Advances in Coating
- Published: March 31, 2005, By Edward D. Cohen, Edward D. Cohen Consulting
Coating Equipment
Recent technology advances in web coating have led to an improved process with the capability to produce products with a wide range of characteristics. These advances have occurred in all parts of the process, with major advances in coating application, on-line inspection instrumentation, and process control systems.
Coating Application
The use of pre-metered coaters has increased significantly because of advances in the coating applicator technology and hardware. They are being used to replace various roll coating techniques in both existing and new coaters because of superior characteristics. In this method, the coating solution is metered to the applicator and all of the material is transferred to the web. There are three types of applicators in this class of coaters: slot die, curtain, and slide, and all of them are available commercially from several vendors.
Fundamental R&D studies led to an understanding of the basic fluid flow mechanisms in these applicators and the development of computer models to simulate the die performance. This technology has been transferred to coater manufacturers and now is in routine use to design the applicator and optimize coating solution rheology. As a result, an applicator can be custom designed for specific product requirements, and sophisticated configurations can be designed readily. This capability previously was restricted to large, technically sophisticated companies. Now it is available to all and has resulted in the major increase in usage.
Advances in metal fabricating machines and measurement techniques led to the fabrication of applicators with very tight tolerances over increased widths. These applicators can coat at increased speed, with an improved coating weight uniformity and the ability to apply coatings as thin as 0.025 micron. The overall quality, uniformity, and precision of the applicators have increased, and they are cost-effective.
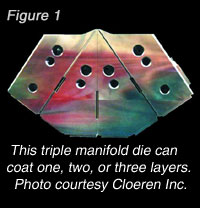
These applicators can coat several layers simultaneously. Three-layer slot dies now are commercially available. Figure 1 shows a triple manifold die that can coat one, two, or three layers. The slot die and curtain coaters can coat in excess of 12 layers if needed (see Figure 2). These methods have an advantage over the previous multilayer coatings, which required several passes through the coater or multiple in-line coaters. The availability of this capability will allow development of product concepts that previously were not economically feasible.
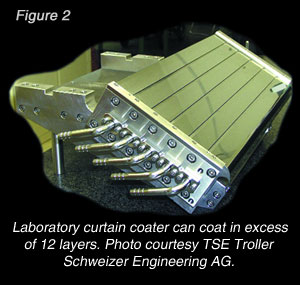
The patents on an improved version of the curtain coater recently expired, and now they are available from coater vendors. It is a multilayer applicator, which uses precision edge guides to stabilize the curtain. The major advantages of curtain coating are that it can produce high quality coating uniformity, reduce defect levels because of the wide gap, and apply uniform coating weight at line speeds in excess of 3,000 fpm. Figure 3 shows a curtain applying pressure-sensitive adhesive at 100 mpm.
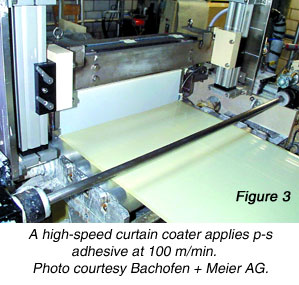
Advances in coating station support, station technology, fabrication, and measurement capability have contributed to improved product quality and coatability. Cartridge coaters were developed to replace the standard single-method coating station. This permitted multiple coater techniques to be available for rapid insertion into the coating line, thereby increasing the flexibility of the process and allowing the correct method to be used for each product. The designs and fabrication of the coating station are more rigid to prevent chatter-induced vibrations and to maintain settings throughout a long run. Precision positioning systems were developed to allow precise settings and maintenance of applicator settings throughout a long coating campaign. New measurement technology permits continuous precise measurement of gap setting. The combination of improved die machining and measurement capability and precision positioning systems has resulted in precision coating dies with widths of more than 100 in. (see Figure 4). Dies with reduced precision can be fabricated in widths to 300 in.
