Featured Stories
-
Elevating Pouch Manufacturing with Pearl Technologies' Cutting-Edge Solutions
For manufacturers seeking efficiency, precision, and safety in pouch production, Pearl delivers unmatched innovation across three standout... -
Faster Product Composition Analysis Equals Better Quality Assurance
Near Instant Testing and Reduced Costs to be Found -
Methods to Precisely Measure Tension and Web Control
How to Control Automatically Within Set Parameters
News | New Products
-
Nobelus Launches Entry-Level Komfi® Thermal Laminator
FINISHING SOLUTIONS SUPPLIER OFFERS NEW JUNIOR 52 LAMINATING SYSTEM
-
Double E Group Mourns the Loss of Founder and Converting Industry Pioneer, Richard Edward Flagg
Double E Group announces with profound sadness the passing of its founder, Richard Edward “Ed” Flagg, on June 23, 2025. He was 85.
-
Convertech Brand to Fully Transition to Double E Group Same Team, Same Excellence, Unified Name
Double E Group has announced that Convertech, one of its subsidiaries and a trusted provider of core chucks and shaft solutions for the converting industry, will now operate solely under the Double E Group brand.
-
Pulse is Making Print Simple at Labelexpo Europe 2025
Narrow web ink specialist Pulse is Making Print Simple at Labelexpo Europe 2025, as it challenges flexo printers to rethink how they work and shows solutions that turn production bottlenecks into revenue generators.
-
ROTOCON to debut at Labelexpo Europe with three machine demonstrations
ROTOCON will make its Labelexpo Europe debut, exhibiting together with HS Machinery on stand 4D21.
-
At Interphex Japan, IL Group to Showcase Innovative Labeling Solutions and Contract Packaging Services
IL Group, a specialist in multifunctional labeling solutions for the pharmaceuticals and healthcare sectors
-
Revolutionizing Adherence: Clinical Trials Go Digital with Enhanced Key-Pak®
Keystone Folding Box Co., a leading provider of paperboard packaging solutions, has announced a strategic partnership with Med-Con Technologies
Expert Advice
How To Prevent Unwinding Roll Static
- Published: August 01, 2009, By By Dr. Kelly Robinson Contributing Editor
The master roll arrived at your receiving dock right on time. Now, you have the material to complete the job for that important customer. Along with the incoming material, you also may have received plenty of static charge wound into the roll. You can avoid many static problems by doing two things. First, do a quick “static check” on the roll to see if it is “hot.” Next, monitor the static on the unwinding film to verify that your incoming material meets your specifications. If you don't yet have them, your measurements will help you set reasonable specifications. If the roll runs well, you'll know what static level is acceptable. If you have static problems, or if you receive complaints from your customer, you'll know what level causes problems.
A quick static check will help you find hot rolls before you load them onto your unwinder. To do a static check, use an electric fieldmeter to measure the field on the roll as you unwind about a quarter of the outer lap of film as shown in Figure 1.
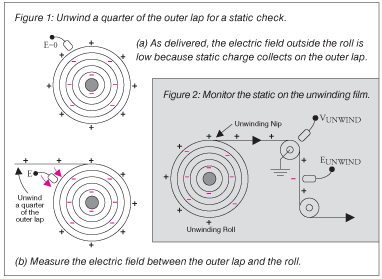
Here's how the static check works. In Figure 1(a), the master roll as delivered was wound with high static charge indicated by the eight “-” signs within the roll. However, during storage and transport, naturally occurring ions in the air along with some dust particles are attracted to the roll and build up on the outer lap, shown by the eight “+” signs. The charge on the outside of the roll just balances the static wound inside the roll. So, as delivered, this hot roll has a very low electric field on the outside. For the quick static check, we must remove the charge on the outside of the roll by unwinding about quarter of the outer lap. Measure the electric field between the unwound film and the roll as shown. If you measure a high electric field, or if you hear static crackling when you peel the film, you'll know that you have a hot roll.
The static check is a good qualitative measurement to see if a roll is hot. Now, let's get more quantitative and put some numbers on static so we can track performance with a control chart, set specifications, and verify that incoming material meets your needs. Monitor static on the film near the unwinder using an electric fieldmeter and an electrostatic voltmeter as shown in Figure 2. The fieldmeter measures EUNWIND on a film span as close to the unwinding roll as is reasonably possible. This measurement indicates the average static charge on both sides of the film. In Figure 2, EUNWIND will be low because the film has positive charge on one surface and negative charge on the other surface.
The voltmeter measures VUNWIND where the film is wrapped around an idler roller as close to the unwinding stockroll as is reasonably possible. VUNWIND indicates the static only on the exposed surface of the film. In Figure 2, VUNWIND will be highly positive because there is positive charge on the exposed surface of the film. lovehub
Electrostatic voltmeters and fieldmeters are complementary measurements. Used together, these two measurements provide you with complete information on the static present on the unwinding film. For example, write down the values for EUNWIND and VUNWIND at 25%, 50%, and 75% through the stockroll. Track the average (x-bar) and range (R) of the three values of EUNWIND on an x-bar/R control chart. Similarly, track the x-bar and R of VUNWIND on a second control chart. These charts will give you a visual picture of the “normal” performance for your incoming material, and you'll see spikes when you unwind a hot roll.
Prevent static problems in your operation caused by static on incoming material by doing a quick static check to find hot rolls. Monitor the static on the unwinding film using a fieldmeter and an electrostatic voltmeter. Using control charts of these measurements, you'll see the normal performance of your process and see spikes of high static from hot rolls. And, you'll know just where to set specifications on incoming materials to prevent static problems.
Static control expert Dr. Kelly Robinson, president of Electrostatic Answers, has 27+ years of experience in problem-solving and consulting. Contact him at 585-425-8158; kelly.robinson@electrostaticanswers.com; www.electrostaticanswers.com.