Rx for ER
- Published: May 01, 2009, By By Edward Boyle, Contributing Editor
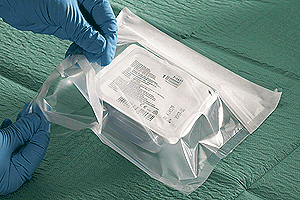
Rollprint Packaging Products Corp. recently celebrated its 75th anniversary as a worldwide supplier of flexible packaging materials for the healthcare and food industries. Yet company president Dhuanne Dodrill says the Chicago-area converter still maintains the innovative spirit of a startup. And that, she says, has been the real secret behind the company's longevity and ongoing success.
“Going forward, we want to continue our focus on leading-edge technologies and custom applications,” says Dodrill. “But we also will be applying our expertise to additional mainstream products. We realize that today's healthcare and food packers require both innovative and traditional structures, and we want Rollprint to be the company that can fulfill all of their flexible packaging needs.”
As evidence of that entrepreneurial spirit, Rollprint recently developed two major product innovations. The company introduced Triad (see PFFC, March 2009, p62), an extrusion-coated lamination of polyester, aluminum foil, and metallocene that has been engineered to provide an exceptionally strong hermetic weld seal in high-speed, chemically sensitive, pharmaceutical applications.
“Triad has terrific seal properties that allow you to run at extremely high speeds and still be assured of achieving hermetic seals,” says Dodrill. “It has excellent barrier properties and great bonds, so if you have a tear-open package, you don't have to worry about webbing and stringing; it just tears open easily. Delamination is simply not a concern. In addition, Triad contains no solvents.”
Focus Group Feedback
Rollprint also developed a new generation, peelable chevron header pouch called Duet, which reduces costs while offering improved aseptic presentation of medical products. Dodrill explains that Rollprint took an innovative approach to developing Duet, in particular: The company actually convened a focus group of operating room nurses and doctors to determine what they want in a flexible package, then incorporated those insights into a new product.
“We designed the Duet around the feedback we got from the focus group; the things they liked about the packaging and what they wanted changed,” explains Dodrill. “There was an awful lot they didn't like, so it was really eye-opening.”
Duet's new hybrid design combines elements from both header bags and chevron pouches, a further expansion of one of its premier product lines.
Among its many advantages to the end-user, Duet reduces the amount of Tyvek typically found on a chevron pouch by borrowing the “header” concept from the bag, thereby removing cost. A strip of Tyvek is heat sealed to a polyester/extrusion-coated sealant to create one side of the structure. The next step is to three-side heat seal the Tyvek/film combination to a layer of polyester/poly. (The top Tyvek area is left unsealed so the medical product can be loaded later.)
At the bottom, the polyester/extrusion-coated layer extends slightly beyond the polyester/poly film side, creating access tabs at both corners where a dual chevron opening feature has been created. The pouch is sent to the sterile medical packager with the chevron or bottom access seals already in place. The device or kit is loaded from the top end where the Tyvek and film are to be heat-sealed.
Page 2 of 2
The dual chevron at the outer edge of the structure makes it easier for operating room personnel to open and remove challenging three-dimensional geometries — such as trays, tubing, and various kits — without flaps potentially compromising the aseptic presentation.
“I think it was quite clever,” says Dodrill, noting that the product won a 2008 Flexible Packaging Assn. silver award for Technical Innovation.
A Global Imprint
Dodrill says Duet is just the most visible example of what Rollprint does on an ongoing basis. “We really listen to what our customers' needs and requirements are and help them achieve their goals. Often it may be [by using] a standard product offering, but then it may be something different and unique. We have a tremendous range of technologies that we can draw from and combine to create some very unique materials that can help a customer be the most competitive they can be.”
And the company certainly has the resources to do just that. Rollprint's two Addison, IL, converting facilities encompass a combined 200,000 sq ft.
Its capabilities include Egan extrusion coating and laminating equipment from Davis-Standard, Schiavi adhesive coating and laminating equipment from Bobst Group, and Brampton Engineering blown film lines. Flexographic printing to six colors is accomplished on a Schiavi Sirio press. Dusenbery slitting equipment is supplied by Parkinson Technologies.
