Ink Mileage: Measure & Manage
- Published: December 01, 2006, By By David Argent Contributing Editor
Process Management
In November we reviewed ink transfer. With this basic understanding, we can move on to actual numbers on the basis of that which can be measured can be managed. Skeptics abound who believe there are too many variables to get useful data. Others think this is an opportunity to isolate and minimize process variation and thus improve productivity and reduce waste.
Back to the process model shown in the August issue: An ink mileage concept can be developed as an input-transform-output equation. On the input side is ink of correct color and strength. It is then metered precisely (more or less) through the press. On the output side is a predictable consumption figure.
The flexographic printing process has become very repeatable due to quality and consistency improvements in anilox rollers, plates, chambered inking systems, and press controls. It has been shown in many studies that flexo ink transfer is very predictable, can be quantified, and is directly proportional to the anilox roller volume.
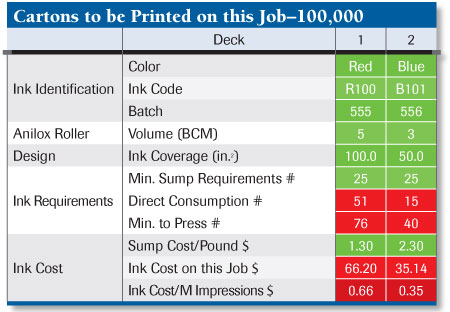
Between 25% and 30% of ink in the anilox roll is deposited on the substrate, at the low end for film and at the high end for paper and board. The wet ink film transferred to the substrate is very thin—about 2 microns from a 5 bcm anilox roller. Having established there is a predictable transfer rate, it is fairly straightforward to develop accurate ink consumption rates. There is a stepwise procedure:
- Measure the gross ink consumption on an actual press run.
- Convert the figures to 100% coverage, based on actual plate coverage.
- Convert to consumption rate: lbs/ream or g/m2.
- A spreadsheet can be designed for ink consumption for future jobs.
It is interesting that on deck 2, the ink consumed on the job is less than the amount required to ink up the deck. The overage contributes to the rework stream. But most importantly, this model allows the job to be costed realistically before going to press and before pricing. The biggest variable in this model is anilox roller care. These rolls are made with accurate, repeatable cell volumes, but loss of volume can occur without preventative cleaning maintenance.
Similar mileage models can be made for gravure and litho presses, although there may be more variables to be addressed. In gravure, the chrome wears on the cylinder during the run, reducing ink volume in the cells. This is addressed by feeding stronger ink to the press progressively. In litho, the amount of ink delivered to the substrate is influenced by ink/water balance and roller adjustments.
Once again, ink mileage modeling is an example of that which is measured can be managed.
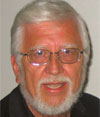
David Argent has 30+ years of experience in the converting industry. He specializes in process analysis and improvement with particular emphasis on ink and coating design and performance. Contact him at 636/391-8180; djvargent@sbcglobal.net.