How Closed-Loop Integrated Motors are Meeting the Demand for Higher Acceleration Rates and Faster Machine Cycles
- Published: March 09, 2020
By Eric Rice, Marketing Director at Applied Motion Products
Step motors provide a low-cost and simple solution for high-resolution positioning in a variety of motion control applications, such as those with well-defined and predictable loads, repetitive motion and low speed. Examples include indexing, positioning, inserting, feed-to-length, desktop printers, ATMs and security cameras.
While inherently precise due to their toothed rotors and stators that create a fine resolution for positioning tasks, open-loop step motors have limitations with torque and acceleration. Peak torque is important for today’s high-throughput production machinery that requires motors to operate reliably with high acceleration and deceleration rates.
Because step motors produce less torque at high speeds, they can misstep or stall if overloaded. Step motors are most commonly operated as open-loop systems in which the motor’s position, velocity and acceleration are controlled without any feedback device. Without an encoder or another device to provide feedback about motor position, velocity and torque, the controller is unaware of how the step motor is moving. Missed steps or stall conditions at the step motor can result in machine malfunctions. Having to reset motor position or adjust operating parameters results in downtime, affecting machine throughput.
When more torque is needed or machine performance is upgraded, moving to a larger motor size is often not an option due to space limitations, heat problems or cost. Besides, retrofitting for a larger step motor can be time-consuming and expensive, requiring new mounting brackets, power supplies and even an increased drive size.
Closed-Loop Step Motors Outperform Open-Loop systems
Closed-loop step motor systems offer many advantages over their open-loop counterparts including higher torque to accelerate and decelerate faster, better addressing today’s high-throughput and high-speed processes.

Adding a low-cost, high-resolution encoder closes the loop around step motor performance (see Graphic 1), providing feedback to the drive that enables constant monitoring in real-time of the step motor’s actual position and velocity. By adding servo-control features to the step motor system, the drive can control the current in the motor to eliminate some of the biggest challenges with open-loop step motors: position errors and stall conditions.
While open-loop step motors operate at the full current all the time, regardless of demanded torque, closed-loop step motors operate with just enough current to move the load accurately. As a result, they operate cooler and consume up to 2/3 less power than open-loop motors, which greatly improves motor efficiency. A closed-loop step motor also can create peak torques up to 50 percent higher than a traditional step motor of the same frame size. A video that demonstrates how closed-loop step motor systems outperform traditional open-loop step motors in terms of torque can be found online at https://youtube/lp-9138HQ5E.
When the load increases, a closed-loop step motor adjusts by automatically increasing torque instead of stalling due to rotor lag. Boosting torque higher than the rated holding torque increases the limits of acceleration, leading to faster cycle times and greater throughput. A comparison of move profiles between open- and closed-loop step motor systems shows how the latter benefits from higher torque performance (Graphic 2).
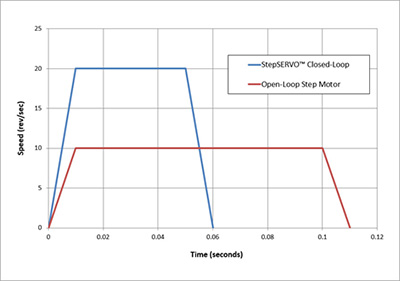
Closed-Loop Integrated Motors Decrease Space Requirements
An integrated motor design incorporates the drive, power, communication and I/O electronics in the same package as the motor (Graphic 3). This space-saving design means reduced cost and less panel space required per axis. The elimination of wiring between the drive and motor saves cost and allows easy mounting of motors all over the machine.
Closed-loop integrated step motors are ideal for applications that require high torque but have limited panel space available. They provide the same performance as separate motor and drive components but with cost savings due to reduced wiring, smaller control panels, reduced bills of materials and simplified maintenance. In combination with closed-loop control of the step motor, integrated motors offer a range of communication options (Ethernet, EtherNet/IP, Modbus, CANopen, etc.) and modes of operation (positioning, velocity control, torque control, stored program execution, etc.) that permit their use in a wide variety of machine designs. Upgrading to a closed-loop integrated motor is not difficult as it most often entails replacing the same size step motor but with reduced wiring requirements.
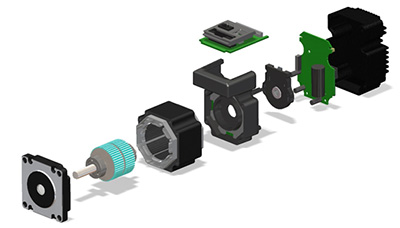
About the Author
Eric Rice graduated with a degree in electrical engineering from the University of Illinois Urbana-Champaign and joined Applied Motion Products as an Application Engineer in 1997. He has worked in the motion control industry for 20 years, specializing in step motors, servo motors, drives and controls.