Rollprint also converts a range of custom pouches that incorporate unique combinations of film, foil, paper, and Tyvek to meet a variety of end-use needs. Equipment suppliers include GN Packaging Equipment and CMD Corp.
In addition to its many product introductions, Rollprint expanded its geographic reach several years ago by forming Alliantz Flexible Packaging, a joint venture with Acme Packaging Co. (Pte) Ltd. in Singapore, to serve the flexible packaging supply needs of Southeast Asia and China.
“Increasingly, we are all becoming part of a global economy,” Dodrill explains. “As a result, one of our goals is to continue to expand Rollprint's worldwide imprint through acquisitions.”
Innovative Structures
Rollprint has become known for its extrusion coating expertise in the past decade, notes Dodrill. “Our polyester sealants are particularly unique. We started with extrusion coating polyester sealants into film, and then expanded into peelable extrusion-coated polyester sealants,” she says. “Our structures have very good temperature resistance. They are ideal for high heat applications, such as dry heat or autoclave sterilization methods. Another desirable aspect of polyester sealants is that they are chemically ‘clean.’ They don't leach into nor do they tend to scalp compounds out of products.”
With regulatory agencies continuing to press against the use of solvent-based materials (and those containing isocyanates) in pharmaceutical applications, these structures were developed to meet these objectives without sacrificing performance. Historically, many competitive solvent-free structures have been known to come up short in machineability speed, seal strength, and/or cost, recalls Dodrill.
To support its innovation efforts, Dodrill says Rollprint has instituted a sophisticated R&D system that “eliminates duplication of efforts. It's a great communication tool, and it maintains strict design control practices.” She notes that both Triad and Duet, among others, went through the process, along with new customer product requests. “We really provide service in all aspects of the business,” says Dodrill. “From the development of the packaging projects and materials, we provide technical assistance and support to allow customers to validate the products and to ensure that they're running optimally on their equipment. We've got a very talented team and state-of-the-art laboratory to support our customers. And once the business is ongoing, we provide terrific support from that end as well.
“We track our customers' loyalty, and we don't see customers leaving,” says Dodrill. “They usually feel like they've found a good home when they come to Rollprint, and we work very hard to make them feel that way.”
Contributing editor Edward Boyle, based in Reading, PA, has covered the converting industry for more than 24 years. Contact him at EJB Communications; 610-670-4680; ejbcomm@aol.com.
A (Family) History of Innovation
Rollprint Packaging Products Inc. was founded in 1933 as Schenker Printing Co. and was purchased by the Dodrill family in 1975. The company flourished under Robert Dodrill, who continues today as chairman of the board. Dhuanne Dodrill, fourth president of the family-run company, says her father was instrumental in bringing a new level of technological innovation to the flexible packaging sector.
One of the first introductions under his leadership was Rollprint's RP-1A heat-seal coating. Its very broad operating window continues to make it a frequently specified product today. Additionally, in the late 1960s, the company was one of the first to introduce coated Tyvek to the healthcare market. In 1969, Rollprint patented what is now known as the header pouch. This marked the company's entrance into medical packaging, which has since become its major market.
Converter Info
▶Rollprint Packaging Products Inc. | 320 S. Stewart Ave., Addison IL 60101 | 800-276-7629 | www.rollprint.com
Supplier Info
▶Davis-Standard Converting Systems Group | www.bc-egan.com
Circle 316 or visit www.freeproductinfo.net/pff
▶Bobst Group | www.bobstgroup.com
Circle 317 or visit www.freeproductinfo.net/pff
▶Brampton Engineering | www.be-ca.com
Circle 318 or visit www.freeproductinfo.net/pff
▶Dusenbery | www.dusenbery.com
Circle 319 or visit www.freeproductinfo.net/pff
▶GN Packaging Equipment | www.gnpak.com
Circle 320 or visit www.freeproductinfo.net/pff
▶CMD Corp. | www.cmd-corp.com
Circle 321 or visit www.freeproductinfo.net/pff