Featured Stories
-
-
Elevating Pouch Manufacturing with Pearl Technologies' Cutting-Edge Solutions
For manufacturers seeking efficiency, precision, and safety in pouch production, Pearl delivers unmatched innovation across three standout... -
Faster Product Composition Analysis Equals Better Quality Assurance
Near Instant Testing and Reduced Costs to be Found
News | New Products
-
PACKZ 11 Launches with Industry-First RIP Integration
Plus extended CF2 format and automated support for 2-D Barcodes as Required by the Sunrise 2027 Initiative
-
Double E Group Acquires CAC, Further Enhancing its Strength in the Global Converting Industry
Double E Group, a global leader in converting components and web handling technology, has announced its acquisition of Converter Accessory Corporation (CAC)
-
Nobelus Launches Entry-Level Komfi® Thermal Laminator
FINISHING SOLUTIONS SUPPLIER OFFERS NEW JUNIOR 52 LAMINATING SYSTEM
-
Double E Group Mourns the Loss of Founder and Converting Industry Pioneer, Richard Edward Flagg
Double E Group announces with profound sadness the passing of its founder, Richard Edward “Ed” Flagg, on June 23, 2025. He was 85.
-
Convertech Brand to Fully Transition to Double E Group Same Team, Same Excellence, Unified Name
Double E Group has announced that Convertech, one of its subsidiaries and a trusted provider of core chucks and shaft solutions for the converting industry, will now operate solely under the Double E Group brand.
-
Pulse is Making Print Simple at Labelexpo Europe 2025
Narrow web ink specialist Pulse is Making Print Simple at Labelexpo Europe 2025, as it challenges flexo printers to rethink how they work and shows solutions that turn production bottlenecks into revenue generators.
-
ROTOCON to debut at Labelexpo Europe with three machine demonstrations
ROTOCON will make its Labelexpo Europe debut, exhibiting together with HS Machinery on stand 4D21.
Expert Advice
What's Really On the Surface?
- Published: October 31, 2005, By David J. Bentley Jr., Contributing Editor
PLC Probe Television or print advertisements for cleaning products sometimes will show a microscopic picture of what a supposedly clean surface looks like. Such pictures emphasize that the surface really is contaminated with germs, bacteria, and similar items that are too small for the naked eye to observe.
The substrates converters use are somewhat similar except converters usually do not worry about germs and bacteria. Rather, they must be aware of the possibility of dirt, grease, plasticizers, oil, etc., discussed in this column in August 2004. Besides the causes mentioned then, substrate surfaces are prone to cause problems because of items that are impossible for the naked eye to see.
The first one is treatment or the lack thereof. Hopefully everyone knows this is an extremely important consideration in a converting operation. Looking at the substrate rarely will indicate whether it has a treatment or not.
Since many polyolefins will not accept an adhesive, coating, primer, or ink without treatment, converters must know whether that treatment is present before proceeding to use the substrate. Test solutions and testing inks will indicate this. Because a treatment can dissipate with time, testing the substrate for treatment immediately before use is a definite requirement.
A substrate can become contaminated during an out-of-line converting operation. Suppose a converter coats a primer onto one side of a polyester film at a specified coating weight, runs it through an oven on the converting line, and then rewinds it immediately as it exits the oven. After storing this coated roll, the converter then runs the primer-coated polyester through an extrusion line so the extrudate contacts the primer side of the substrate. This is then rewound as a finished product. The operation in this case is out of line, because it uses two separate steps rather than a single step in which the converter immediately would apply the molten extrudate to the dried primer in one operation.
During the time the primer-coated substrate is in storage waiting for the second step of the operation, certain negative events can occur. First, the entire primer might transfer from the side of the substrate on which it adhered originally to the opposite side. Although this does not happen frequently, it is theoretically possible. If this were to occur, the extrudate would not adhere during the extrusion step because the primer now would be on the wrong side.
A more likely scenario is that something in the primer might migrate to the surface. The primer might contain low-molecular-weight components, a plasticizer, or some other incompatible material. Because of the incompatibility, this particular ingredient or ingredients will tend to migrate to the surface of the primer. Of course, this happens only when these incompatible ingredients are components of the primer. When they are present, their migration more likely will happen when the roll of primed substrate is subjected to lengthy storage or storage at an elevated temperature. Both temperature and time drive the incompatible ingredients toward the surface.
If this migration occurs, the extrudate being applied during the second step of the out-of-line operation does not contact the primer. Rather, it contacts the low-molecular-weight material, plasticizer, or other incompatible material that has accumulated at the surface. Thus, the extrudate probably will not adhere as it should, and the customer will find the resulting product to be unsatisfactory.
A similar phenomenon has occurred with contamination from rollers over which a substrate passes during a converting operation.
Obviously, this occurs only with rollers made from rubber or some composite material. Improperly made rollers can contain an ingredient that might migrate to the surface of the roller after a period. A substrate passing over the roller could wipe off the material that migrated. This modified surface then would cause a problem for any adhesive, coating, primer, ink, or resin that subsequently would contact it.
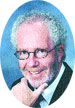
David J. Bentley Jr. is a recognized industry expert in polymers, laminations, and coatings with more than 30 years of experience in R&D and technical service. Contact him at dbentley@unm.edu.