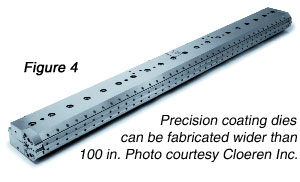
On-Line Inspection
As a result of advances in technical capability and cost-effectiveness, on-line measurement instruments have found widespread use on web coating lines and have become an integral part of the quality control program. Their use can lead to improved product quality and a reduced level of physical defects. Previously, product quality parameters such as coating weight and defect levels were measured by sampling the roll and measuring off-line in the laboratory. As coating speeds increased, this method could result in a large amount of defective material being produced before testing was complete.
Coating weight and thickness is a key parameter for all coated products. On-line coating weight measurement equipment has been developed that gives rapid, accurate measurements. The web can be 100% inspected and average coating weight and cross web profiles calculated. This equipment permits rapid corrective action if out-of-spec material is detected. Also, the real-time capability of these measurements permits rapid startups and reduced downtime. In addition, operating variables can be optimized since results of process changes can be seen immediately. These measurements can be incorporated into a control loop. The instruments also can be equipped with data storage and analysis capability, so past and current runs can be analyzed and compared. There are a variety of on-line measurement technologies available that permit a wide range of substrates and coating weights to be measured. These include beta transmission, contact and noncontact caliper, gamma backscatter near infrared, X-ray transmission, and X-ray fluorescence.
Coating physical defects is another key property that can be evaluated in real time with on-line web inspectors. The first generation of web inspectors were expensive because they were custom-fabricated for specific applications, and the cost of the component’s software was high. The recently developed generation of web inspectors has improved optics, electronics, and software to analyze, display, and store defects information. Their increased computing power permits vastly improved sensitivity. They can detect a wide range of defects, spots, dirt, streaks, chatter, etc., at high line speeds over the entire web. Also, the purchase costs have been reduced significantly. There are several detection technologies—cameras, laser scanners, reflection, transmission—that can be configured to cover a wide variety of web types and defects. Adding them to a web coating line will provide rapid defect detection and the ability to initiate troubleshooting procedures rapidly, thereby reducing the amount of scrap material produced.
Process Control Systems
There have been major advances in the systems that monitor and control all of the coater process variables. The current systems are based on digital microprocessors, which integrate the control of all these systems to ensure effective operation of the entire coater. The reduction in microprocessor costs and increase in performance have resulted in powerful, cost-effective systems that can be used for any coater. The increased computing power permits advanced process control concepts to optimize coater performance and achieve more precise control. Also, their rapid response results in a steady state being reached rapidly, which reduces scrap produced during this start-up period. This is advantageous particularly for high-speed coatings. These systems also can be used to manage all the recipes for setting the coater conditions, preparing solutions, and storing and analyzing process data. Systems can be accessed over the Internet, which facilitates troubleshooting.
Future Advances
Current advances in coating technology will gain wider use as the technology and cost-effectiveness of the hardware are improved. This will result in improved quality and productivity, thinner applied coatings, increased uniformity, and higher line speeds. There should be an increase in multilayer products since multilayer coaters are readily available.
New technology also will be introduced in several other areas. Improved coating formulations based on nanotechnology will be available. They will find widespread commercial application to provide products with improved scratch resistance, barrier layer performance, nonstick performance, abrasion-resistance conductivity, and antibacterial properties. The miniaturization of the ink jet nozzle will lead to its increased use as a web coating technique to provide thin, discrete coatings. Improved dispersion and stabilization technology will permit coating of very small particles and thinner coatings.
Edward D. Cohen is a technical consultant in all aspects of the web coating process. His expertise is in the coating and drying of thin films, coating process development and scale-up, polyester base development, film defect mechanisms, and defect characterization techniques. He has more than 40 years of experience in coating research and manufacturing technology and has extensive publications in the field including two books. Currently he is technical consultant for the AIMCAL. He can be reached at 480/836-9452; This email address is being protected from spambots. You need JavaScript enabled to view it..
This article, along with future articles by other authors, is provided as a cooperative effort between PFFC and AIMCAL. Authors contribute to AIMCAL’s technical and education offerings, which include the association’s Fall Technical Conference, Summer School, and Ask AIMCAL.