Rotary Screen Printing's Contribution to RFID, Part 2
- Published: January 31, 2005, By John Costenoble, Stork Prints
Part 1 | Part 2
Drying and Curing Considerations
Particular care has to be taken in the drying of the circuits. The inks are likely to lose conductivity if they are not printed according to the desired ink profile. Deposit thickness and track width tolerances are extremely tight. Generally, a printer can achieve tolerances of ±0.1 mm. Deviation from the required distance between the printed antenna tracks must be avoided as well. As already stated, if accuracy in any of these areas is not achieved, it is unlikely that the printed circuit will have the desired antenna resistance, resulting in malfunction.
Recommended drying times for RFID antennae typically range from 30–120 sec, at up to 140 deg C. A longer make-ready length of the web in the drying system can help speed up the process - though there are other variables that have to be taken into consideration. Vertical systems are ideal for slower presses. With stricter environmental regulations, one must prevent solvents from entering the atmosphere. Thus the rotary screen drying units on the RFID converting line would include a second chamber to which evaporated solvents would be channelled for condensation. Thereafter they can be used for energy recovery or even treated and reused.
Apart from printing speeds though, the quality of the ink is an important variable. Efforts are being made to improve the conductivity, so that lower ink volumes are necessary. Work has been done with a leading ink producer to print an antenna that can print at speeds up to 30 m/min.
After the drying operation, the antenna is cured at about 120 deg C for about 2 min to achieve the correct softening of the particles.
Because of the drying conditions, the choice of substrate is either paper or polyester, of thickness between 50 and 100 µm. Etching rules out paper; drying and curing rule out polyethylene and polypropylene, for the meantime at least!
Usually, curing in the above conditions halves the resistivity; lamination halves it again. The figures quoted earlier relate to the desired outcome.
All this goes to show that you just can't go out on a mission to supply RFID labels without a good understanding of how the label will be used, whether it is going to be part of a larger label, and how it will be inserted into that construction. There are so many variables in the equation that determine the end product. The best move is for all the people involved in supplying the materials and the label-making equipment to sit down together from the earliest stage.
Opportunities for Growth
The growth of the RFID market depends a lot on reducing the size of the chip - or finding an alternative solution to the chip. That's because the chip makes up such a big proportion of the label's cost.
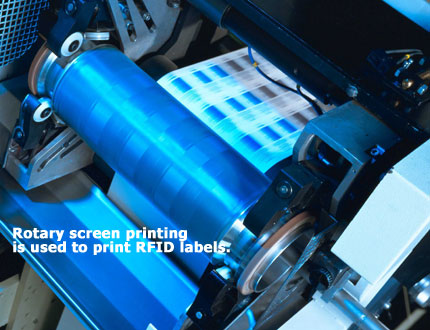
It's heartening to see research into producing and placing tiny chips, as well as into chipless tags, too. Chipless circuits will take RFID into new areas because they appear to be the cheapest to produce; therefore, this technology is the industry's best route to the $0.01 tag. By 2003, cumulated sales looked like this:
- Chip-based - 1400 million
- Chipless - 120 million
- Chip based counted for 97% of the market value
(Figures compiled by Frost and Sullivan.)
So beyond the technological advances, what else will drive the volume higher?
High-frequency applications include the National ID contactless cards. These are becoming more likely since the world is a less safe place. China expects to have completed this by 2010, which means a 970 million market size there alone.
Electronic Passports - these are becoming a requirement to enter the USA. They will be rolled out in Australia in 2004, followed by Thailand and Europe, especially Belgium, Sweden, UK, and the Netherlands. The latter country currently is doing tests with biometric passports for instance. Other opportunities include encapsulated laundry tags and public transport tickets.
The market opportunities for UHF frequency are very large since they are the choice for supply chain management applications at pallet level. Examples include the roll-out of RFID by major retailers - Metro of Germany and the world's largest retailer, Walmart. The latter has insisted the top 100 suppliers be ready to work with RFID at pallet level and have the necessary systems in place by 2005. UHF opportunities in the automotive value chain also are significant. One example is their potential for application to car tires. There are 1.25 billion in use today, and 200 million new tires are sold each year.
Research from Frost and Sullivan suggests the overall RFID market is growing at about 8% a year, and that toward 2006, the speed will accelerate toward 10%. By that time, annual production is expected to be 2.5 billion units.
Over the last year, we have heard some wonderful things about what RFID can do; imagination is the only limit, and exponential growth is just around the corner.
There are many hurdles that have to be crossed.
First, the cost of an RFID tag is a long way off the 1-cent mark, which is the key to exponential growth.
Second, there is the cost of RFID implementation. Who is going to pay for that at the supplier's and retailer's end? Then, there is also the question of paying for the RFID tags on each product. Besides the RFID label you need to install readers and software systems, too. These figures can be significant.
Let's look at the challenges facing converters. We must remember the factor that drives the price down will be the ability of suppliers in the chain to provide economies of scale.
There is plenty of confusion in the marketplace. Some label converters think they can just enter the market. It just isn't like that. RFID has more in common with electronics than it does labels with regard to know-how, and it takes a lot of investment in time and training to get the necessary know-how.
Many are still waiting on the sidelines. What factors are putting them off from joining in?
It is a big investment for a converter. They have to consider the cost of buying converting systems, as well as the cost of hiring staff, training, acquiring the software, research and development, and setting up the quality controls.
Can investment in RFID-making equipment be justified if there is doubt about whether the same standards for RFID production will still be in place in ten, five, or even two years? Some confirmation there would help greatly.
So, it is a chicken and egg situation: converters and their customers wait on the sidelines till the prices come down, yet this will never happen until there are enough players in the market.
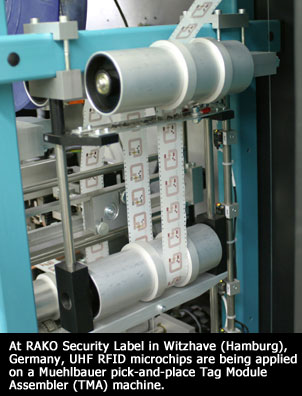
On the positive side, it is good to see partnerships emerging all along the chain, with component manufacturers working together. It is only though close collaboration that improvements and, ultimately, cost-reductions will come that will lead to the predictions of RFID's exponential growth coming true.
The picture is not yet clear as to which frequency is going to be the most commonly used. In fact, there is every good reason to imagine that a number of frequencies will be in operation for some time to come. But one thing is certain. Rotary screen offers a very accurate and fast means of applying the ink or etch-resistant material in all but the low-frequency antenna situations.
Bear in mind also that a dedicated line gives you the option to produce other "functional" labels whose purpose is to identify rather than be decorative. Electro-luminescent labels, thermo-chromic labels, the magnetic stripe on scratch-cards, and scratch-off applications, like lottery cards, are examples.
SUPPLIER INFO:
Stork Prints - storkprints.com
For more information or print samples, contact John Costenobble at Stork Prints; john.costenoble@stork.com.
Part 1 | Part 2