Digital Printing, Part 1 | Technology
- Published: October 01, 2009
In the most recent columns, the competition between flexo and gravure printing was examined. It seems that digital printing is becoming a factor in this arena, and now it may have achieved the status of being a disruptive technology. Digital printing solutions directed at the converting market open up new opportunities for packaging printers with just-in-time printing and economic short runs.
Digital Printing Overview
There are three primary digital solutions: thermal ribbon, electro-photography, and inkjet. The future path for digital printing has become clearer now that there is experience with the various technology alternatives that have been developed. Inkjet has taken the lead, and this technology will be examined.
Inkjet is a noncontact printing method that can use several different ink platforms and thereby print a wide variety of substrates, including paper, film, and foil. There are two main classes of inkjet printing: continuous (CIJ) and drop-on-demand (DoD).
CIJ long has been used for printing low-resolution expiry dates and simple bar codes. DoD technology allows printing of full color images at line speeds of commercial interest. Printheads can be configured to function in a scanning mode in which the substrate is static during the print cycle. One row of dots is jetted while the substrate is held stationary. When this row is complete, the substrate is advanced to the next row for jetting. In this mode, the print rate is inherently slow, but it is possible to wipe and clean the printheads during production. Consumer and office desktop systems employ this setup, but slow output will limit any packaging applications.
Single-pass inkjet printing uses a group of stationary printheads to create an image on the moving print substrate, allowing competitive print output for packaging. However, this configuration places greater demands on ink stability since cleaning the printheads is more difficult.
The UV Advantage
In single-pass DoD inkjet printing, there are several ink options. These are water-base, solvent-base, and UV cure. Since UV inks remain completely open until they are cured on the substrate, they have the real advantage of fewer tendencies to clog the inkjet nozzles. There are also application advantages of gloss, product resistance, and near-zero VOCs, all of which combine to make UV ink the favored DoD ink system.
DoD Jetting Process
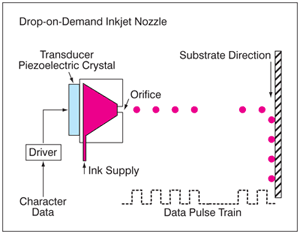
In DoD printing, an ink chamber is filled with ink. An ink droplet is ejected when an electric field is applied to the piezoelectric crystal. This results in the deformation of the crystal, which, in turn, squeezes an ink droplet from the ink chamber. The relative numbers involved in this process are quite astonishing. The jet nozzle is about 50 microns in diameter. The jetting occurs in a binary manner (on/off) driven by data input for the print design.
Each jet nozzle emits drops of ink as small as 10 pl (a picoliter is one-trillionth of a liter). The jetting rate from the nozzle is in the order of 20,000/sec. In a production application, there can be tens of thousands of nozzles. It is fascinating to note that the inkjet drop size is about the same as the amount of ink transferred from an individual anilox cell in flexo printing.
When the ink spreads on the substrate, the resulting thickness is about 8 microns. This ink film thickness is several times greater than flexo, gravure, and offset, so the applied cost of ink will be higher. However, since the same amount of pigment is being used to produce a given visual effect, the extra cost is for less expensive carrier medium. If you factor in the elimination of makeready and less waste (because registration in inkjet is perfect from startup), inkjet will be cost effective.
Next month some commercial aspects of digital ink jet printing will be explored.
Process improvement expert David Argent has 30+ years of experience in process analysis with particular emphasis on ink and coating design and performance. Contact him at 314-409-4304; djvargent@sbcglobal.net.