A Family of Possibilities
- Published: February 28, 2006, By Nsenga Byrd Thompson, Associate Editor
Folding Cartons
When George Keyser purchased Utah Box and Label in 1922, he had more than labels on his mind. Changing its name to Utah Paperbox, the company’s focus moved to rigid boxes. In the late 1960s, the emphasis shifted once again, this time to folding cartons, adding offset printing and platen die-cutting to the mix.
It was with the production of folding cartons that the business flourished. By the ’90s, folding cartons accounted for 85% of sales. In 2000 Utah Paperbox entered the litho laminating business, considerably expanding packaging options for its customers.
As the third generation to oversee operations, CEO Paul Keyser—a driving force in the company’s entry into folding cartons—attributes UPB’s continued success to its strong sense of family (that includes employees as well as son Steve, who is VP of sales), sizeable investments in prepress and printing, and being a one-stop shop for customers.
With 210 employees working three shifts, five days a week, the company is home to three divisions: Folding Cartons, Rigid Paper Box, and Litho Laminate Containers, and is affiliated with Wasatch Container (which offers point-of-purchase displays, corrugated shipping containers (RSCs) and protective packaging using foam).
Tools of the Trade |
---|
Laser die burner: Data Technology |
Router: Elcede/Ferranti |
Computerized rule bender: Adams |
Window Machine: Heiber/Schröder 1400 Matic |
Foil stamper: Steuer |
Bleached board: International Paper, Smurfit, and Potlach |
Coated natural kraft: MeadWestvaco |
Solid unbleached sulphate: Graphic Packaging Intl. |
Ink: Graphic Ink and INX |
Prepress: Macintosh and ArtPro |
Proofing: Creo, Epson |
The company has full-service prepress operations. Plates are made digitally on a Creo (now Kodak) VLF platesetter.
UPB’s printing operations have seen extensive changes in the past 12 months. A year ago, the company operated six MAN Roland presses but recently removed three presses for its latest investment: the MAN Roland 707 Plus, designed for high-speed, unitized, sheet-fed printing.
The remaining two presses are a 56-in., seven-color MAN Roland 900 large-format press purchased in 2002 and a 41-in., seven-color MAN Roland 700, featuring interstation UV capabilities.
UPB has an extensive die-cutting operation with six Bobst die-cutters and a Gerber computerized die router. The finishing department features three Kluge stamping presses; a state-of-the-art window machine; a Bobst Alpina 145 folder-gluer, four other Bobst gluers, as well as a Jagenberg 125 gluer.
In addition to two Bobst stamping presses, UPB purchased a high-speed foil stamper, which was installed in February.
Bringing in Flexibility
Although UPB’s print capabilities allowed for maximum capacity and high quality results, the company desired the flexibility of using different inks, in-line perfecting, maximum drying capabilities, and most importantly, the ability to accomplish all of this in one pass. UPB knew it would require the highest level of expertise, so it consulted three press manufacturers to engineer the final configuration of the press. The end result was MAN Roland’s 707 Plus sheet-fed press, which UPB reports offers the company a unique printing experience.
Explains Mike Salazar, VP of operations, “We pulled out three cylinder presses, older technology, and put in a high-speed, unitized printing press perfecter. It’s something that can print the back, flip it over, and print the front in one pass. We were looking at modernizing all of our printing presses—this press did that.”
Taking out three presses for the power of one has been a worthy investment. Salazar and Steve Keyser describe several new capabilities.
“We wanted to tie the flexo ink…to the sheet-fed world in a one-pass solution,” says Salazar. “Flexo pigment gives you a little bit different latitude because of how it is applied to the sheet, and sheet-fed printing presses give you the best quality in the world as far as repeatability and printability. Flexo presses are getting better, but they still [can’t do] what a sheet-fed press will do. So we wanted to have the flexibility to marry those two combinations.”
Adds Keyser, “We also wanted to enter the world of UV and UV hybrid. We had two UV units on the older press, [so] we were limited to two in terms of printing on foil.”
With the 707 Plus, UPB now has UV docking stations after every print unit. The company also added several additional lamps and a drying tower from IST Technotrans.
“Steve’s father knows about drying,” says Salazar. “He made sure we had enough drying capacity. We spent additional money so we can move the lamps wherever we want. We have docking stations between all of the units. What that has done is allowed the marketing people to say, ‘Here’s a few more possibilities we bring to the marketplace.’”
Experience Counts
Bringing in the press as a double delivery installation, UPB was able to have the seven-color, 41-in. press up and running in 45 days. Getting the operators up to speed on the press’s unique capabilities proved to be a smooth transition.
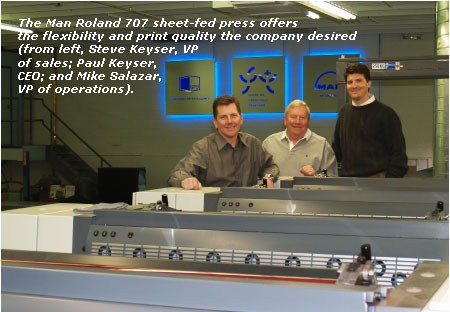
“Part of our decision to stay with MAN Roland was that our operators were familiar with MAN Roland equipment. Fortunately, the majority of our employees have been with us a long time,” says Salazar. “If you come for a press check today, five years from now the same person more than likely will be handling your press check.
“We have a lot of veteran, talented pressman and operators, and those guys do a fantastic job. We are testing a lot of new inks and pigments and doing a lot of different things that challenge the pressmen, but our crews just do a fantastic job of adjusting and making it work,” he says.
Salazar and Keyser have confidence in the investments they have made to bring their customers the highest quality product, but at the end of the day, it’s UPM’s devoted employees and family spirit that bring the company its greatest success. “The thing that is going to make this whole thing work is not the equipment, it’s really the people,” Salazar maintains. “The printing press will print, but you are only as good as your prepress department and your printers.”
With its newfound print capabilities, worrying if it will print shouldn’t be a problem.
CONVERTER INFO:
Utah Paperbox
340 W. 200 South
Salt Lake City, UT 84101
801/363-0093; upbslc.com
SUPPLIER INFO:
MAN Roland—manroland.com
Kodak Graphic Communications Group—graphics.kodak.com
Epson—epson.com
Bobst Group—bobstgroup.com
Kluge—kluge.biz
Jagenberg Inc.—jagenberg.com
IST Technotrans—technotrans.com