Featured Stories
-
Elevating Pouch Manufacturing with Pearl Technologies' Cutting-Edge Solutions
For manufacturers seeking efficiency, precision, and safety in pouch production, Pearl delivers unmatched innovation across three standout... -
Faster Product Composition Analysis Equals Better Quality Assurance
Near Instant Testing and Reduced Costs to be Found -
Methods to Precisely Measure Tension and Web Control
How to Control Automatically Within Set Parameters
News | New Products
-
Nobelus Launches Entry-Level Komfi® Thermal Laminator
FINISHING SOLUTIONS SUPPLIER OFFERS NEW JUNIOR 52 LAMINATING SYSTEM
-
Double E Group Mourns the Loss of Founder and Converting Industry Pioneer, Richard Edward Flagg
Double E Group announces with profound sadness the passing of its founder, Richard Edward “Ed” Flagg, on June 23, 2025. He was 85.
-
Convertech Brand to Fully Transition to Double E Group Same Team, Same Excellence, Unified Name
Double E Group has announced that Convertech, one of its subsidiaries and a trusted provider of core chucks and shaft solutions for the converting industry, will now operate solely under the Double E Group brand.
-
Pulse is Making Print Simple at Labelexpo Europe 2025
Narrow web ink specialist Pulse is Making Print Simple at Labelexpo Europe 2025, as it challenges flexo printers to rethink how they work and shows solutions that turn production bottlenecks into revenue generators.
-
ROTOCON to debut at Labelexpo Europe with three machine demonstrations
ROTOCON will make its Labelexpo Europe debut, exhibiting together with HS Machinery on stand 4D21.
-
At Interphex Japan, IL Group to Showcase Innovative Labeling Solutions and Contract Packaging Services
IL Group, a specialist in multifunctional labeling solutions for the pharmaceuticals and healthcare sectors
-
Revolutionizing Adherence: Clinical Trials Go Digital with Enhanced Key-Pak®
Keystone Folding Box Co., a leading provider of paperboard packaging solutions, has announced a strategic partnership with Med-Con Technologies
Expert Advice
Improving the Process
- Published: June 30, 2007, By By David Argent, Contributing Editor
Process Management
Over time the converting industry has seen many incremental improvements punctuated with periodic step changes in which the process has changed significantly to meet new Consumer Product Company (CPC) requirements. Trends include shorter run lengths, regional designs, special promotions, and quicker turnaround times.
These trends can have an adverse effect on performance measures in the pressroom, since set-up costs, downtime, substrate waste, and press return inks are being supported by fewer print impressions. At some point we will see diminishing returns where current converting practices are no longer capable of meeting CPC needs at acceptable levels of profit to the converter.
Annualized Material Balance—Multi-Press Printer | ||||||
---|---|---|---|---|---|---|
Scenario | Min. # Ink to Ink Up | Print Job | Print Colors | # Ink to Press | # Ink Consumed | # Ink Returned |
Base Line | 150 | 2,000 | 6 | 1,800,000 | 900,000 | 900,000 |
Run Length Reduced | 150 | 2,500 | 6 | 2,250,000 | 900,000 | 1,350,000 |
Sump Size Reduced | 100 | 2,500 | 6 | 1,500,000 | 900,000 | 600,000 |
Run Length Further Reduced | 100 | 3,000 | 6 | 1,800,000 | 900,000 | 900,000 |
Extra Color Introduced | 100 | 3,000 | 7 | 2,100,000 | 1,050,000 | 1,050,000 |
Some converter improvement projects now are in place with little possibility of success. An example: The above table is an annualized material balance example for a multi-press packaging gravure printer. As run lengths decrease, the system becomes overwhelmed with managing press returns. Reduction in sump size as a tactic eventually will be negated by shorter press runs and designs with more colors—and it goes on.
This is an extreme example to illustrate a point. Similar calculations can be made for any pressroom and also for the impact on substrate waste and loss of press utilization.
Four-color process inks can produce a wide range of colors, but spot colors are used to generate colors outside of the CMYK gamut. However, printing with spot colors means special inks must be blended, press cylinders and rollers must be cleaned and prepared for each job, and items with unique colors cannot be ganged in the same run.
Expanded color gamut systems such as Hexachrome and Opaltone now are receiving much more attention from packaging printers. Printing with six or seven standard colors offers efficiency benefits compared to printing all spot colors or with CMYK plus custom spot colors.
I have seen sheet-fed offset presses running packaging materials on paper substrates using Hexachrome CMYKOG ink sets. It is very impressive to see these same six inks pumped from the inkroom to the same decks to produce packaging featuring major CPC brand colors. In this case all participants in the color management workflow, including the end-user, had to be involved in making the process work.
There are, however, many unknown factors. Foremost is the ability to produce visually acceptable brand colors. Another concern is that it may be more expensive to build strong colors from expanded color gamut ink sets compared to custom blended spot color inks.
The digital press already has a place in producing contract proofs. PANTONE solid colors are simulated using CMYKOV inks said to give a wide color gamut in commercial digital printing with results close to the original PANTONE solid colors. Pockets of knowledge exist among various participants in the supply chain, and further development will require collaboration by all, possibly leading to a new business model for some areas of the converting industry.
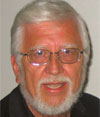
David Argent has 30+ years of experience in the converting industry. He specializes in process analysis and improvement with particular emphasis on ink and coating design and performance. Contact him at 636/391-8180; djvargent@sbcglobal.net.