be printed conventionally. As volumes grow, we can move them into the flexo environment, improving efficiency and pricing with faster press speeds.”