Atmospheric Plasma Treatment
- Published: April 01, 2022, By Josh Scanlan
SOFTAL Offers a Practical Solution for Improving Adhesion on Thermally Sensitive Materials, Thick Materials, Embedded Electronics, Foam, Panels and More.
Atmospheric plasma and corona technology have been widely used for many decades for the surface treatment of polymers and more. Both methods are used to modify a substrate’s surface energy to improve the adhesion of inks, lacquers, adhesives, and coatings. Corona treatment is the most the most popular surface treatment method in the plastic film, extrusion, and converting industries. It is economical and adaptable to many applications such as high-speed printing presses, blown film applications, and extrusion coating applications.
However, conventional corona technology can be limited to two-dimensional materials with thicknesses of only a couple of millimeters. Other challenges include, heat damage on delicate and thin substrates and embedded circuitry and metals cannot be treated due to the electrical discharge of corona treatment.
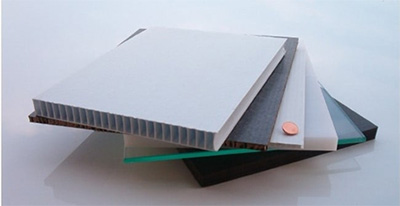
What motivated SOFTAL Corona & Plasma to develop the LinearPlasma system?
With these limitations in mind, Hamburg-based SOFTAL Corona & Plasma developed its patented LinearPlasma system. This system uses a method similar to corona treatment, however LinearPlasma has the ability to process delicate substrates due to the lower temperature of plasma discharge. And without a counter electrode, there are no restrictions on a substrates thickness or makeup. Unlike corona discharge, LinearPlasma does not cause streamers, heat damage, and flawed edges.
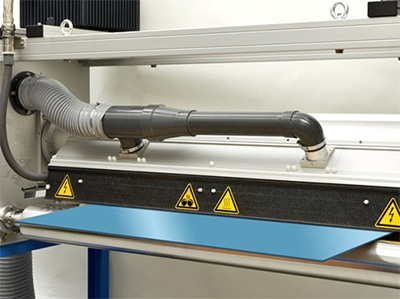
What types of materials and applications is LinearPlasma best suited?
LinearPlasma opens up numerous surface treating applications such as, treating wide materials (up to 2 meters wide) and thick materials without the necessity of a counter electrode. Plasma works well for surface treating panels and foam. LinearPlasma also effectively treats extruded boards without any problem.
SOFTAL’s LinearPlasma capabilities include the surface treatment of printed electronics. These sensitive materials, which are increasingly embedded in state-of-the-art packaging and technical film require non-conductive surface treatment. Electric circuits inside the film are damaged by corona treatment, but this is avoided when using LinearPlasma which is potential-free.
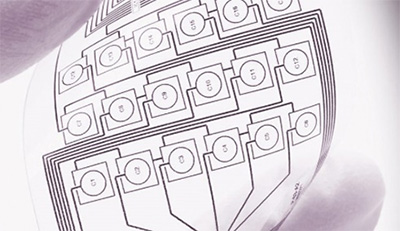
Plasma Treatment Improves Adhesion on These Materials and Applications:
- Thick polymer sheets
- Foam, open and closed pore
- Metal & alloy sheets
- Glass plates
- Composites
- Optical Film
- Thermally sensitive film
- Embedded electronics
- Multiwall panels
Are there other benefits unique to SOFTAL’s atmospheric plasma system?
Beyond increasing surface energy and promoting powerful adhesion, atmospheric plasma will clean surfaces to remove contamination and physically etch surfaces aiding in bonding. LinearPlasma can be configured to produce a voltage-free stream of energy capable of cleaning the surfaces of stainless steel, aluminum, and various alloys for improved adhesion by removing lubricants, coolants, and release agents often used in the production of metallic components. LinearPlasma improves the adhesion for subsequent processes such as gluing, painting, laser welding and over-molding.
Plasma treatment is environmentally friendly because it does not produce ozone. LinearPlasma treated surfaces works well with water-based paints, inks, and adhesives and do not require primers. Plasma is safer than flame surface treatment.
Importantly, LinearPlasma is easy to use and integrate into production lines. It provides repeatable, process-controlled operation, with high efficiency with low operating costs.
How does atmospheric plasma treatment function?
During Linear Plasma’s treatment the plasma discharge causes chemical reactions in the air within the electrode gap and on the polymer surface. The result is the chemical restructuring of functional groups, such as hydroxides, ketones, ethers and carboxylic acids to the polymer surface. The newly created polar groups on the surface now readily form strong bonds with inks, coatings, adhesives, etc.
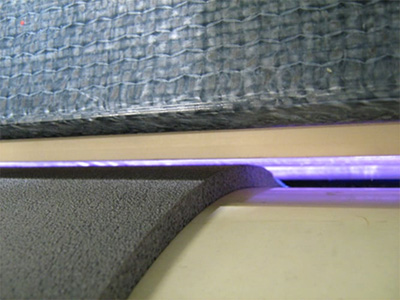
What other solutions does SOFTAL Corona & Plasma provide for the film and converting industries?
SOFTAL Corona & Plasma produces a full range of powerful, dependable corona and plasma surface systems designed to raise the surface energy and adhesion properties of numerous substrates. Printing inks, lacquers and adhesives thoroughly wet out once treated with SOFTAL’s technology. More than 60 years of surface treatment experience has made SOFTAL a world leader and the benchmark in surface treatment technology.
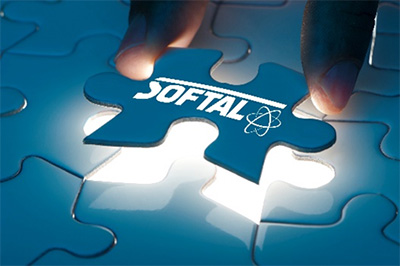
SOFTAL’s Corona & Plasma Systems:
- Produce optimal bonding for printing, coating, laminating and adhesive applications
- Reliable performance, robust design for maximum up-time and productivity
- Capable of meeting any line speed per specification
- Individual corona generator power: up to 144 kW, twice as much as conventional generators on the market
- Corona stations - from 10 inches to 10 meters - with single or multiple electrode assemblies
- Modular generator technology overcome the performance limitations of a single generator and keep systems running
- Stand-alone, high-performance ozone filter and destruction system
- Low energy requirements and operating costs
- Potential-free plasma stations for delicate films, thicker materials, glass, metal and printed electronics
SOFTAL is represented in the USA, Canada and Mexico by 3DT LLC of Germantown, Wisconsin; providing state-of the-art German engineering with U.S. sales, service and support. This strategic partnership provides solutions to numerous adhesion challenges in both the film and 3D industries. 3DT manufactures a broad line of surface treatment systems, all customizable for unique applications. For more information contact sales@3DTLLC.com or visit our website at www.3DTLLC.com.