Why so Tense?
- Published: January 01, 2010, By Edited by Nsenga Byrd Thompson, Assoc. Editor
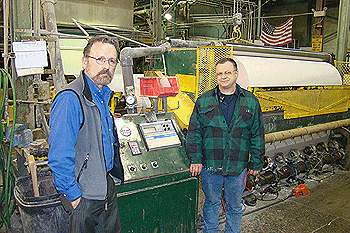
Putney Paper is located on the same site where papermaking has been a continuous process since 1818. In addition to its long-standing mill, Putney has been a manufacturer of converted paper products for more than 45 years, supplying a host of well-known companies across the US.
A major part of Putney's operation is the production of tissue paper rolls, with a critical stage being the slitting/rewinding process. The company's workhorse slitter/rewinder previously was equipped with old-style load cells that didn't retain calibration — a critical function to rewind rolls of tissue properly. Putney recognized it needed load cells that were durable and reliable to receive maximum productivity.
To find a cost-effective solution to its dilemma, Putney turned to The Montalvo Corp. to replace the old-style load cells with new U-50 load cells. Problem solved.
How Putney Rolls
According to David Brownell, mill superintendent, “The U-Series is used on our slitter/rewinder for tension control. We require constant and reliable tension because we run lightweight papers. The new load cells are rugged and reliable and hold the roll tight; there are no wrinkles, no tears now.”
In addition to tissue paper, Putney's other paper products include napkins, paper towels, packing for shoes and hats, wrapping paper, etc. Each product requires a different tension setting that had to be changed manually by the operators. If there was too much tension, they had to stop, splice the roll, and re-set. Now, using Montalvo's U-50 load cells with its S-3000 controller, the problem of zero drift has been resolved.
The load cells are calibrated using a known weight. When the weight is removed, the cells should go back to zero, and once a couple of rolls are run, they still should return to zero. That wasn't happening with the older load cells.
“We used to lose about 15 minutes per hour on that slitter/rewinder. Now we may lose perhaps a half-hour per day — and that's due to roll changes or some other issue. We no longer lose time because of load cell performance,” Brownell says.
Montalvo's 1400 series brake also is used on the machine. The S-3000 controller reads and sets the tension on the rolls and sends a signal to the output device (the brake) to acquire the precise tension needed for any weight of paper.
Brownell says the equipment runs at 2,300 fpm, and products at Putney are rewound to a 3-in. core and then sent to the converting plant. Rolls can be 92 in. wide with 30-48 in. dia, depending on the customer's order. They are normally slit to widths between 14½ and 90 in. for further processing downline.
Putney converts about 50 tons of paper products per day and has overall annual sales of about $30 million. The 150-employee operation takes pride in diverse product offerings that are made entirely from 100% recycled paper.
Supplier Info
-
The Montalvo Corp. | www.montalvo.com
Circle 304 or visit www.freeproductinfo.net/pff
Converter Info
-
Putney Paper Co. | PO Box 226, Putney, VT 05346 | 802-387-5571 | www.putneypaper.com