How to Drive a Winding Roll
- Published: December 01, 2006, By Timothy J. Walker, TJWalker & Assoc. Inc.
Web Lines
What is the best way to drive a winding roll? You have three choices: from the surface, from the center, or both.
The default answer in the converting industry seems to be center winding. Grab the core, connect to a motor or clutch, and start cranking. Center winding can be improved by using a close-proximity gap roller or a nip roller controlling the web’s entry into winding.
In pure surface winding, the core is idling. All the work to drive the roll is applied to the roll’s surface via a driven roller (or belt). Surface winding dominates the paper industry but is less common in the rest of the converting industry.
How do you choose between center and surface winding? Here’s a short survey to lead you to the right answer for your product.
How big is your final roll diameter relative to your core diameter (a.k.a. the roll build-up ratio)? Center winders definitely have more trouble with larger build-up ratios. A center winder’s torque and motor size will be a direct function of final tension and radius. Also, center winding transmits the core-applied torque to all the winding roll’s layers. If you have marginal friction or pressure within your roll, the increasing torque of large build-up ratio often will cause slippage, cinching, and telescoping.
Surface winders don’t care about roll size and don’t have the same internal roll friction needs. A surface winder’s torque is transmitted at the surface via a constant diameter roller, so larger rolls don’t need more torque or larger motors. Do you need automatic at-speed roll transfers? At higher process speeds, you can’t design an accumulator big enough for a zero-speed transfer system, so you need an at-speed transfer system.
At-speed, auto-transfer center winders are common in the converting industry. Auto-center winders use two spindles: one for winding and transfer, the other for roll unloading, core loading, and auto-splice preparation. Since each winding spindle is driven, it’s easy to drive the empty core to web speed before transfer. Many equipment suppliers have inventive (and patented) ways to sever the web from the finished roll and attach it to the new core. Automatic transfers on surface winder, though not impossible, are more complicated and are made by dramatically fewer equipment suppliers.
Do you need tighter or looser rolls? Both winder styles can produce a wide range of roll tightness with adjustments to winding tension, torque, and nip force, but center winding always will tend to make tighter rolls and surface winding looser rolls. Surface winders have an especially hard time tightening up a roll with a loose core start.
Is your product nip-sensitive? Most surface winders use a nip, but some special designs drive the roll with a surface belt. Center winding is the more common nip-free winding option.
Is your product porous? In surface winding, the air that slips through the winding nip can get caught ahead of the nip point in the roll’s topmost layer. As the trapped air bubble grows, it will create wrinkling in thinner products. Porous products don’t face this potential surface winding liability, since the air just leaks out through the web. Why center winding doesn’t have this trapped bubble problem is unclear, but likely it is related to the tightening direction of the nip-induced tension and slippage.
Why would you ever do both? Center-surface winding seems like a “belt and suspenders” approach. Most center-surface winders are really just modified surface winders with a center-assist option. Having a torque-driven core on a surface winder can help tighten up loose starts, speed match a new core for the auto-transfer process, and control the deceleration of the finished roll. Center, surface, belt, suspenders, or all of the above—choose the option that keeps your rolls fit and your pants up.
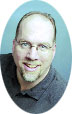
Timothy J. Walker has 20+ years of experience in web handling processes. He specializes in web handling education, process development, and production problem solving. Contact him at 651/686-5400; jwalker@tjwa.com; tjwa.com.