Allied Printing Services Leads Way with U.S. and World-First Technologies
- Published: January 04, 2024
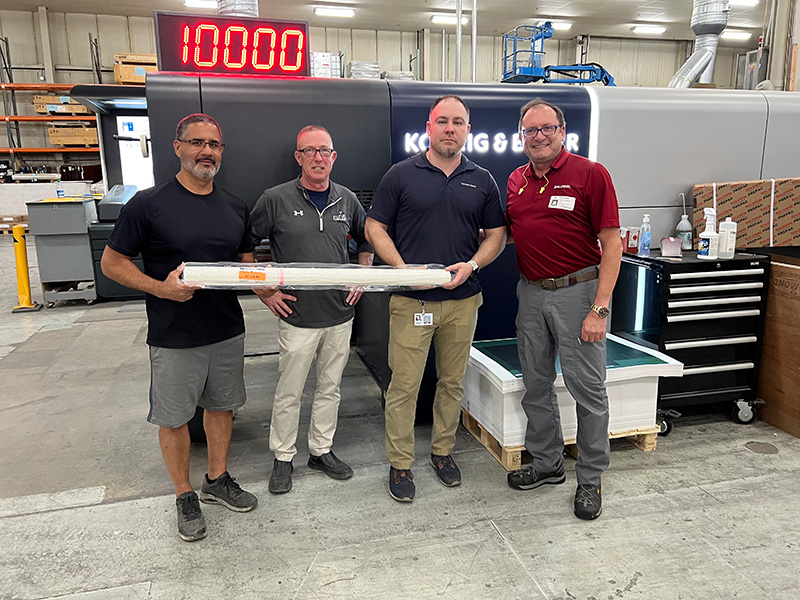
On the cusp of its 75th anniversary, Allied Printing Services remains successful and competitive in large part due to the company (and companies) it keeps in its orbit of like-minded and resilient innovators. The Manchester, Connecticut-based printer, one of the largest family-owned commercial printers in the Northeast, is leading the way with first in the U.S. and world technology investments.
2023 is the latest benchmark in its storied history with Allied now holding the dual distinction as the first printer in the U.S. to operate a Koenig & Bauer Rapida 106 X double coater UV perfector press and the first in the world to configure it with Baldwin Technology’s PREPAC automated blanket-washing system.
WATCH THE VIDEO: https://baldwintech.com/blog/2023/12/11/
allied-printing-services-leads-way-with-us-and-world-first-technologies
According to Koenig & Bauer (K&B), its new Allied Printing Services press is a specially configured eight-color four-over-four perfector operating at 18,000 sph that is capable of both conventional and UV printing. It is designed with four print units, plus coater, two drying towers, another four units, and another coater with a 12-ft delivery.
“The Rapida 106 X gives us so much opportunity and differentiates us from our competitors,” said John Sommers, President and CEO of Allied Printing Services. “It’s like a Swiss Army knife with multiple tools and advantages – it's a game changer for our business, showing the versatility, creativity, high quality and speed to market that we can deliver to our customers.”
Allied serves a broad base of customers from its 30-acre campus, including the financial, healthcare, education, manufacturing, pharmaceutical, automotive, biotechnology, travel and leisure and retail sectors.
Upholding its well-earned legacy of superior customer service and results requires Allied Printing Services to continually upgrade and optimize its people, processes and equipment. From first interaction to final delivery, no detail is unworthy of scrutiny, including its press cleaning protocols.
Enter St. Louis, MO-based Baldwin Technology and its PREPAC automatic blanket-washing system that features “pre-impregnated” cloth rolls that provide high ink and lint absorption capacity. PREPAC enables Allied Printing Services to achieve results that are 100 percent accurate and efficient with every ABC (automatic blanket cleaner) wash.
“Baldwin PREPAC is the only cloth we wanted on that machine,” said Gerry Dugan, Sheetfed Manager at Allied Printing Services. “We tested other options and there’s just no comparison – PREPAC is more efficient and requires no clean-up and no need for multiple solvents.”
By replacing the dry cloth/solvent-dispensing wash system on the standard K&B equipment, Allied Printing Services can now make faster make readies and eliminate the many downsides to common solvent-dispensing systems.
“We run PREPACs on all of our other machines, including our K&Bs and Komori web presses, and we demanded that PREPAC be used on the new K&B,” said Kevin Howard, VP Sheetfed, Web, and Postpress at Allied Printing Services. “They are superior to competitive products which we discovered dried out quickly and did not clean as well.”
Baldwin’s proprietary solvent contains the lowest VOC content on the market. In addition to its superior cleaning capabilities, it is non-toxic, non-hazardous, and allows printers to minimize their VOC footprint.
As the designer and inventor of PREPAC, Baldwin continually collaborates with Allied and its other customers to continually help them to improve productivity, leaning on the engineering expertise of its seasoned teams and leveraging its more than 100 years of printing industry leadership.
With consistent, uniform distribution of solvent on the cloth, PREPAC saves the hassle and sizable costs of replacing blankets due to uneven solvent distribution or no solvent spraying, as commonly experienced with such systems in demanding, high productivity environments.